Practical tips and tricks
Pressing with vacuum is different from pressing with clamps, veneer presses or other machines. The digital master manual provides you with all the information you need for every vacuum press from Columbus. Here we have summarized the most important things for you:
With conventional presses, the pressing pressure occurs from two sides. However, when vacuum pressing you have to think differently, here the pressing pressure is even ALL SIDES. For this reason, stencils must be closed on all sides, including the BOTTOM SIDE.
A pressing pressure of just under kg/cm² sounds like little at first, but if it acts on a workpiece from all sides, the resulting forces should not be underestimated and can, for example, cause a less stable stencil to implode.
For larger radii (and thicker layers), the distance between the clamps (ribs) of the template can be 60 to 80 mm. For smaller radii and thinner layers, this distance must be reduced accordingly, otherwise waves can form in the workpiece.
To increase stability, transverse reinforcement of the template is required for taller workpieces.
The distance from the workpiece to the membrane frame or to the next workpiece should be approximately ½ the height of the workpiece. Example: a workpiece with a height of 20 cm should have a distance of 10 cm from the membrane frame on all 4 sides.
During the pressing process, workpieces that are too high or too large can damage the membrane or cause incorrect air to be drawn in (no vacuum is created). The membrane frame should be able to close without applying much force.
Which shapes can be pressed depends primarily on the material and the thickness of the layers used. Bendable plywood and slotted panels (see below) are particularly suitable for form gluing. Otherwise: the smaller the radius, the smaller the layer thickness.
In order to protect the membrane from over-stretching or tearing, very tall workpieces should not fall vertically where no pressing pressure is required. An allowance (e.g. made of Styrofoam) should be included here (see picture).
If the pressing pressure is required on a steep or vertical side, it must be ensured that the membrane can expand below the mold by at least 70 mm. This ensures a high side pressure.
To prevent the layers from slipping, they should be secured with adhesive tape.
Sharp corners and edges must be avoided in order not to damage workpieces and membranes. If this is not possible, the membrane must be protected from mechanical damage with felt or fleece.
Attention: an open template, sharp HPL edges or unrecessed fastening material can destroy a membrane within seconds.
Press pressure from ALL sides
With conventional presses, the pressing pressure occurs from two sides. However, when vacuum pressing you have to think differently, here the pressing pressure is even ALL SIDES. For this reason, stencils must be closed on all sides, including the BOTTOM SIDE.
