Unleash the full potential with a vacuum press
Solid surface materials are true miracle materials that offer craft businesses almost limitless possibilities in terms of areas of application and processing options. A vacuum press is the best tool for users to fully take advantage of the materials potential.
Solid surface materials basically consist of polyester resin or acrylic resin as well as set natural materials such as aluminum trihydrate. Together, these components result in a non-porous, easy-care polymerized surface material that consists of a single mass. Its homogeneous structure makes it particularly versatile.
For users of a vacuum press, acrylic resin-bonded solid surface materials are of particular interest, as these – in contrast to polyester-bonded solid surface materials – can be thermally deformed particularly well.
Solid surface materials score with an enormous number of advantages, of which, depending on the application, always a different one comes first. As already mentioned, solid surface materials are ideal for deforming. No matter what they are used for, they find a versatile optical or functional task in every environment.
The material composition and quality bring several advantages. On the one hand solid surface materials are solid, very robust and extremely scratch, impact and wear resistant. They still inspire optically even after years. Due to the UV resistance also in the outdoor area. In addition, the material has a homogeneous structure. If scratches or damage should occur due to incorrect treatment, they can usually be easily sanded down and polished out. This homogeneity leads us straight to a very special and decisive advantage. Solid surface materials are non-porous. This, coupled with the possibility of being able to glue them completely seamlessly, results in a particularly hygienic surface that lasts a long time and is particularly easy to clean. Moisture cannot penetrate and bacteria and mold don't stand a chance. Solid surface materials are therefore suitable for both indoor and outdoor applications and wherever hygiene is a top priority. In addition, the material is particularly sustainable, recyclable and also ideal for allergy sufferers.
Solid surface materials are used in all shapes and colors, in bathrooms, kitchens, hospitals, laboratories, but also in numerous outdoor applications. Some transparent materials can even be backlit.
As already mentioned, vacuum presses offer the ideal opportunity to process solid surface materials. A vacuum press from Columbus allows its user to bring the solid surface material into many desired shapes.
The smooth and highly elastic membrane – heat-resistant up to +230° C – allows an extremely material-friendly processing without pressure points or scratches - even with a maximum pressure of 9t/m2 - because it adapts perfectly.
To heat up the material, Columbus has developed an external high-performance heating system, which is available in modular form. This can easily be placed under the vacuum table to save space.
When processing mineral materials, the thermal treatment before pressing is a critical factor. For this reason, Columbus deliberately installed a circulating air heating system. In contrast to conventional heating plates, which are not only very expensive and can often cause discoloration, especially with light-colored materials, a circulating air system guarantees very even, gentle heating. The large support surface with grating completes the system.
What are solid surface materials?
Solid surface materials basically consist of polyester resin or acrylic resin as well as set natural materials such as aluminum trihydrate. Together, these components result in a non-porous, easy-care polymerized surface material that consists of a single mass. Its homogeneous structure makes it particularly versatile.
For users of a vacuum press, acrylic resin-bonded solid surface materials are of particular interest, as these – in contrast to polyester-bonded solid surface materials – can be thermally deformed particularly well.
Properties and advantages of solid surface materials?
Solid surface materials score with an enormous number of advantages, of which, depending on the application, always a different one comes first. As already mentioned, solid surface materials are ideal for deforming. No matter what they are used for, they find a versatile optical or functional task in every environment.
The material composition and quality bring several advantages. On the one hand solid surface materials are solid, very robust and extremely scratch, impact and wear resistant. They still inspire optically even after years. Due to the UV resistance also in the outdoor area. In addition, the material has a homogeneous structure. If scratches or damage should occur due to incorrect treatment, they can usually be easily sanded down and polished out. This homogeneity leads us straight to a very special and decisive advantage. Solid surface materials are non-porous. This, coupled with the possibility of being able to glue them completely seamlessly, results in a particularly hygienic surface that lasts a long time and is particularly easy to clean. Moisture cannot penetrate and bacteria and mold don't stand a chance. Solid surface materials are therefore suitable for both indoor and outdoor applications and wherever hygiene is a top priority. In addition, the material is particularly sustainable, recyclable and also ideal for allergy sufferers.
Areas of application for solid surface material
Solid surface materials are used in all shapes and colors, in bathrooms, kitchens, hospitals, laboratories, but also in numerous outdoor applications. Some transparent materials can even be backlit.
Optimal processing using a vacuum press
As already mentioned, vacuum presses offer the ideal opportunity to process solid surface materials. A vacuum press from Columbus allows its user to bring the solid surface material into many desired shapes.
The smooth and highly elastic membrane – heat-resistant up to +230° C – allows an extremely material-friendly processing without pressure points or scratches - even with a maximum pressure of 9t/m2 - because it adapts perfectly.
To heat up the material, Columbus has developed an external high-performance heating system, which is available in modular form. This can easily be placed under the vacuum table to save space.
When processing mineral materials, the thermal treatment before pressing is a critical factor. For this reason, Columbus deliberately installed a circulating air heating system. In contrast to conventional heating plates, which are not only very expensive and can often cause discoloration, especially with light-colored materials, a circulating air system guarantees very even, gentle heating. The large support surface with grating completes the system.
