First-class form veneering with the
Vacuflex Vacuum Bag
The master carpenter and Columbus customer, Tommy Kairat, found his enthusiasm for the carpentry profession already during a school internship in a carpentry shop. Because of this, he did the apprenticeship and became a carpenter. Even after graduating, the craftsman continued to work in his training company for a long time and covered the areas of furniture and joinery. But over time, the future prospects were illuminated and so Tommy finally decided to give his creativity the necessary freedom and to pursue his work as a master carpenter completely independently.
He paved the way there with the production of his masterpiece and the use of the Vacuflex vacuum bag.
The theme of the masterpiece was freely selectable and so Tommy decided to fulfill a personal furniture wish. So he made a TV base cabinet, the shape of which is reminiscent of a sailing ship hull. Since sailing yachts are often equipped with fine veneers, Tommy took this into account when selecting the front veneer. The body, on the other hand, should be made of a lighter and simpler wood that blends in well with all environments.
Functionally, the cupboard should house the receiver for the TV sound system on the one hand, and offer two drawers for storing small items on the other.
The body was made from two curved layer-glued panels. These were glued crosswise from 21 layers of American cherry, giving the edge a multiplex look. The back panel, center panels and the base are also made of American cherry. The four doors are folded in a fold and provided with a burl elm veneer. The doors on the center panel have been mitered on both sides so that they can be opened 180 degrees and do not impede the user. They've also been given recessed brass handle shells that are over-veneered to blend in unobtrusively. The doors are held closed by a veneered magnet. The two drawers on the inside are guided through a solid wood pull-out. The rear wall has an opening for cable outlets and milled grooves for ventilation. The body was connected to each other with finger pins. The center panels were attached by a ridge joint and the bottoms by shaped springs.
Of course, the Vacuflex vacuum bag was used for all layer-gluing and veneering work. Perfect work relief for Tommy, because many of these work steps occurred in this project.
We would like to thank Tommy Kairat for sharing his story and wish the master carpenter all the best for the future.
He paved the way there with the production of his masterpiece and the use of the Vacuflex vacuum bag.
The idea - inspired by a ship's hull
The theme of the masterpiece was freely selectable and so Tommy decided to fulfill a personal furniture wish. So he made a TV base cabinet, the shape of which is reminiscent of a sailing ship hull. Since sailing yachts are often equipped with fine veneers, Tommy took this into account when selecting the front veneer. The body, on the other hand, should be made of a lighter and simpler wood that blends in well with all environments.
Functionally, the cupboard should house the receiver for the TV sound system on the one hand, and offer two drawers for storing small items on the other.
Material selection, structural design and manufacturing
The body was made from two curved layer-glued panels. These were glued crosswise from 21 layers of American cherry, giving the edge a multiplex look. The back panel, center panels and the base are also made of American cherry. The four doors are folded in a fold and provided with a burl elm veneer. The doors on the center panel have been mitered on both sides so that they can be opened 180 degrees and do not impede the user. They've also been given recessed brass handle shells that are over-veneered to blend in unobtrusively. The doors are held closed by a veneered magnet. The two drawers on the inside are guided through a solid wood pull-out. The rear wall has an opening for cable outlets and milled grooves for ventilation. The body was connected to each other with finger pins. The center panels were attached by a ridge joint and the bottoms by shaped springs.
Of course, the Vacuflex vacuum bag was used for all layer-gluing and veneering work. Perfect work relief for Tommy, because many of these work steps occurred in this project.
We would like to thank Tommy Kairat for sharing his story and wish the master carpenter all the best for the future.