A pressing pressure of just under kg/cm² sounds like little at first, but if it acts on a workpiece from all sides, the resulting forces should not be underestimated and can, for example, cause a less stable stencil to implode.
For larger radii (and thicker layers), the distance between the clamps (ribs) of the template can be 60 to 80 mm. For smaller radii and thinner layers, this distance must be reduced accordingly, otherwise waves can form in the workpiece.
To increase stability, transverse reinforcement of the template is required for taller workpieces.
Size of the workpieces/stencil
The distance from the workpiece to the membrane frame or to the next workpiece should be approximately ½ the height of the workpiece. Example: a workpiece with a height of 20 cm should have a distance of 10 cm from the membrane frame on all 4 sides.
During the pressing process, workpieces that are too high or too large can damage the membrane or cause incorrect air to be drawn in (no vacuum is created). The membrane frame should be able to close without applying much force.
Possible forms
Which shapes can be pressed depends primarily on the material and the thickness of the layers used. Bendable plywood and slotted panels (see below) are particularly suitable for form gluing. Otherwise: the smaller the radius, the smaller the layer thickness.
Vertically sloping workpieces
In order to protect the membrane from over-stretching or tearing, very tall workpieces should not fall vertically where no pressing pressure is required. An allowance (e.g. made of Styrofoam) should be included here (see picture).
If the pressing pressure is required on a steep or vertical side, it must be ensured that the membrane can expand below the mold by at least 70 mm. This ensures a high side pressure.
Fixing the layers
To prevent the layers from slipping, they should be secured with adhesive tape.
Protection of the membrane
Sharp corners and edges must be avoided in order not to damage workpieces and membranes. If this is not possible, the membrane must be protected from mechanical damage with felt or fleece.
Attention: an open template, sharp HPL edges or unrecessed fastening material can destroy a membrane within seconds.
In summary: vacuum presses offer an incredibly wide variety of possibilities - but never underestimate the power of the vacuum when implementing your ideas :-)
Further information: PIONEER, the patented modular system
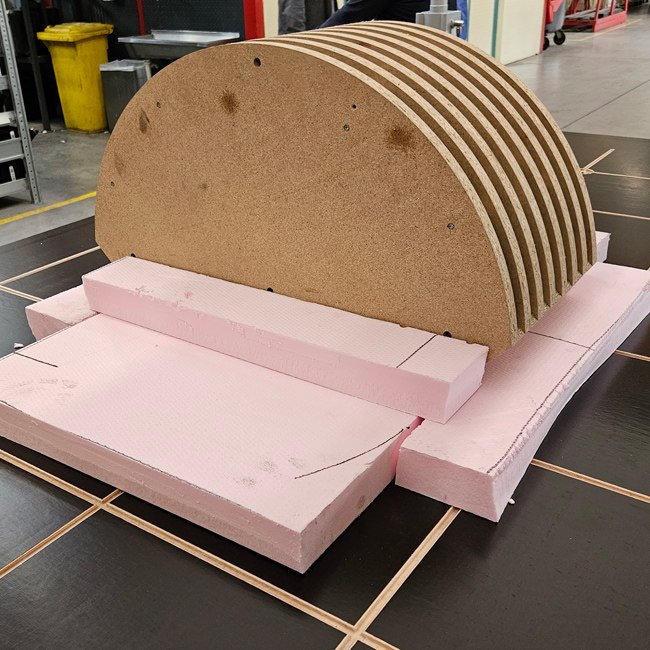
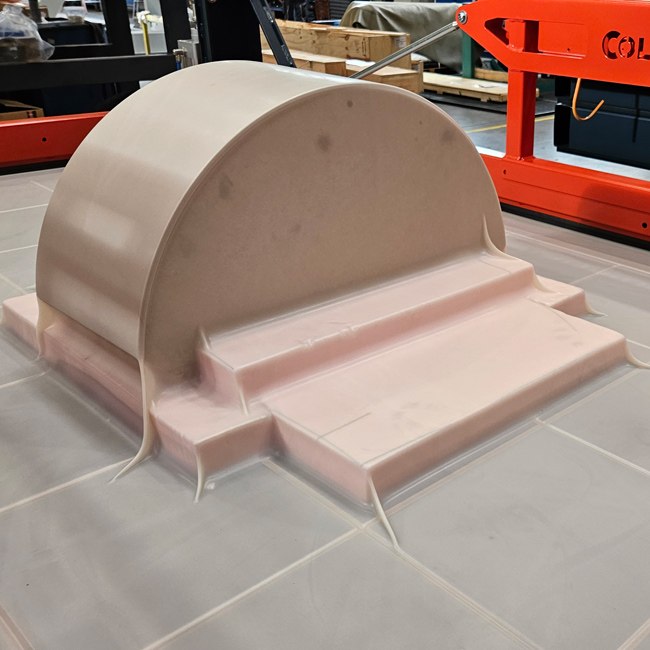
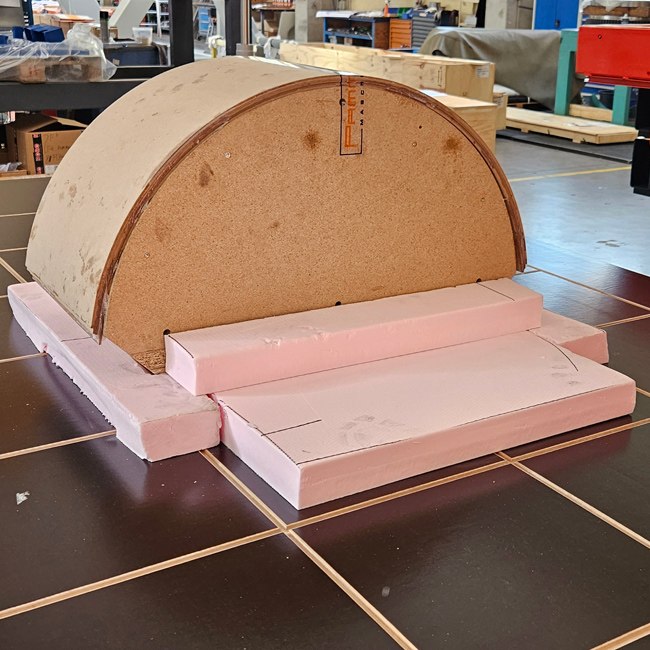
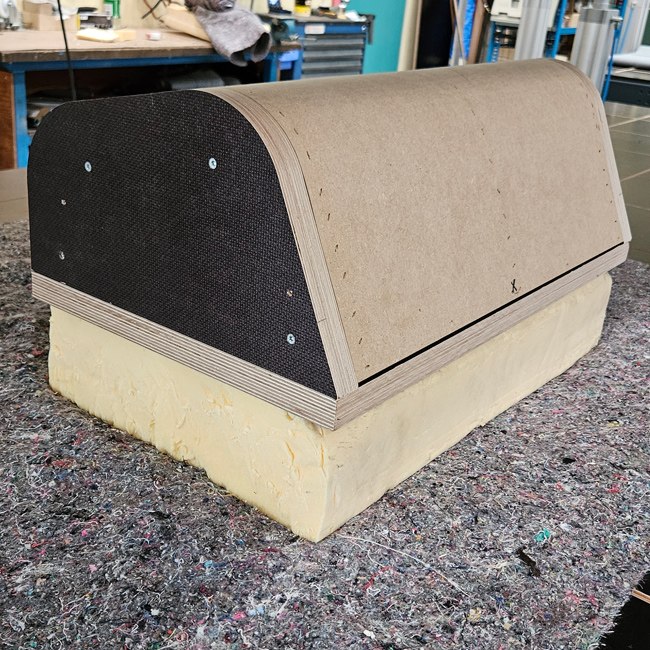
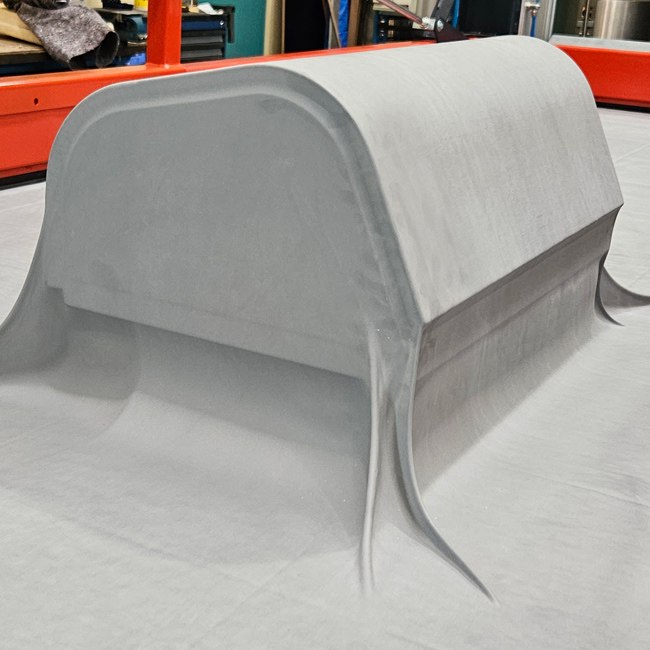
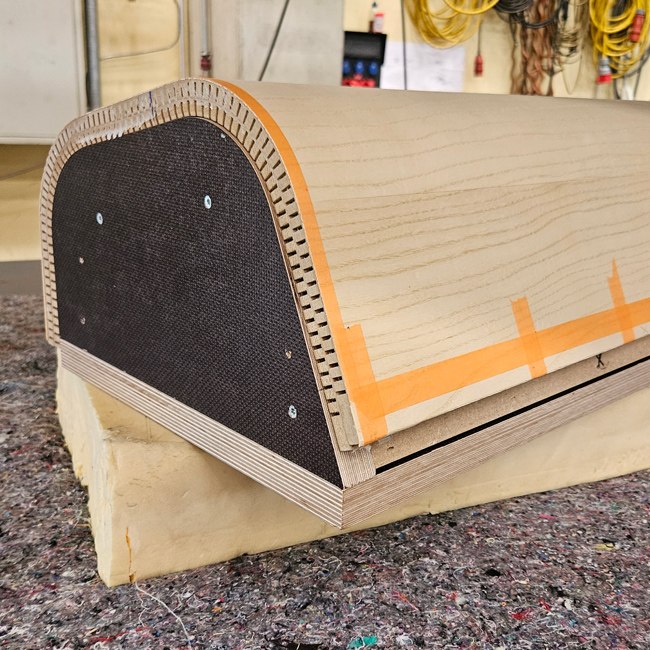
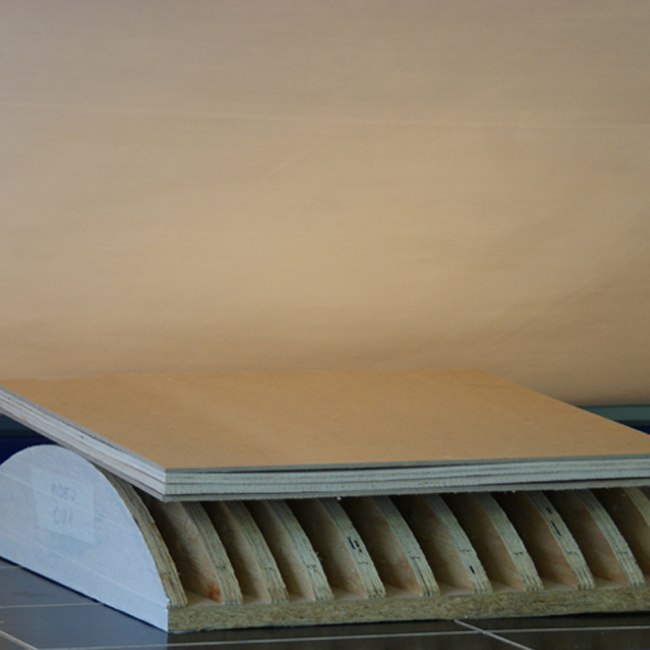
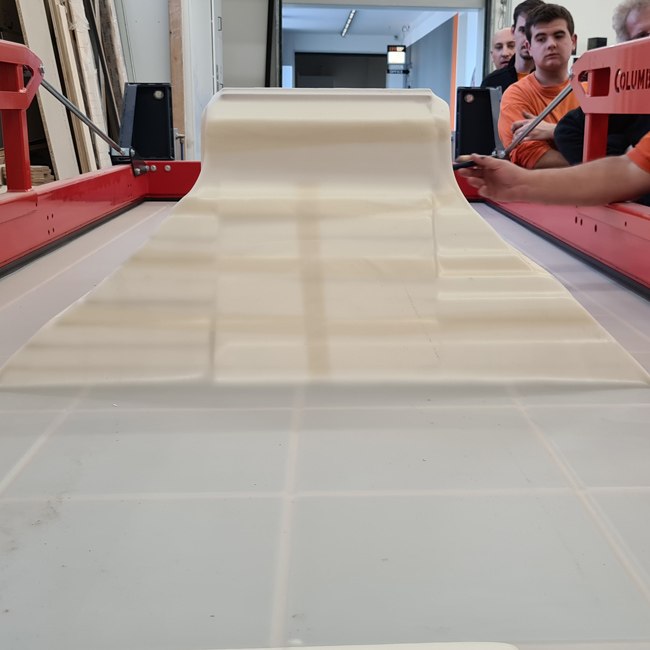
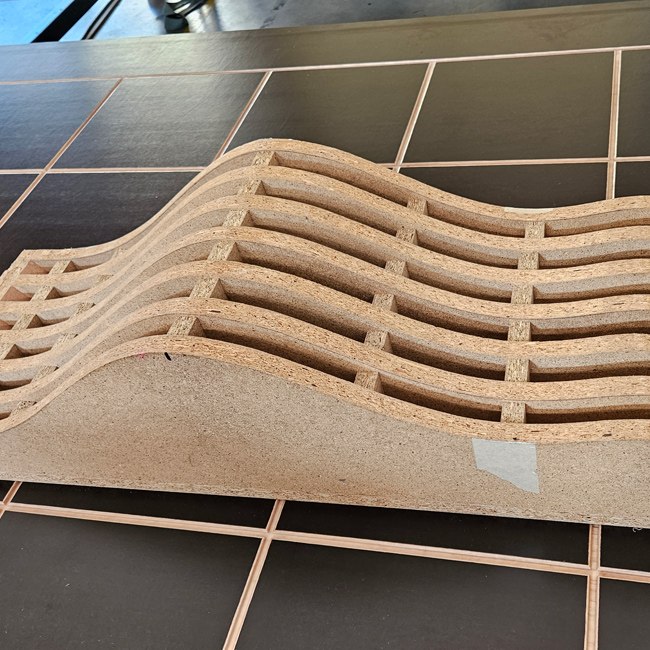
Interested in a modern VACUUM PRESSES?