Find out more at Pioneer, the unique vacuum press modular system
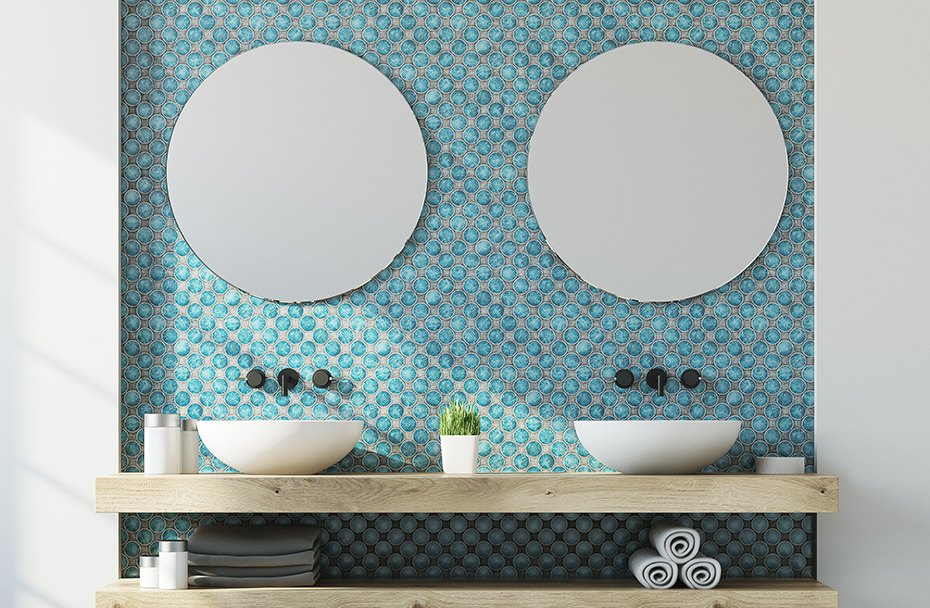
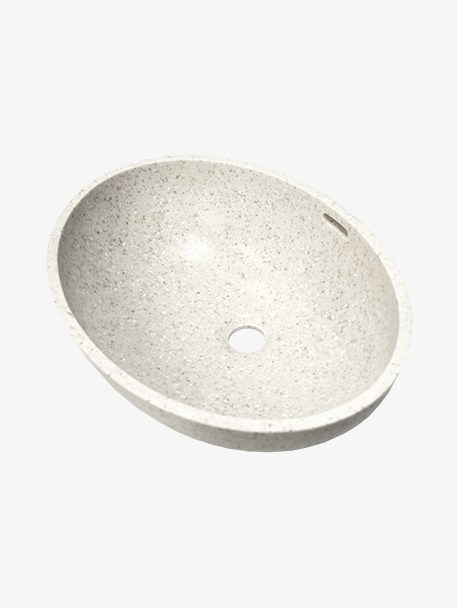
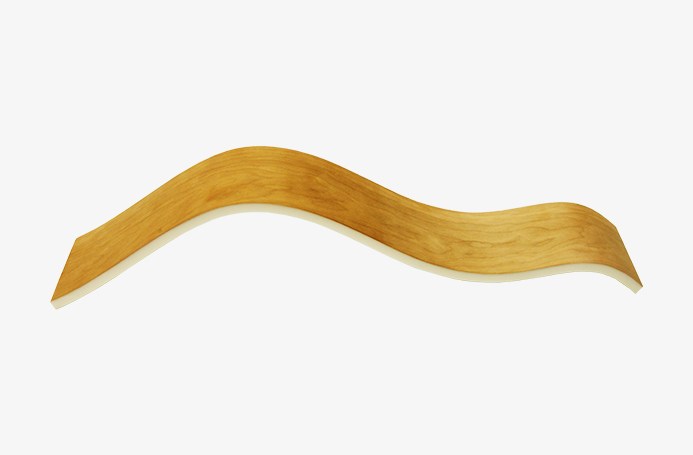
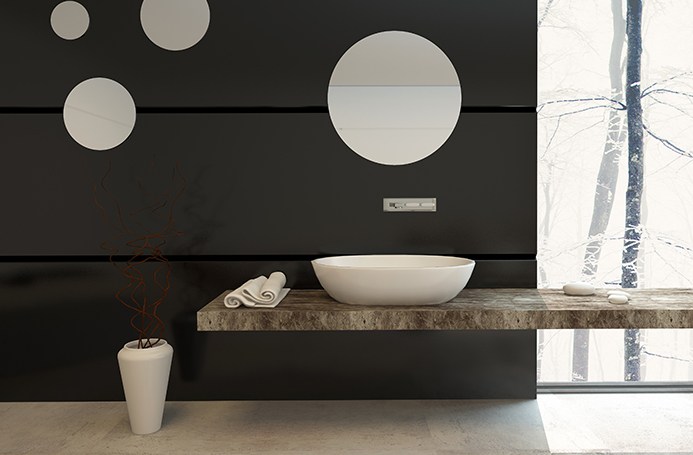
Interest?
If you would like to know more about the possibilities of PIONEER modular system, we would be happy to provide you with more information!
Thank you very much for your inquiry!
We will get back in touch with you.
We will get back in touch with you.
INTERESTING BLOG ARTICLE
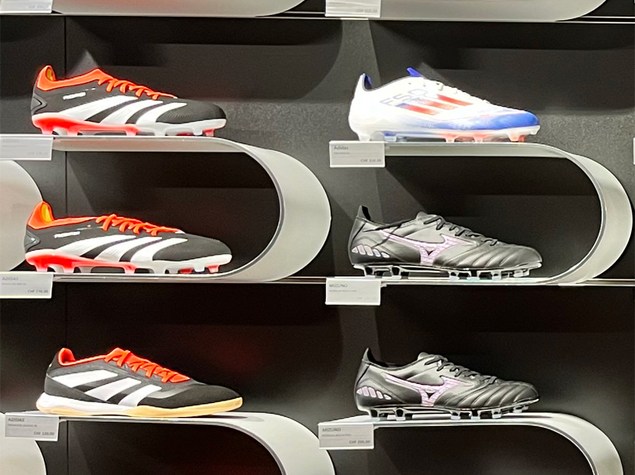
Realising Visions
Swiss Precision Meets Creative Design
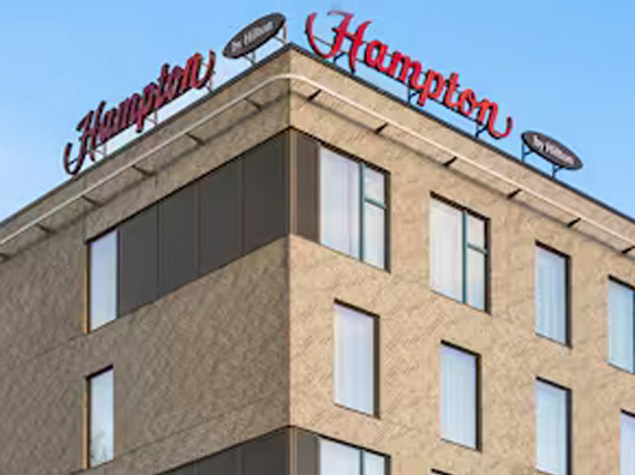
Tailor-made perfection in Estonia
Haapsalu Uksetehase AS Manufactures Doors for Hampton by Hilton
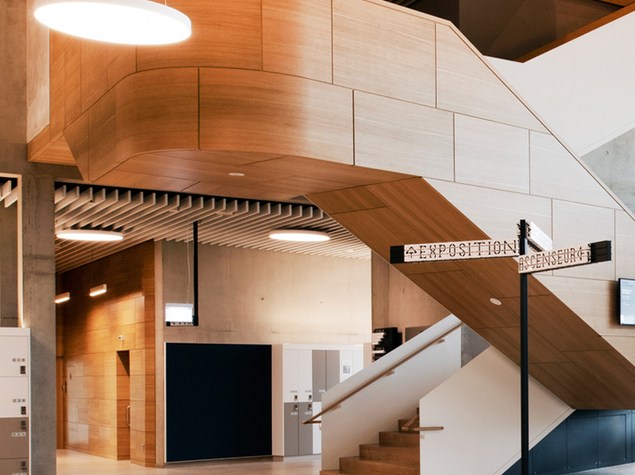
Premium Interior Fittings and Yacht Furnishings
A Vacuum Press has supported Der Ernzerhof for many years
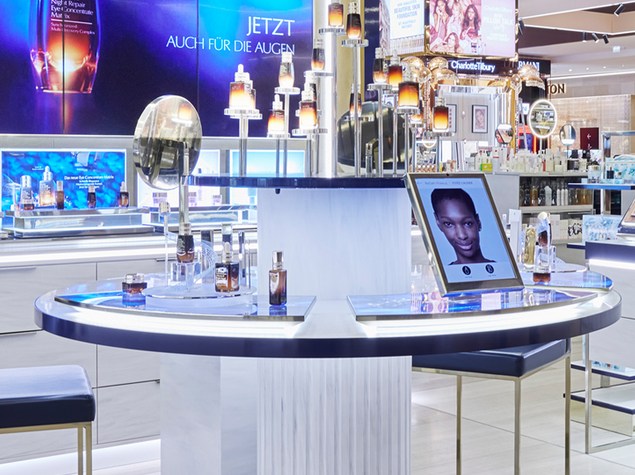
Outstanding Shopfitting with Vacuum
"außerdem" utilizes the advantages of a vacuum press by Columbus
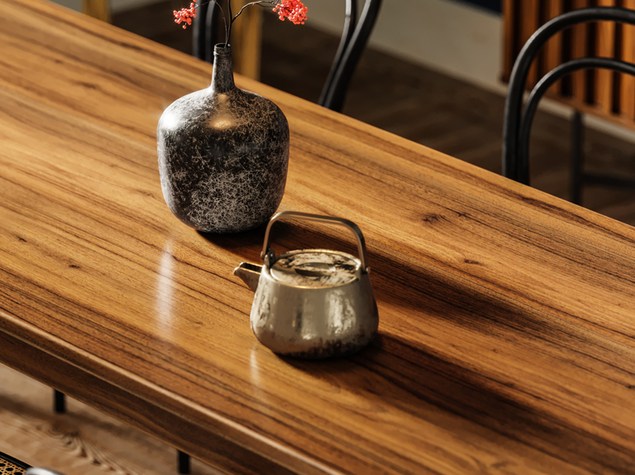