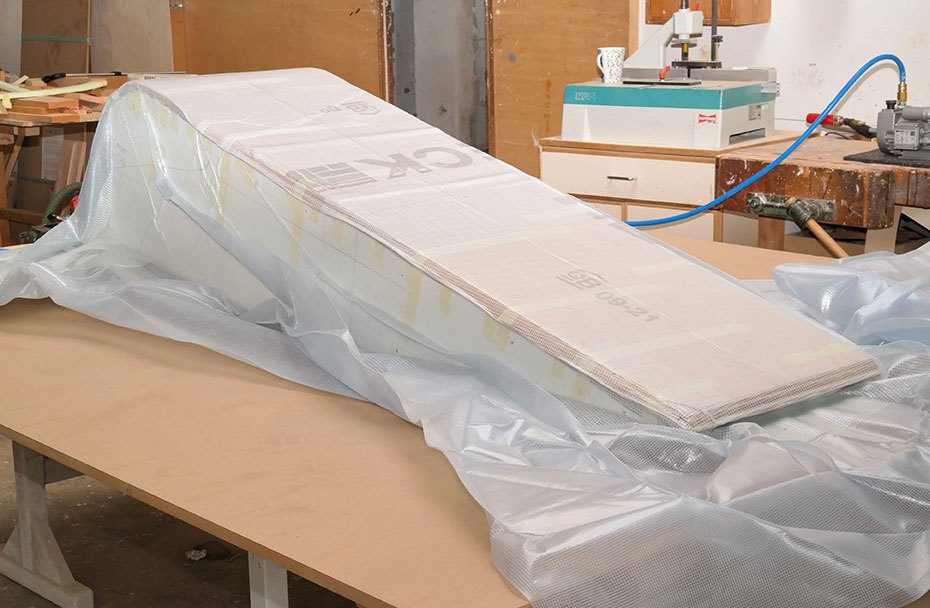
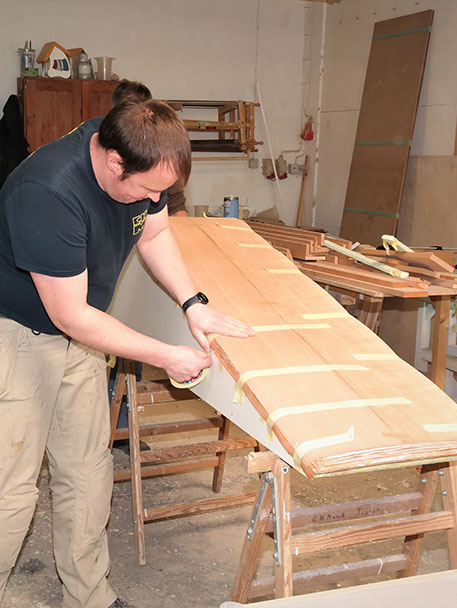
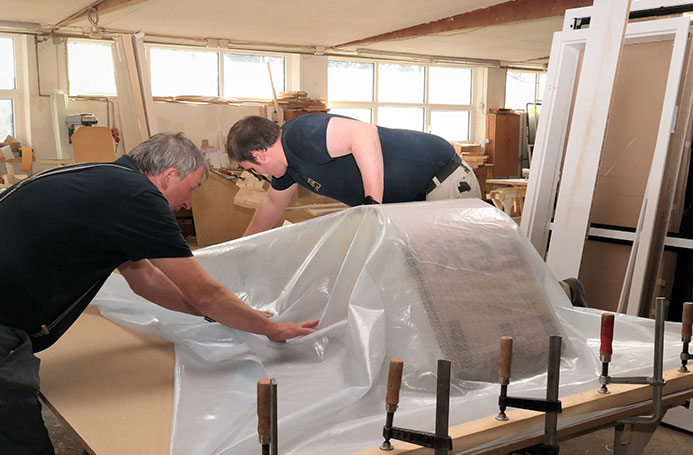