We would be happy to inform you about your options, all versions, prices, etc.
Thank you very much for your inquiry!
We will get back in touch with you.
We will get back in touch with you.
INTERESTING BLOG ARTICLE
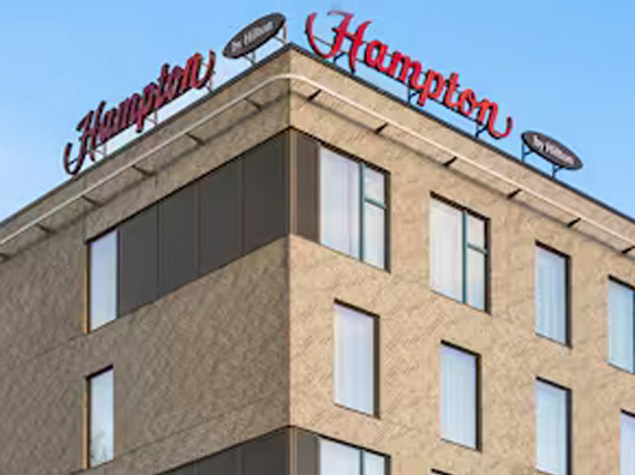
Tailor-made perfection in Estonia
Haapsalu Uksetehase AS Manufactures Doors for Hampton by Hilton
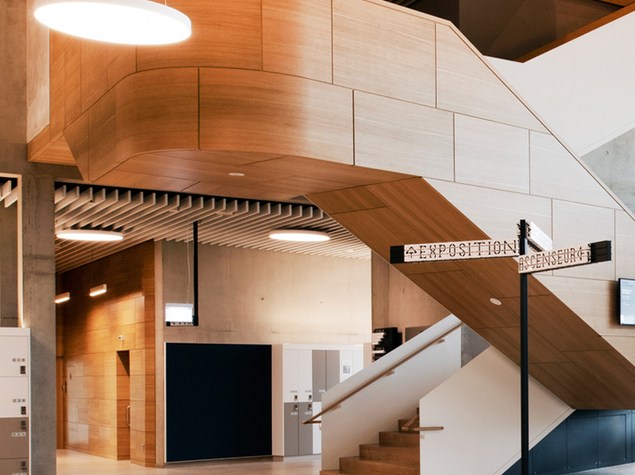
Premium Interior Fittings and Yacht Furnishings
A Vacuum Press has supported Der Ernzerhof for many years
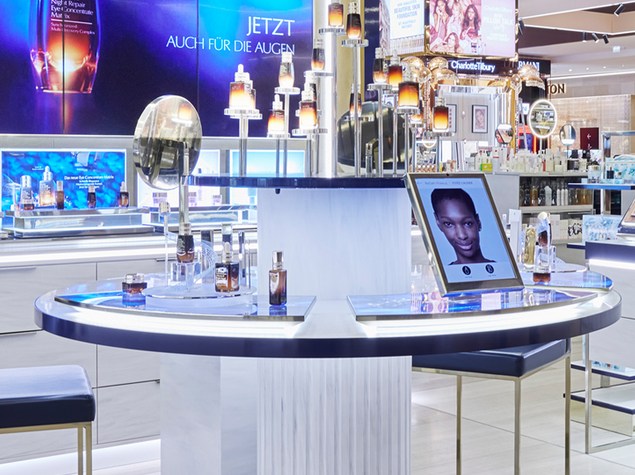
Outstanding Shopfitting with Vacuum
"außerdem" utilizes the advantages of a vacuum press by Columbus
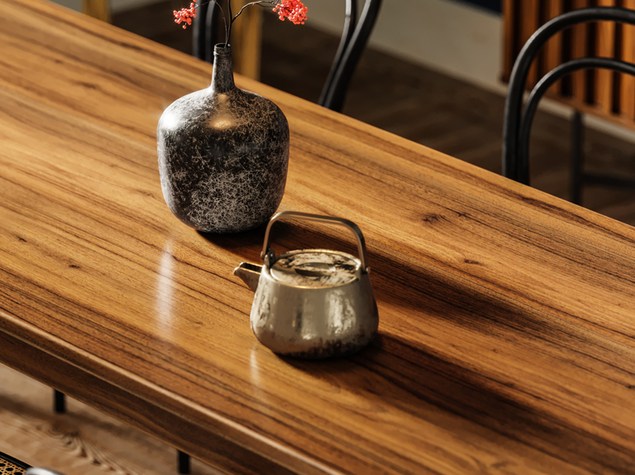
Flat veneering with vacuum
The use of a vacuum press as a veneer press
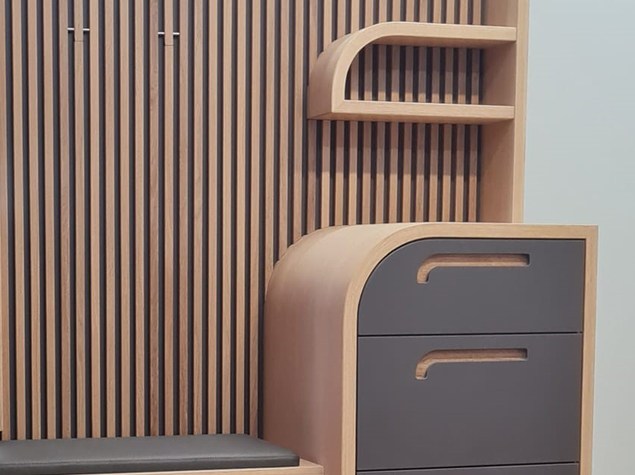
Masterful craftsmanship
The Wardrobe for the Master Carpenter Exam
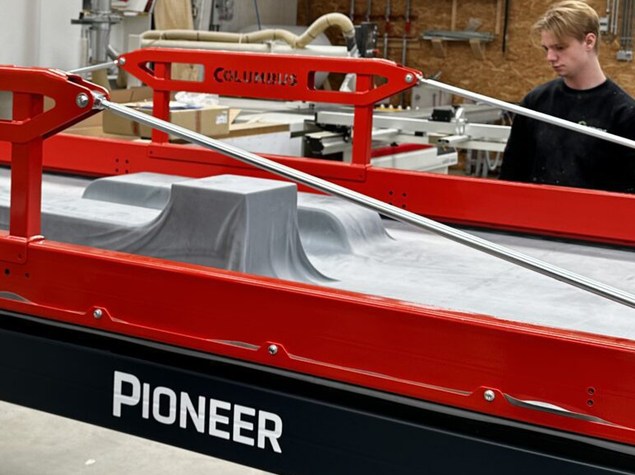
“It presses both flat and curved shapes”
Clairhout Interieur: A Revolution in Interior Design
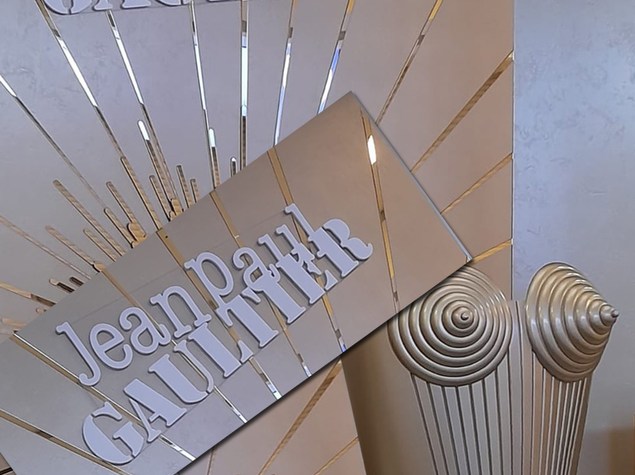
Columbus customer creates artistic masterpiece
Advertisement for Jean Paul Gaultier in Santiago de Chile

Beautiful Gift Idea
My Esel – exceptional bicycles & e-bikes
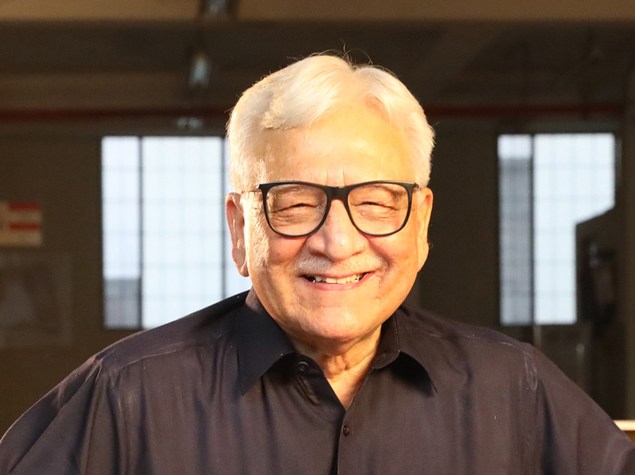