Flat veneering with vacuum
The use of a vacuum press as a veneer press
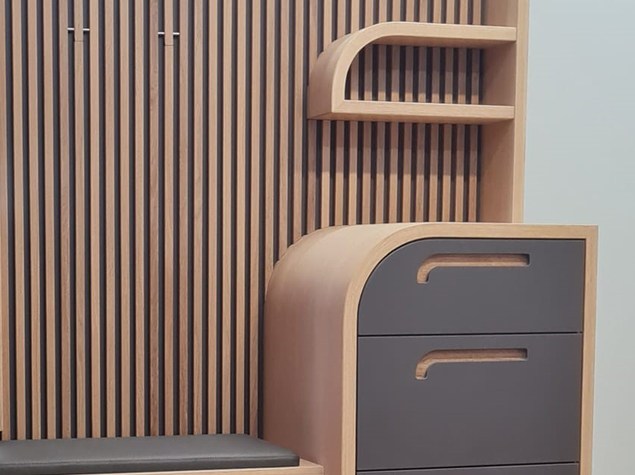
Masterful craftsmanship
The Wardrobe for the Master Carpenter Exam
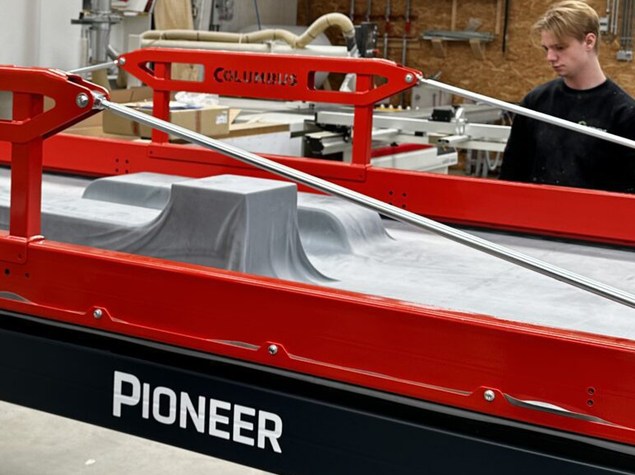
“It presses both flat and curved shapes”
Clairhout Interieur: A Revolution in Interior Design
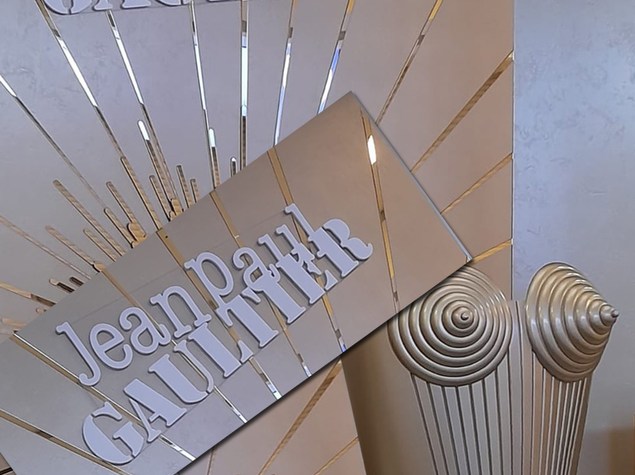
Columbus customer creates artistic masterpiece
Advertisement for Jean Paul Gaultier in Santiago de Chile

Beautiful Gift Idea
My Esel – exceptional bicycles & e-bikes
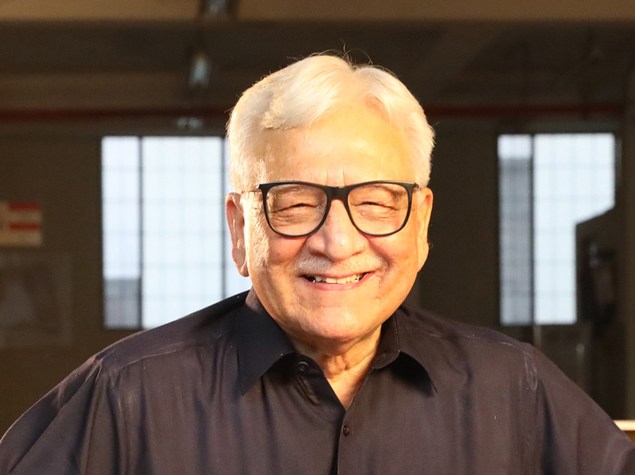
Curving the Impossible with Columbus
Interwood sets new standards with the press
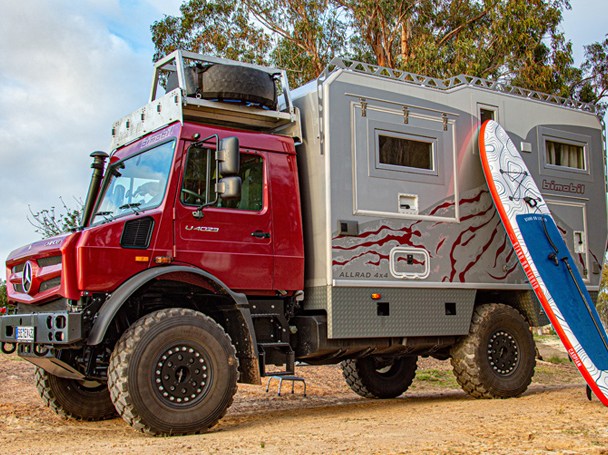
Infinity for bimobil motorhomes
Large-scale perfection for high-gloss paint
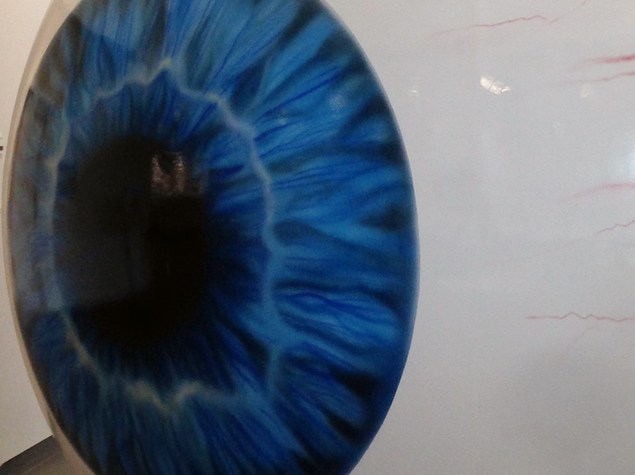
Precession and art from vacuum
Impressive eye model for the university clinic
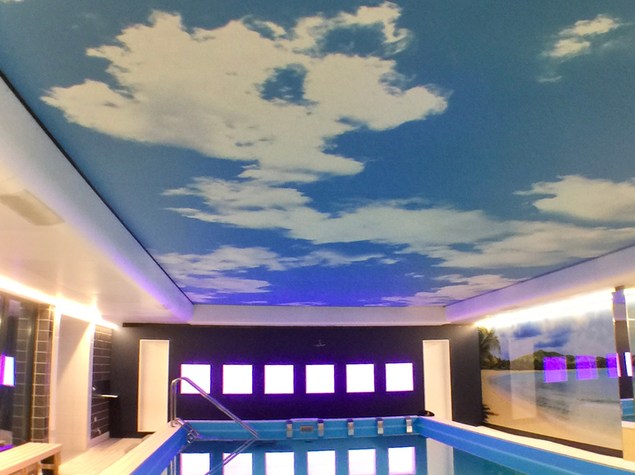
From the fruit bowl to the ceiling construction
The possible applications of a vacuum press
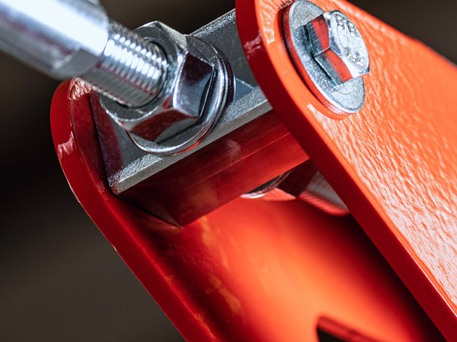