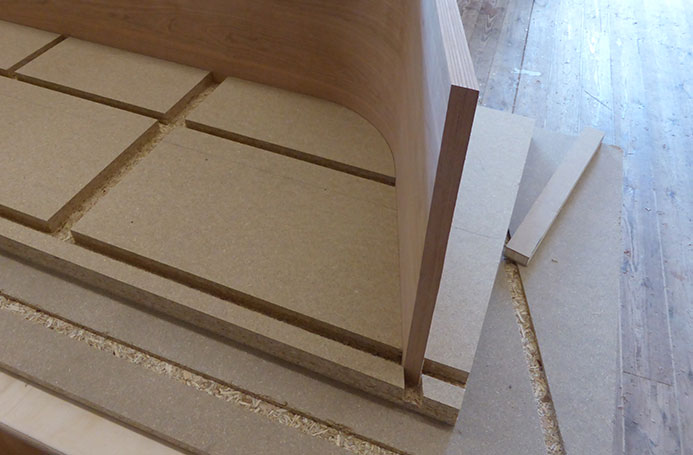
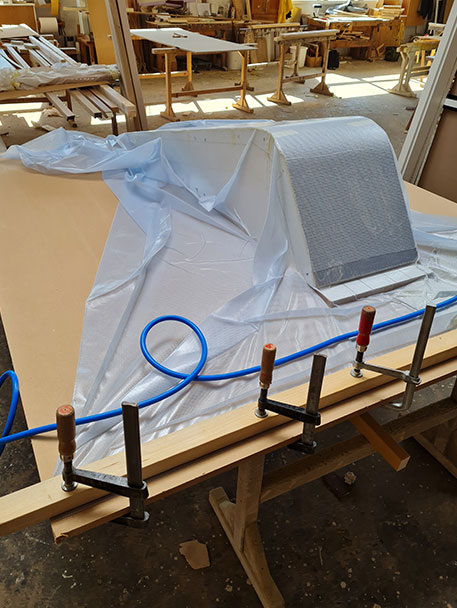
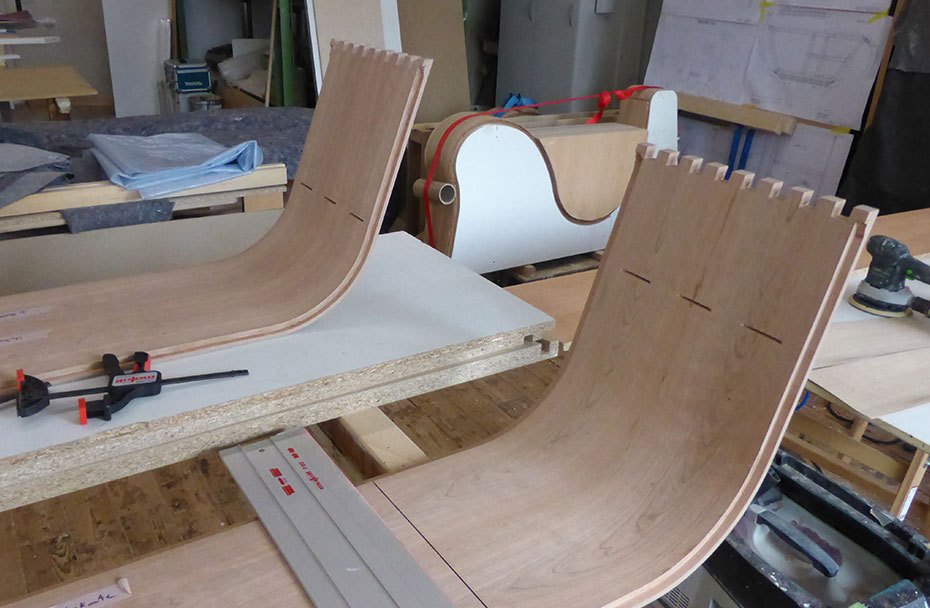