Curving the Impossible with Columbus
Interwood sets new standards with the press
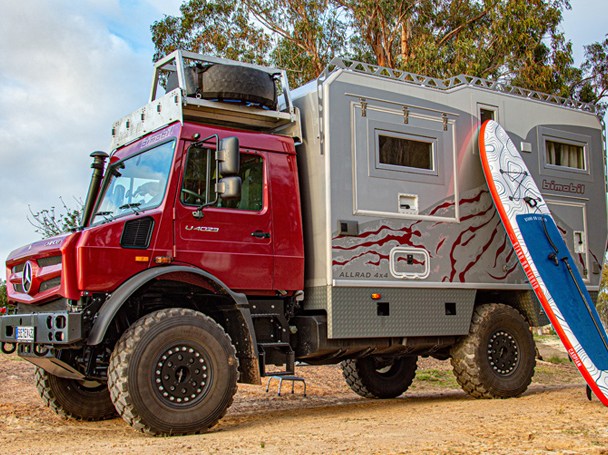
Infinity for bimobil motorhomes
Large-scale perfection for high-gloss paint
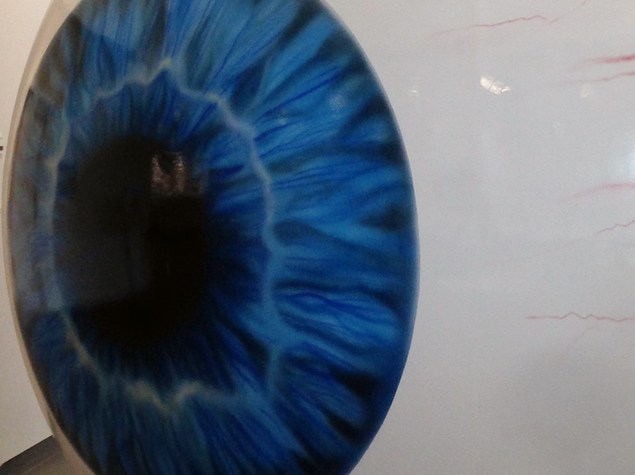
Precession and art from vacuum
Impressive eye model for the university clinic
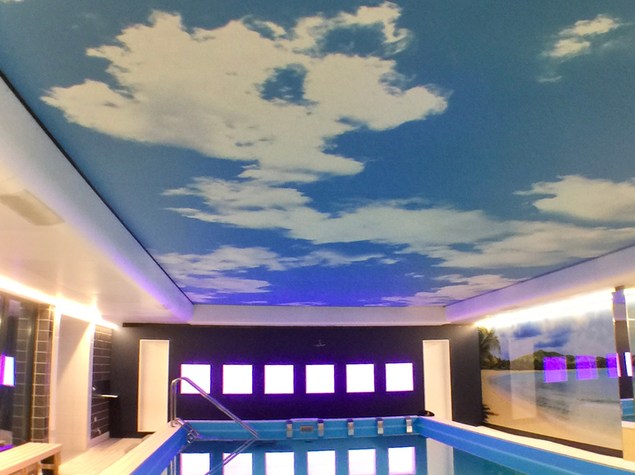
From the fruit bowl to the ceiling construction
The possible applications of a vacuum press
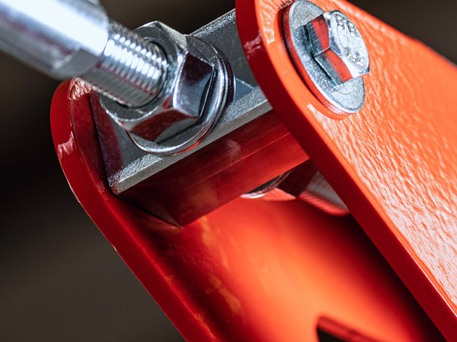
The Columbus Pressure Shifting Tool
So that natural rubber does not deform steel
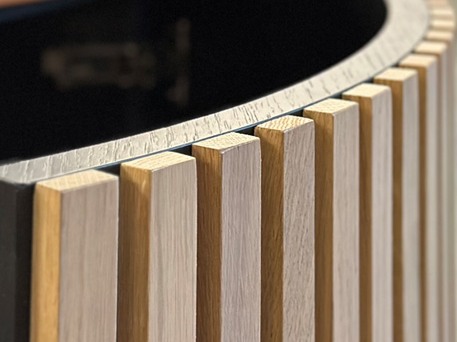
Kempa from Belgium invests in 2 vacuum presses
Round & curved shapes for modern interior design
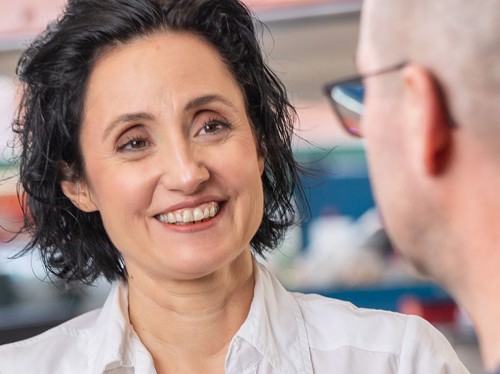
A patent for the modular system
Everyone said it doesn't work - I believed in it
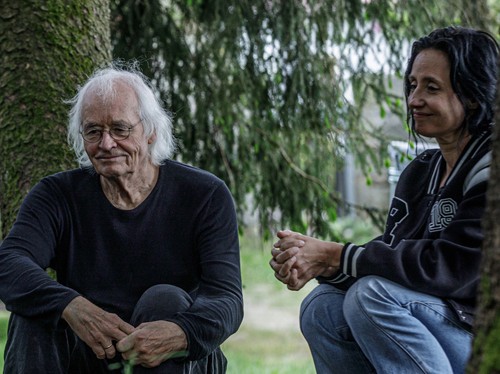
A look behind the scenes at Columbus
Thank you Dad, for a wonderful journey with you
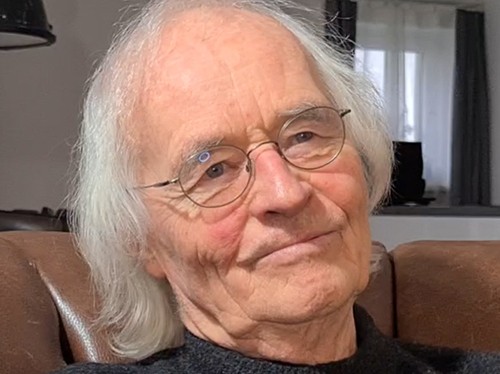
A look behind the scenes at Columbus
Günther Vetter - the invention of the vacuum bag
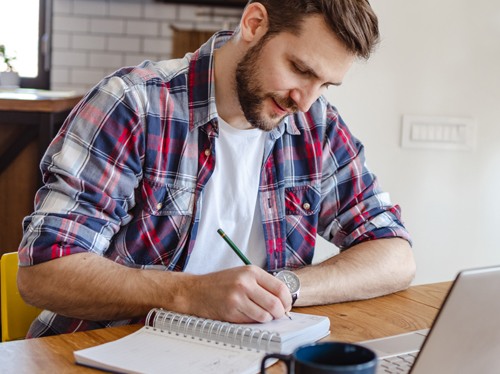
Protect your employees and your company
EU-mandated training for PUR hot melt adhesives
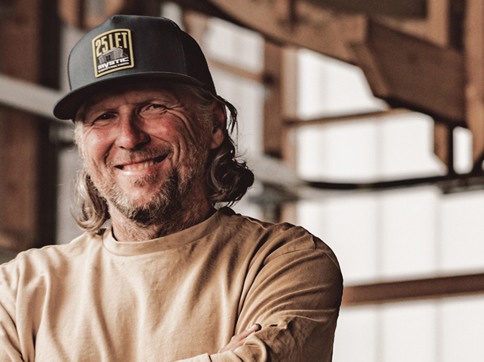