The Columbus Pressure Shifting Tool
So that natural rubber does not deform steel
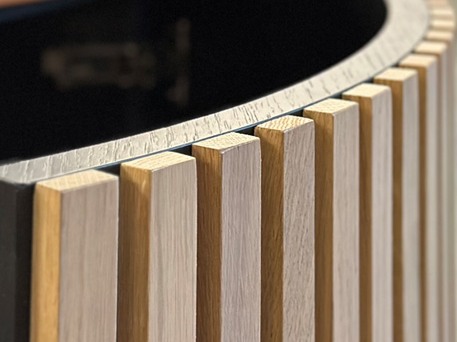
Kempa from Belgium invests in 2 vacuum presses
Round & curved shapes for modern interior design
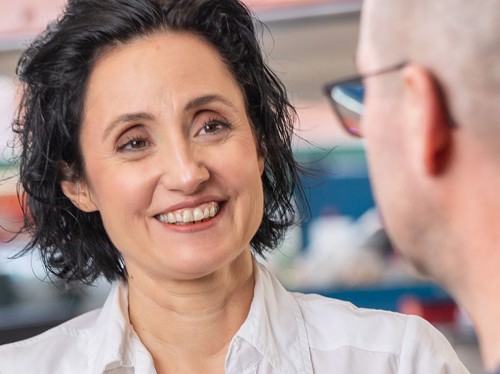
A patent for the modular system
Everyone said it doesn't work - I believed in it
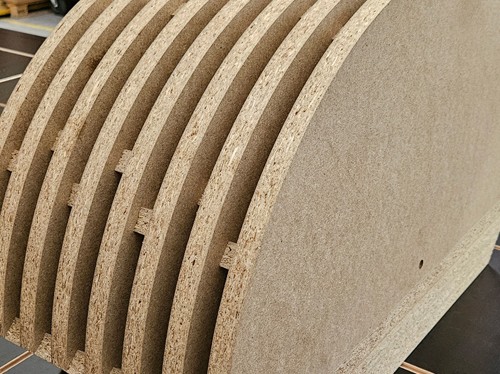
Columbus: Tips and Tricks from Practice
Mold making for mold bonding with vacuum
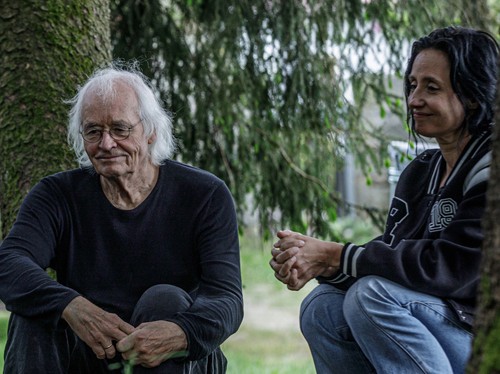
A look behind the scenes at Columbus
Thank you Dad, for a wonderful journey with you
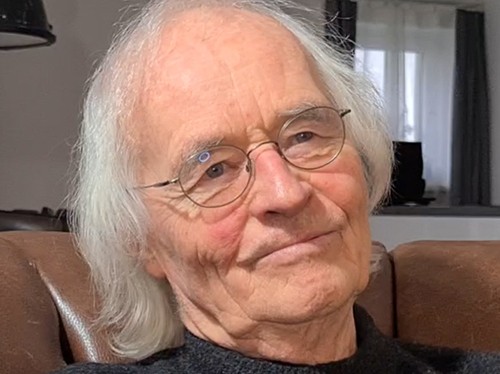
A look behind the scenes at Columbus
Günther Vetter - the invention of the vacuum bag
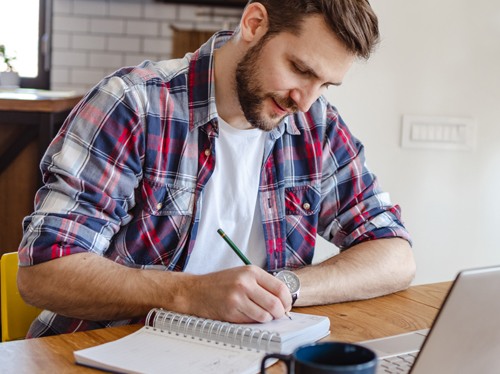
Protect your employees and your company
EU-mandated training for PUR hot melt adhesives
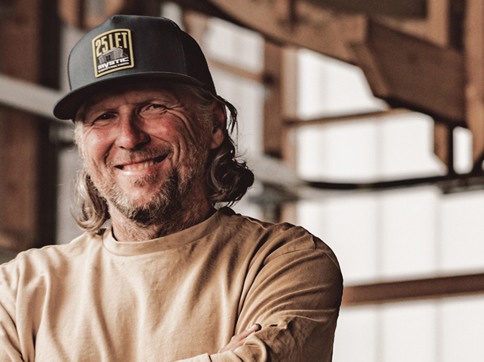
Skateboard ramps with the vacuum press Pioneer
Andreas Schützenberger does great things
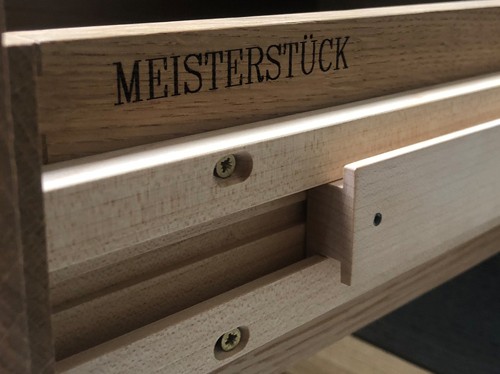
Vacuum bag: ZOSIA by Robert Nößler
His masterpiece with nostalgia and a secret