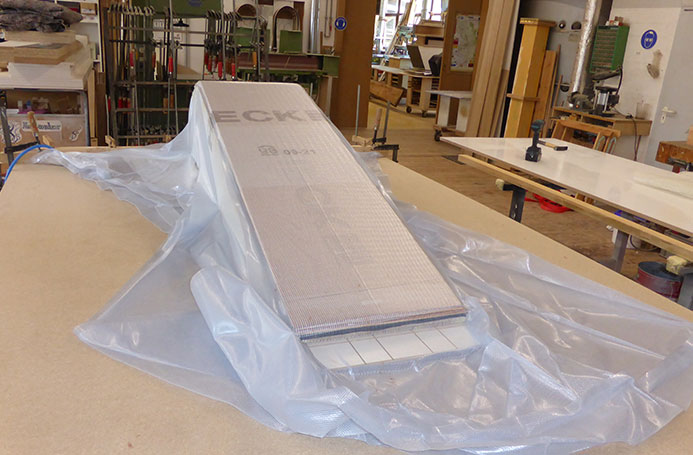
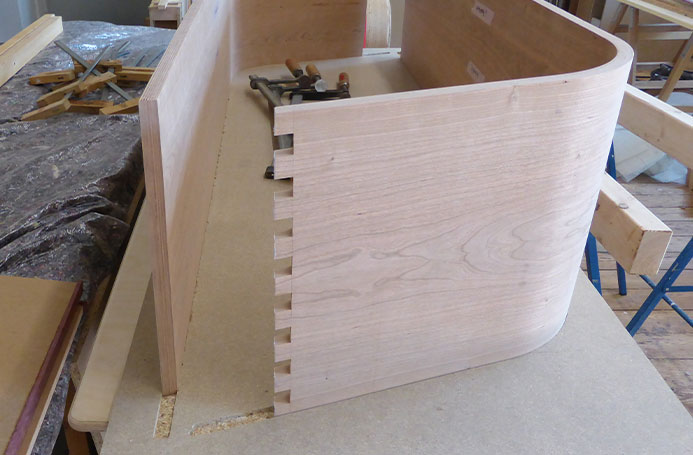
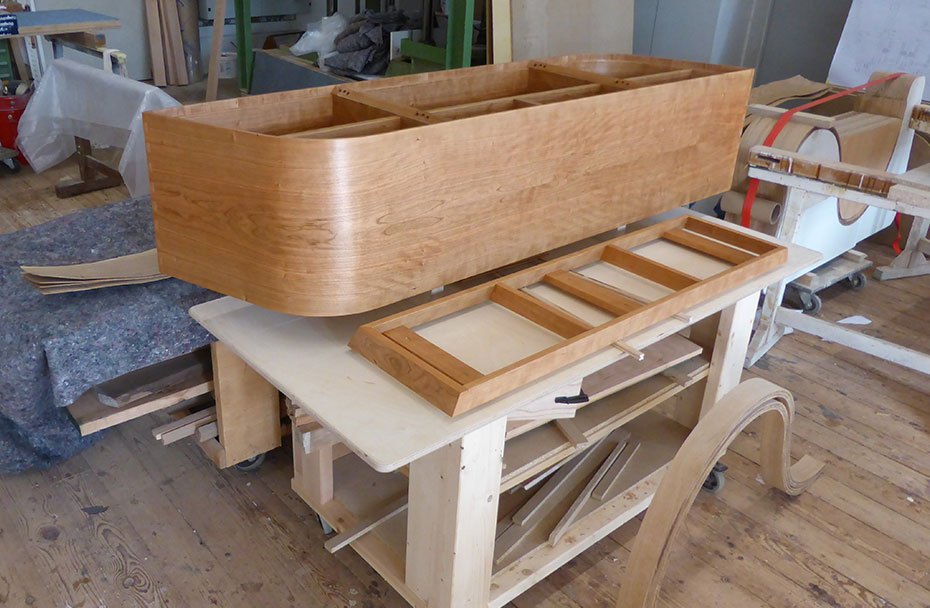
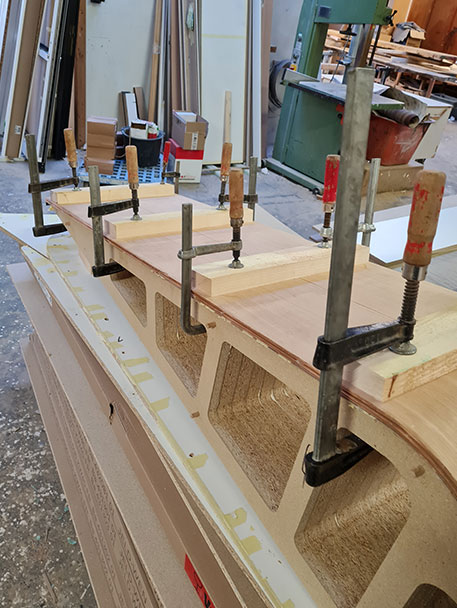