Skateboard ramps with the vacuum press Pioneer
Andreas Schützenberger does great things
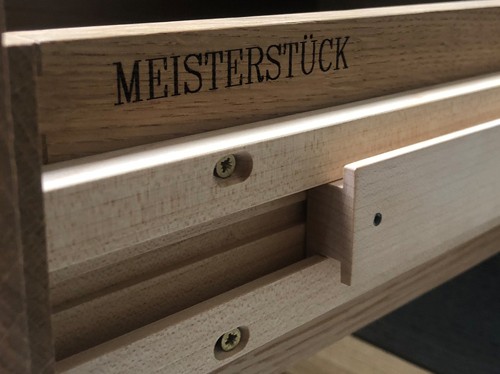
Vacuum bag: ZOSIA by Robert Nößler
His masterpiece with nostalgia and a secret
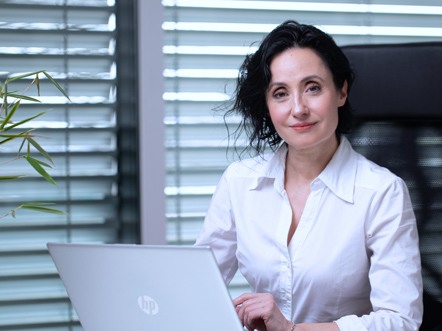
What are the benefits of a vacuum press?
Not only to cover curved workpieces and veneer

Report: International Fair in May 2023
Great success at the LIGNA in Hanover
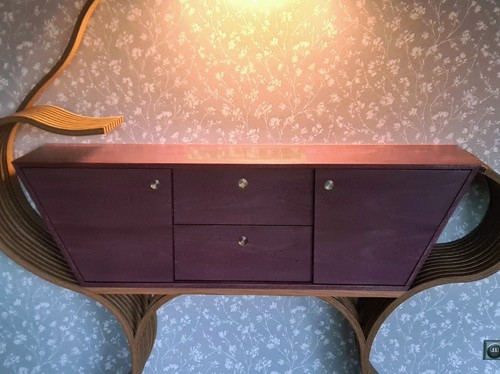
Vacuum bag: Modern Drop by Lars Hackl
Layer bonding for the next masterpiece
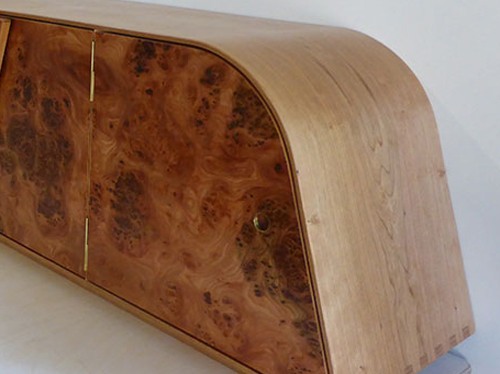
Vacuum bag: masterpiece by Tommy Kairat
First-class form veneering with Vacuflex
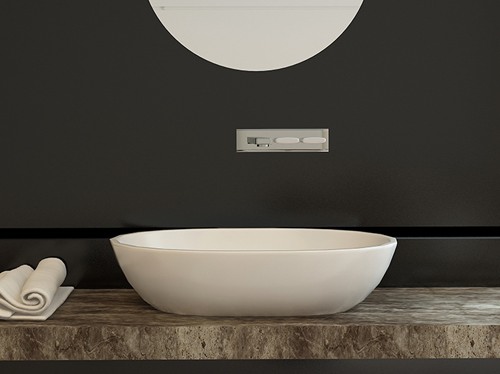
Forming of solid surface materials
Utilizing the great potential of a vacuum press
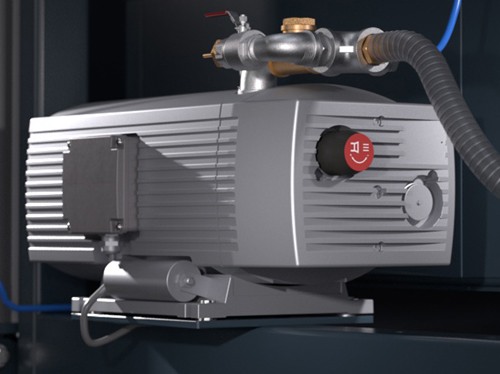
Vacuum pumps: an objective comparison
Columbus shows the advantages of dry runners
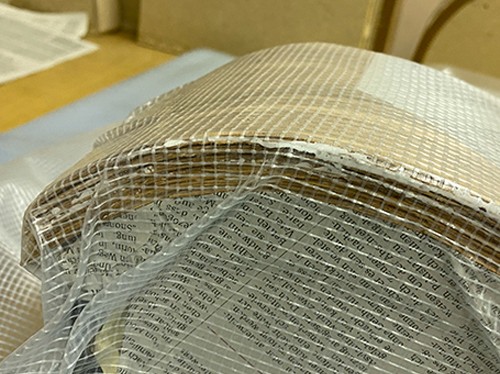
Free creativity in the creating process
Students from the Waldorfschule Mainz
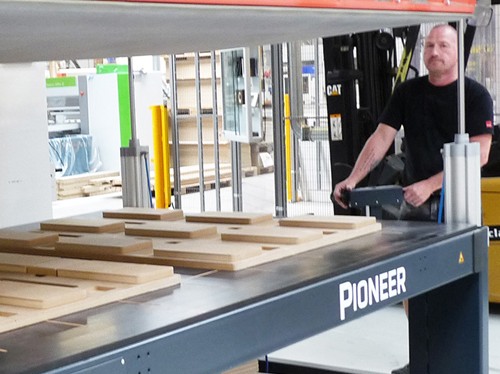
1.5 weeks instead of 6 weeks production time
Precisely curved fronts of the DALI speakers
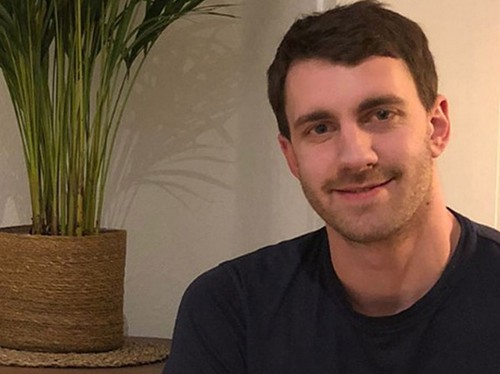
Vacuum bag: Markus Kramer's masterpiece