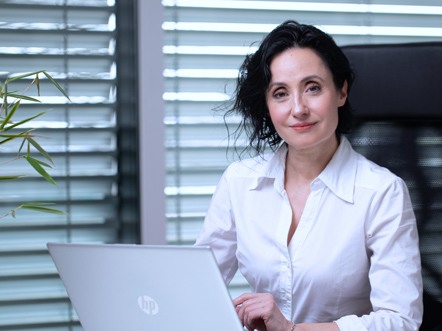
What are the benefits of a vacuum press?
Not only to cover curved workpieces and veneer

Report: International Fair in May 2023
Great success at the LIGNA in Hanover
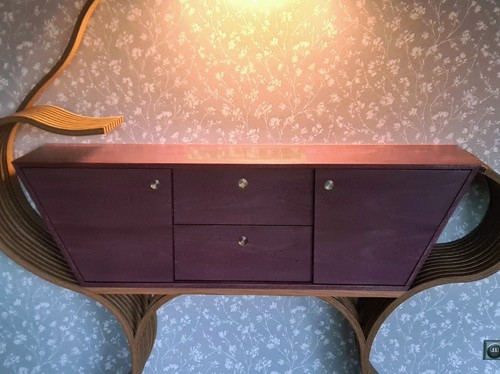
Vacuum bag: Modern Drop by Lars Hackl
Layer bonding for the next masterpiece
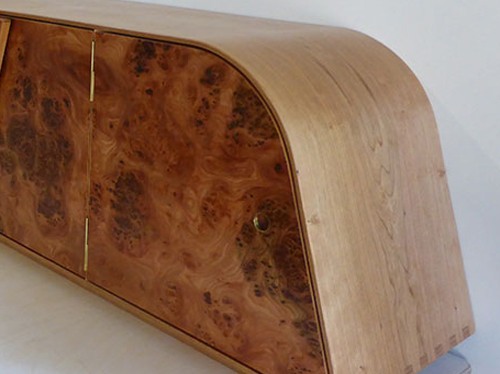
Vacuum bag: masterpiece by Tommy Kairat
First-class form veneering with Vacuflex
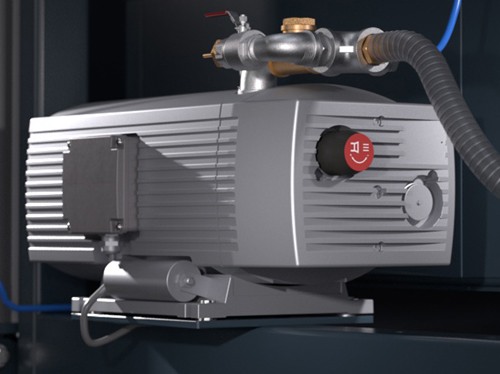
Vacuum pumps: an objective comparison
Columbus shows the advantages of dry runners
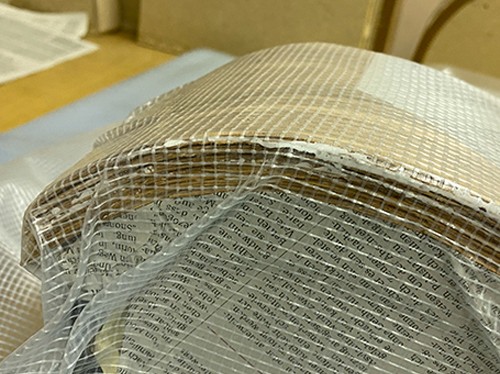
Free creativity in the creating process
Students from the Waldorfschule Mainz
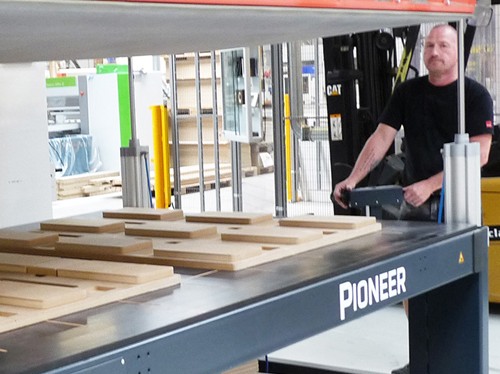
1.5 weeks instead of 6 weeks production time
Precisely curved fronts of the DALI speakers
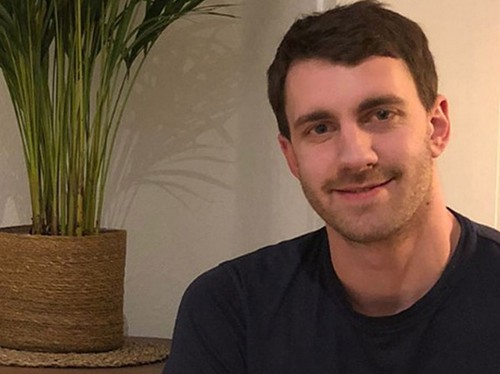
Vacuum bag: Markus Kramer's masterpiece
His vision brings the French past into the present
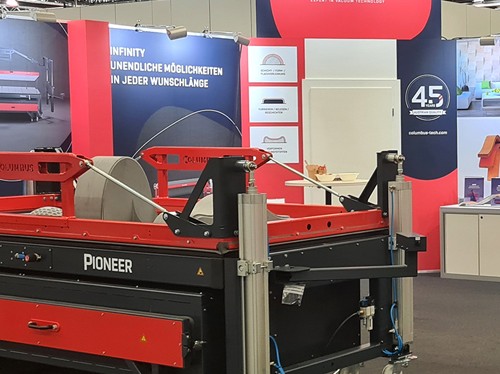
That was the Holz-Handwerk 2022
PIONEER and MOVE: Spectacular success at the fair