His vision brings the French past into the present
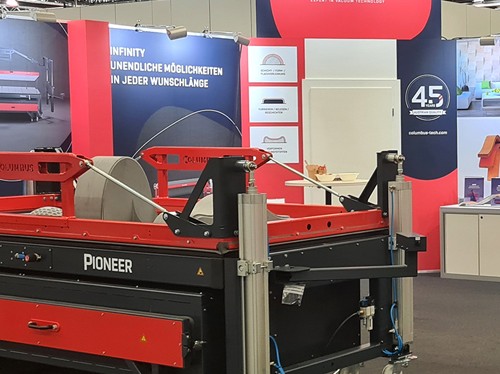
That was the Holz-Handwerk 2022
PIONEER and MOVE: Spectacular success at the fair
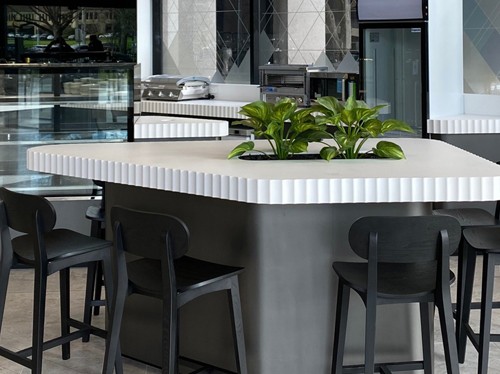
The magic lies in the perfect details
LL Installations creates high-quality accents
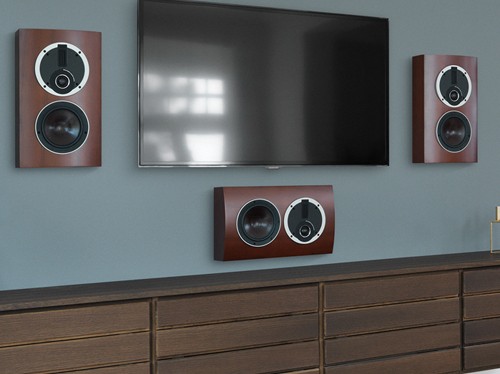
Handmade speakers from Denmark
One million satisfied DALI customers in over 70 countries
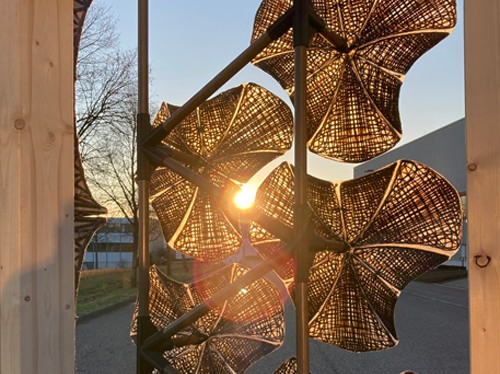
Columbus & University of Stuttgart
Artworks - Innovation meets Science
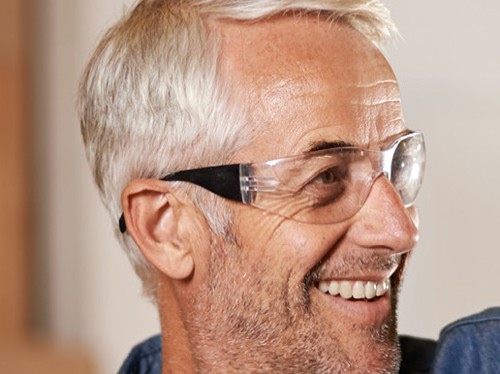
Independence from suppliers
6 Reasons to buy a Vacuum Press from Columbus
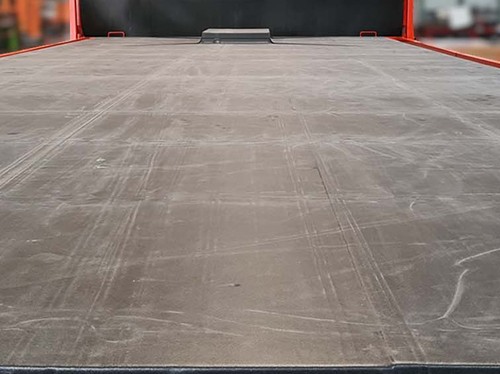
The Birth of Infinity Vacuum Press
Flexstone produces large parts for houseboats
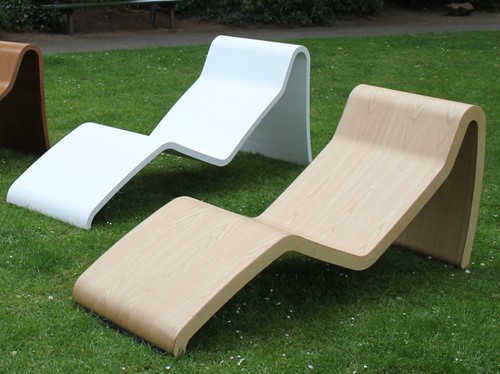
Sound loungers - feel the music
Magnus Hoffmann has developed something creative
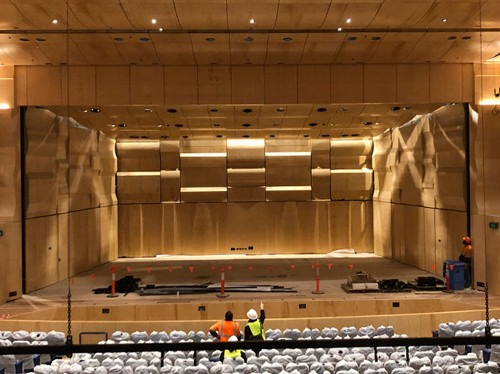
Excellence as far as the eye can see
Acoustic panels for the Leonardian Center in Australia
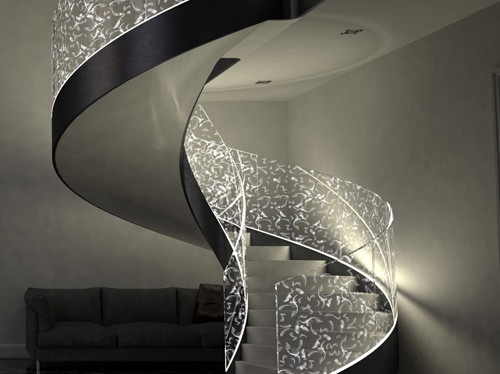
A dazzling cooperation between two pioneers
Vacuum - Acrylic glass - Unlimited possibilities
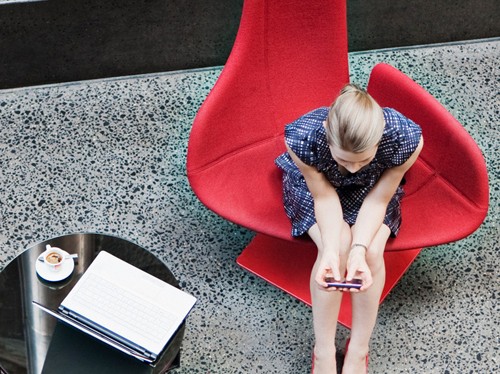
NOW: Individual. Exceptional. Unique.
Vacuum: Best performance from batch size 1
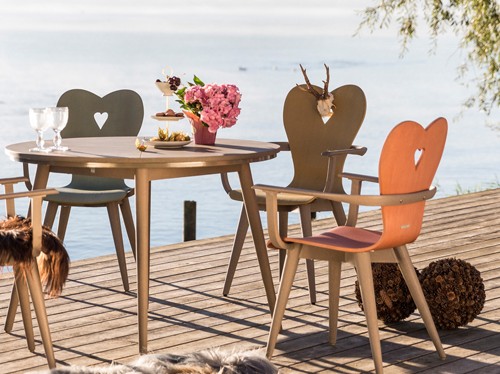
A compound better than wood
Resysta: Design meets sustainability
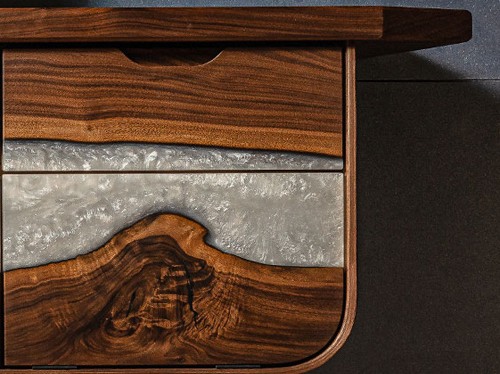
Vacuum bag: White River by Jannik Otte
Masterpiece as an eye-catcher for the entrance area
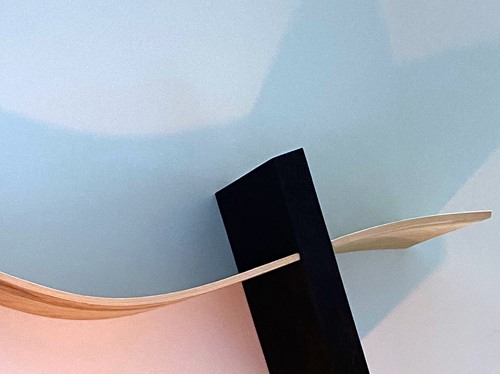
Young creativity conquers the world
Fascinating - these are students - not carpenters
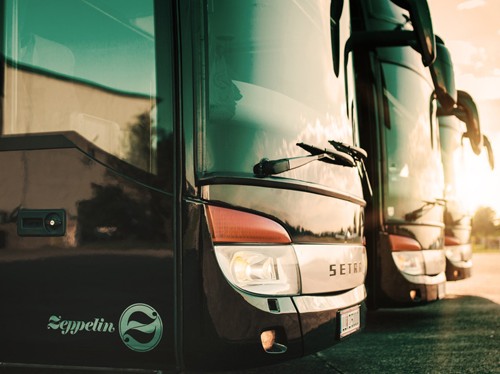
Full speed ahead with a vacuum press
Tour buses for the biggest stars in the world
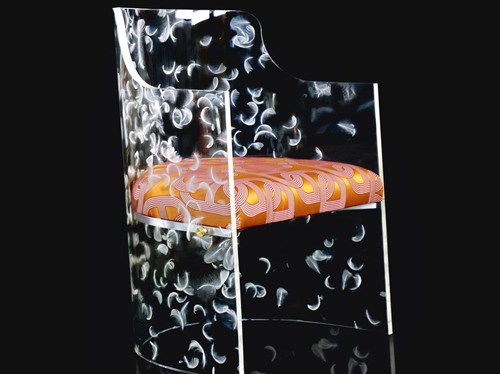
World premiere: acrylic glass chair
Customer Zöllner manufactures for Acrylic Couture
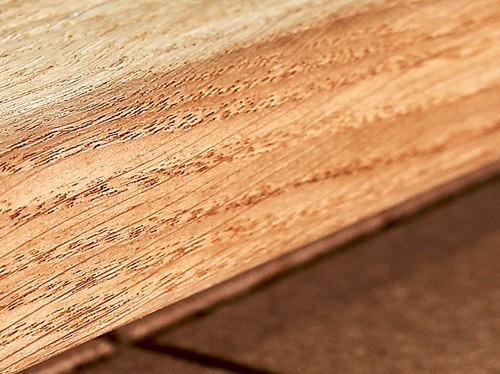
Columbus makes the impossible possible
VIDEO: Seamless veneering in just a few working steps
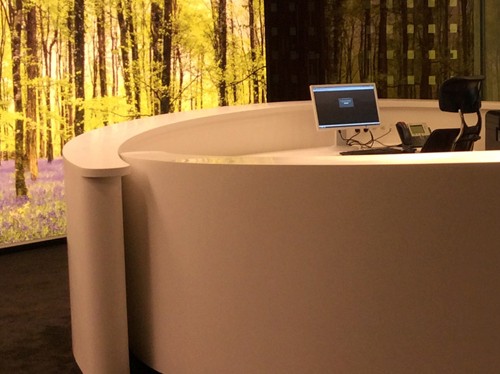
Columbus forms Kerrock in Belgium
An exceptional design future with vacuum presses
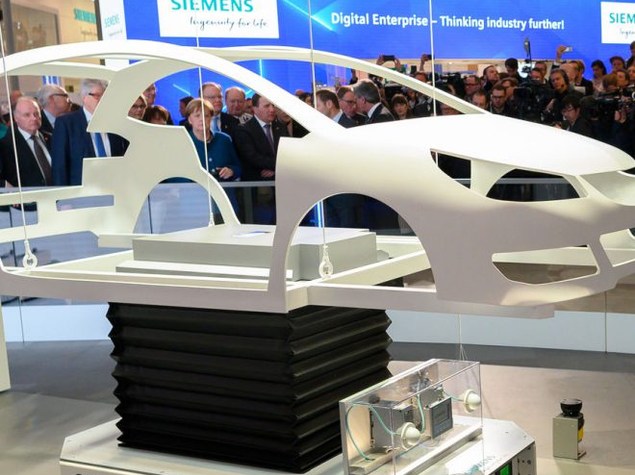
Exhibition builder Prager manufactures for Siemens
An innovative exhibition stand based on vacuum
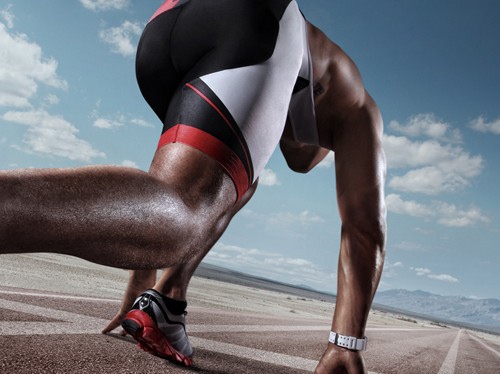
New times bring new opportunities