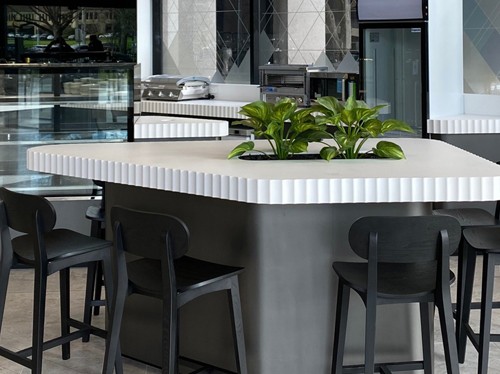
The magic lies in the perfect details
LL Installations creates high-quality accents
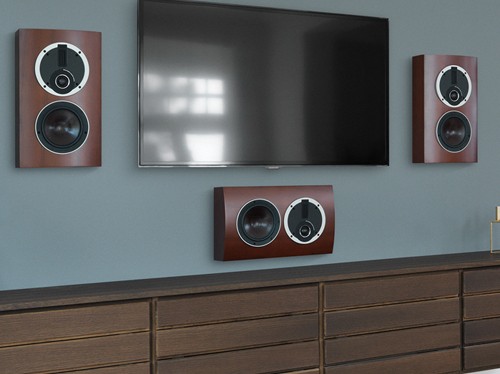
Handmade speakers from Denmark
One million satisfied DALI customers in over 70 countries
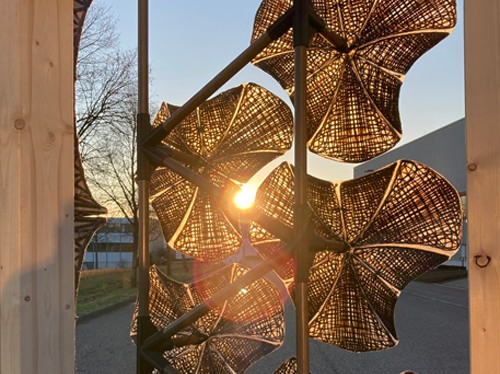
Columbus & University of Stuttgart
Artworks - Innovation meets Science
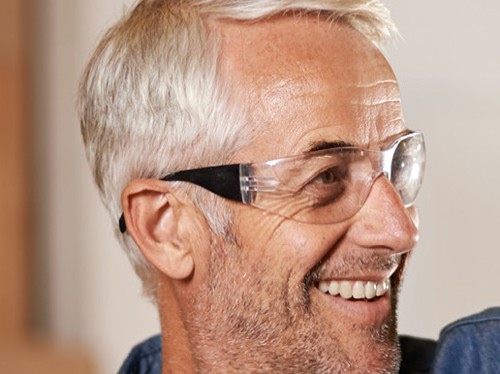
Independence from suppliers
6 Reasons to buy a Vacuum Press from Columbus
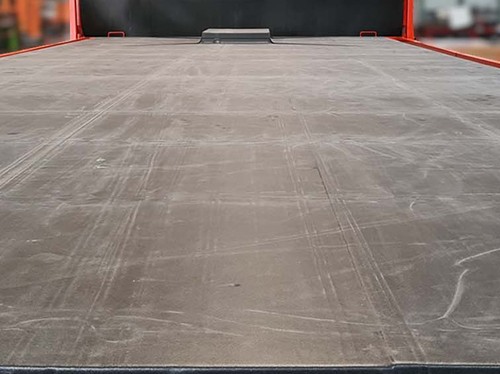
The Birth of Infinity Vacuum Press
Flexstone produces large parts for houseboats
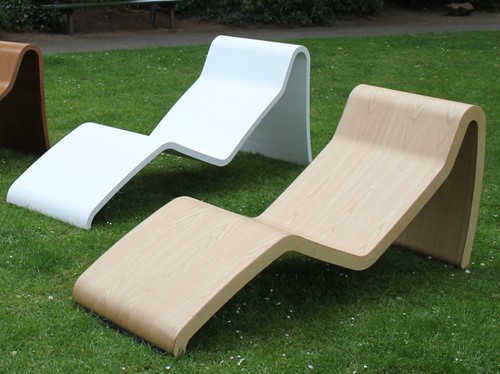
Sound loungers - feel the music
Magnus Hoffmann has developed something creative
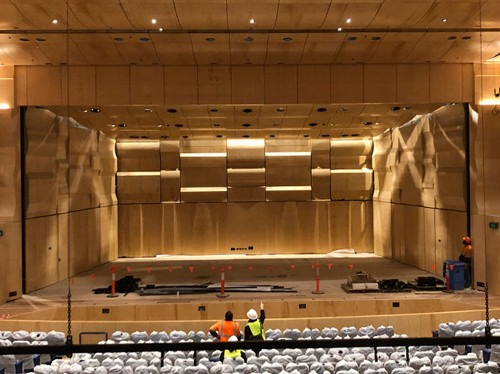
Excellence as far as the eye can see
Acoustic panels for the Leonardian Center in Australia
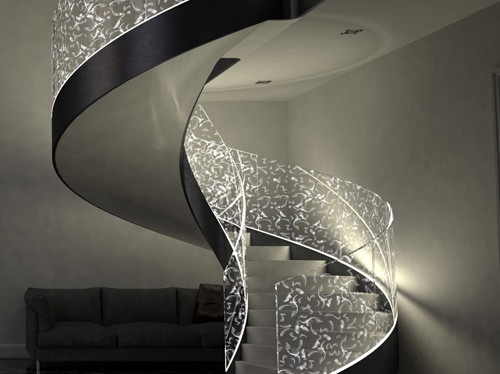
A dazzling cooperation between two pioneers
Vacuum - Acrylic glass - Unlimited possibilities
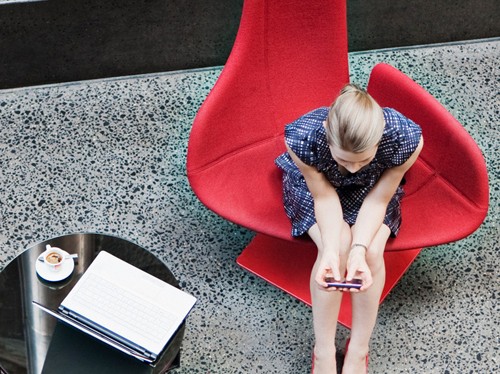
NOW: Individual. Exceptional. Unique.