Conquering existing markets with new applications
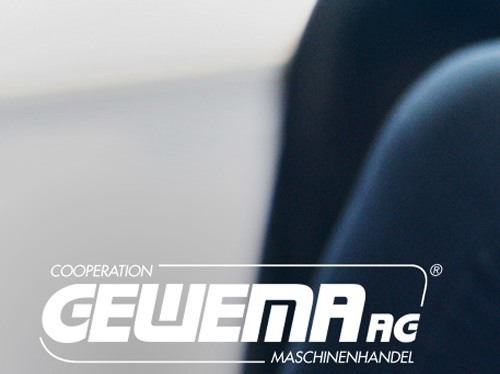
Columbus expands its global dealer network
GEWEMA membership for Columbus Vacuum Presses
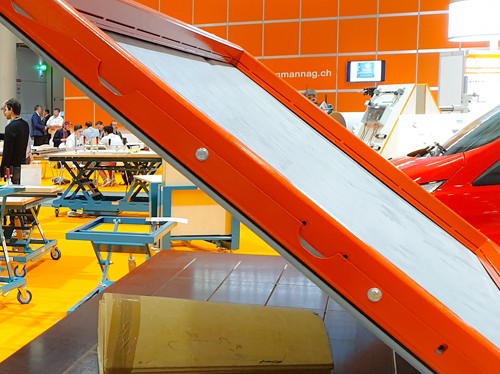
That was the Holz 2019 in Basel
Columbus and the great Swiss carpenters
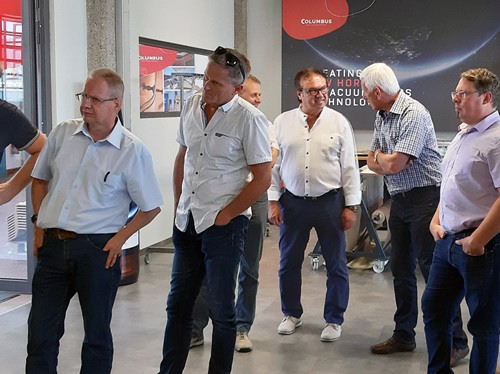
Cooperation with Schachermayer
Columbus receives another strong partner
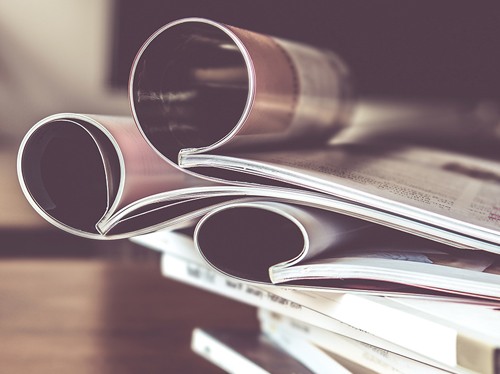
Press: People talk about Columbus
What is published in professional circles about us
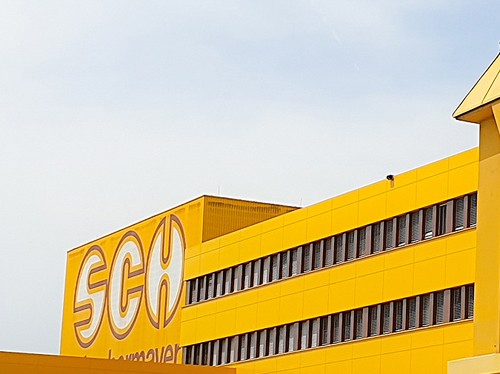
MEETING POINT NOBLE VENEER
Visiting the Schachermayer company
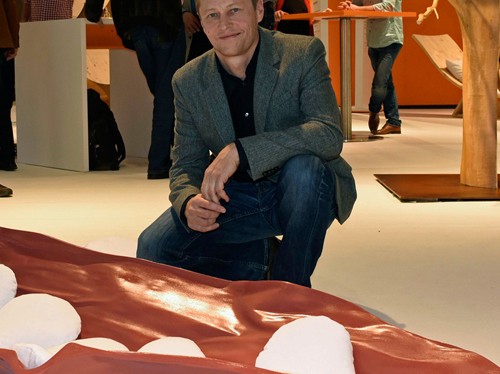
An Honor through Vacuum Technology
A chili as a creative lounge furniture is the winner
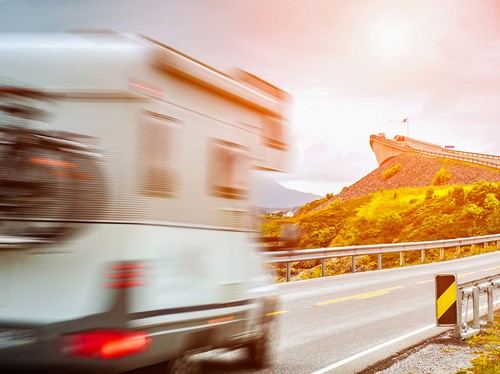
Hymer - a success story with vacuum
The well-known producer works with Columbus
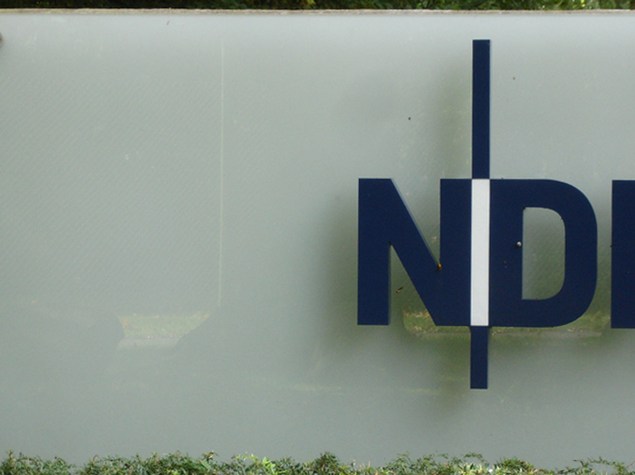
The NDR works with a vacuum press
The Tagesschau desk was produced with Columbus
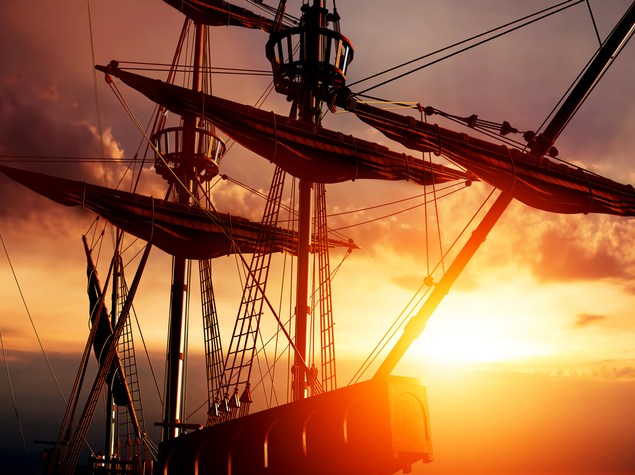
Why we are called what we are called
What Christopher Columbus has to do with Columbus