Vacuum: Best performance from batch size 1
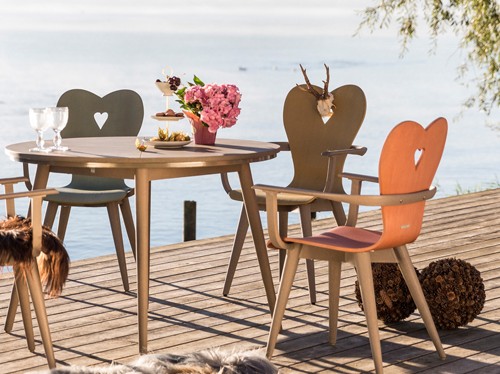
A compound better than wood
Resysta: Design meets sustainability
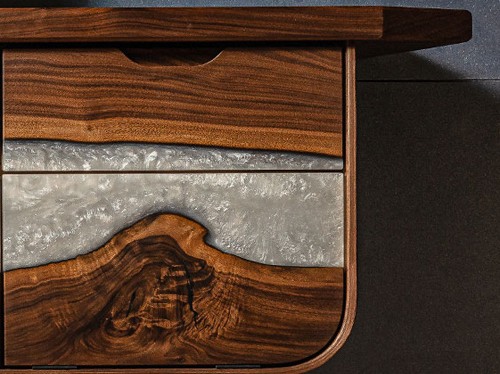
Vacuum bag: White River by Jannik Otte
Masterpiece as an eye-catcher for the entrance area
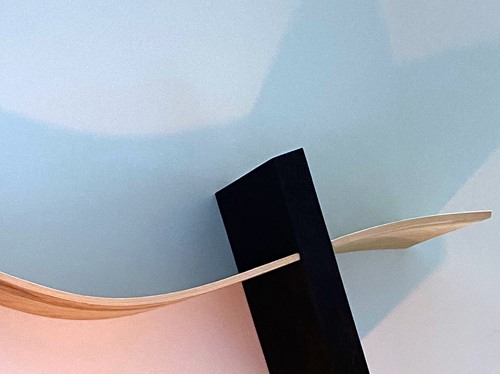
Young creativity conquers the world
Fascinating - these are students - not carpenters
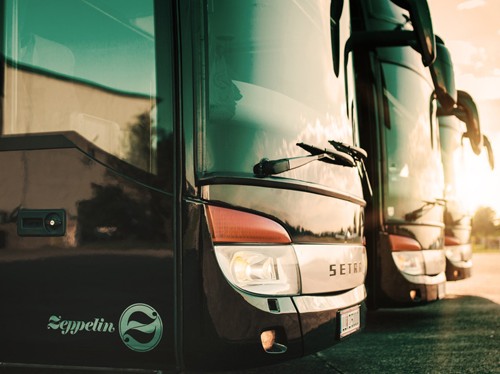
Full speed ahead with a vacuum press
Tour buses for the biggest stars in the world
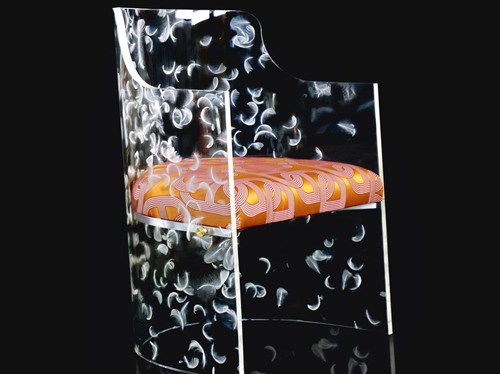
World premiere: acrylic glass chair
Customer Zöllner manufactures for Acrylic Couture
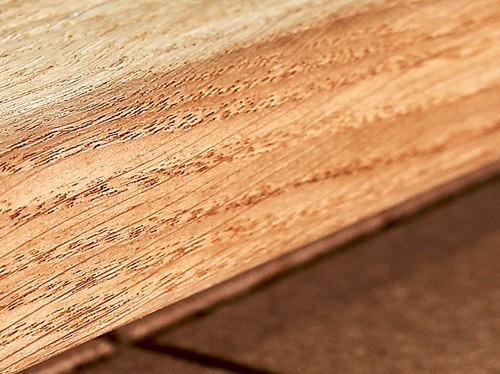
Columbus makes the impossible possible
VIDEO: Seamless veneering in just a few working steps
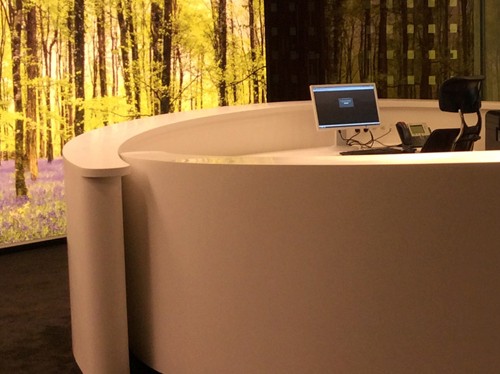
Columbus forms Kerrock in Belgium
An exceptional design future with vacuum presses
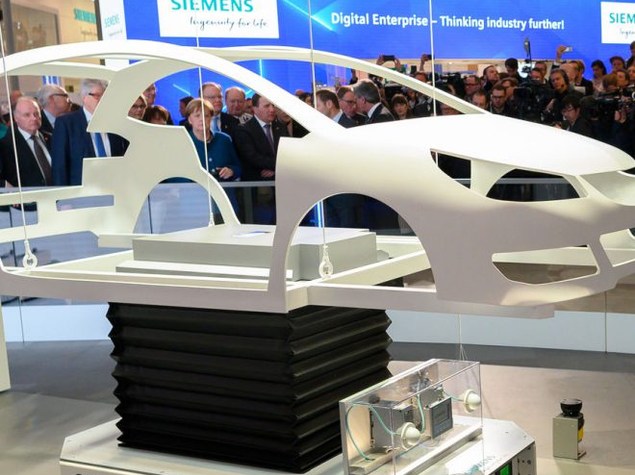
Exhibition builder Prager manufactures for Siemens
An innovative exhibition stand based on vacuum
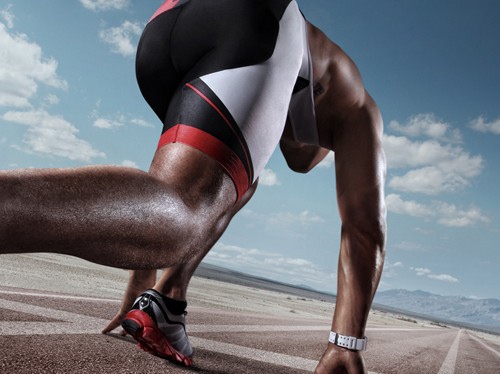
New times bring new opportunities
Conquering existing markets with new applications
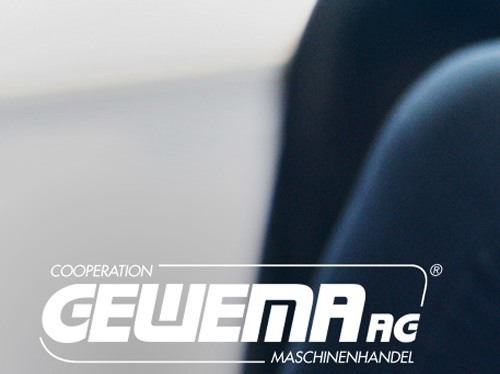
Columbus expands its global dealer network
GEWEMA membership for Columbus Vacuum Presses
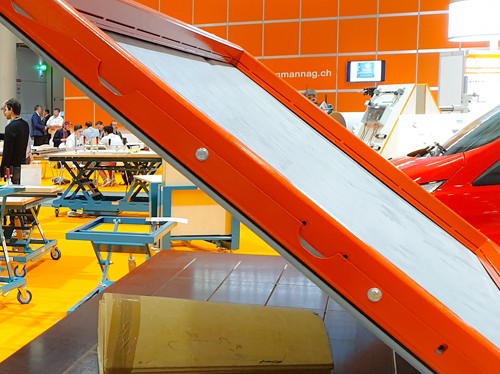
That was the Holz 2019 in Basel
Columbus and the great Swiss carpenters
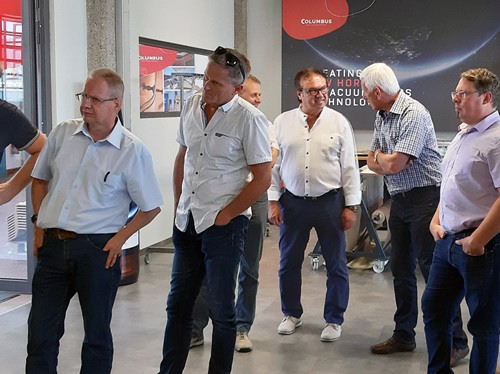
Cooperation with Schachermayer
Columbus receives another strong partner
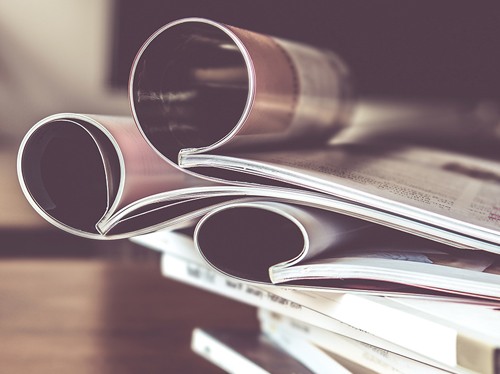
Press: People talk about Columbus
What is published in professional circles about us
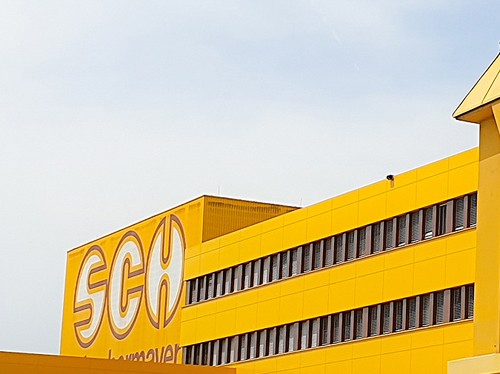
MEETING POINT NOBLE VENEER
Visiting the Schachermayer company
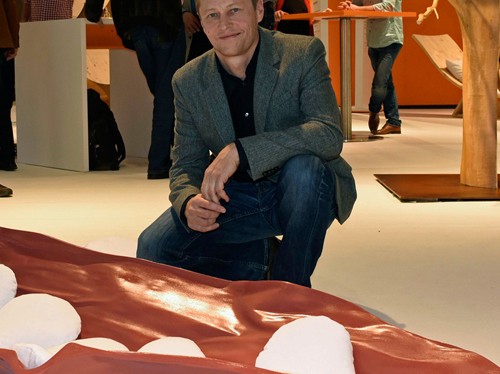
An Honor through Vacuum Technology
A chili as a creative lounge furniture is the winner
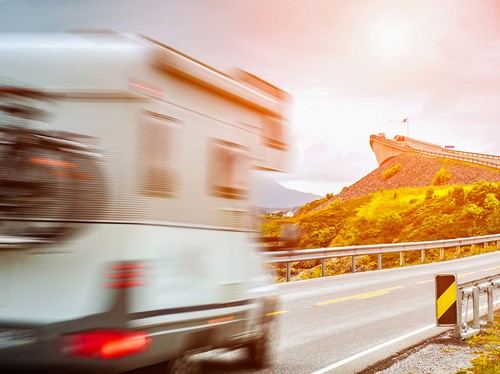
Hymer - a success story with vacuum
The well-known producer works with Columbus
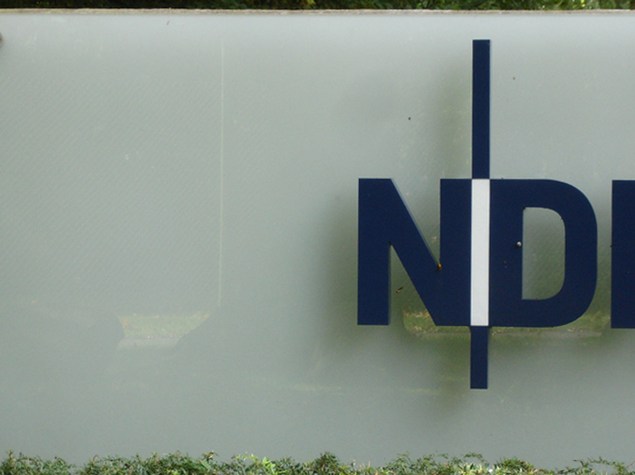
The NDR works with a vacuum press
The Tagesschau desk was produced with Columbus
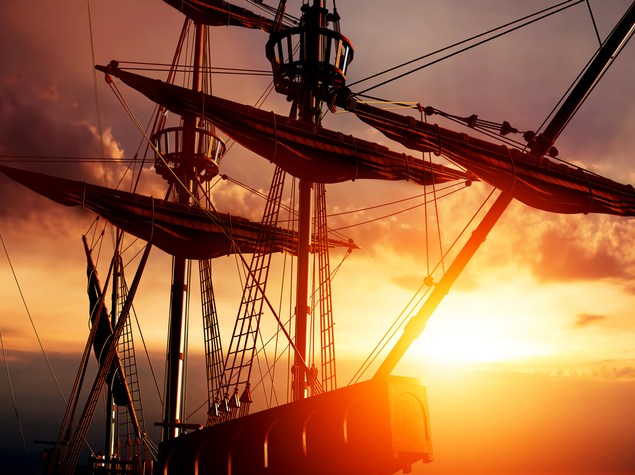
Why we are called what we are called
What Christopher Columbus has to do with Columbus