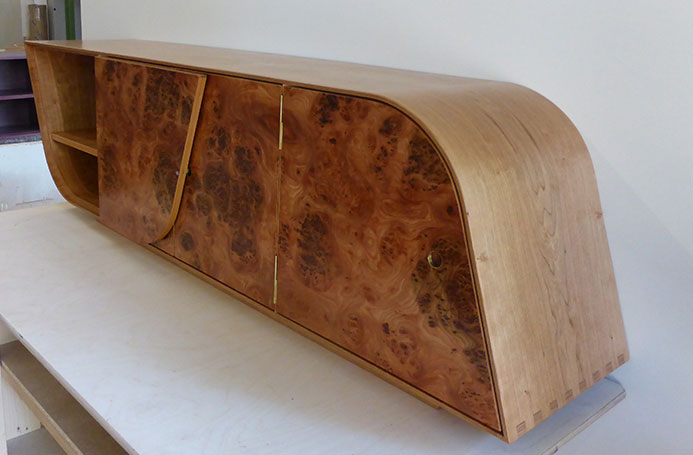
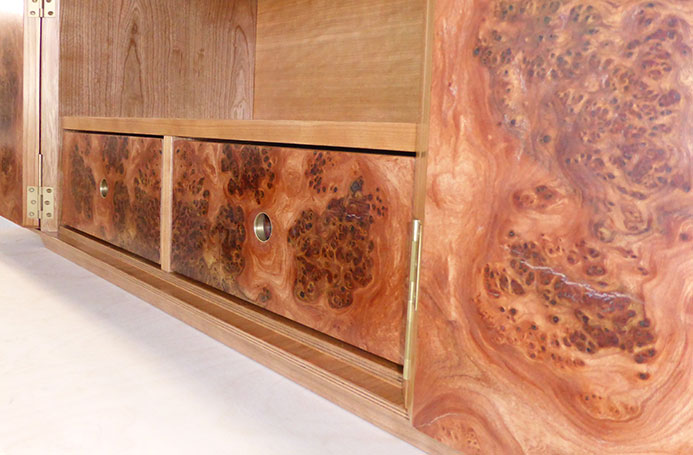
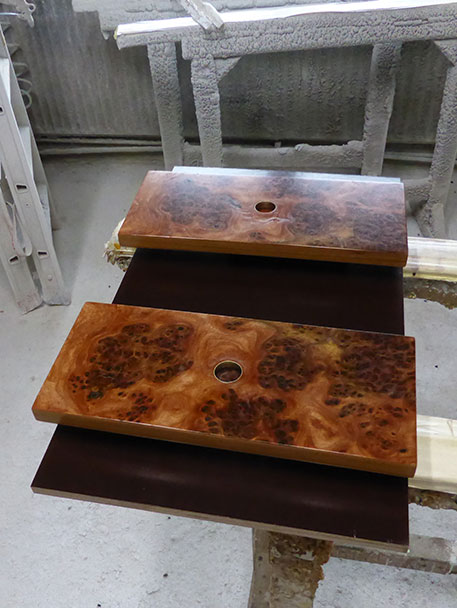
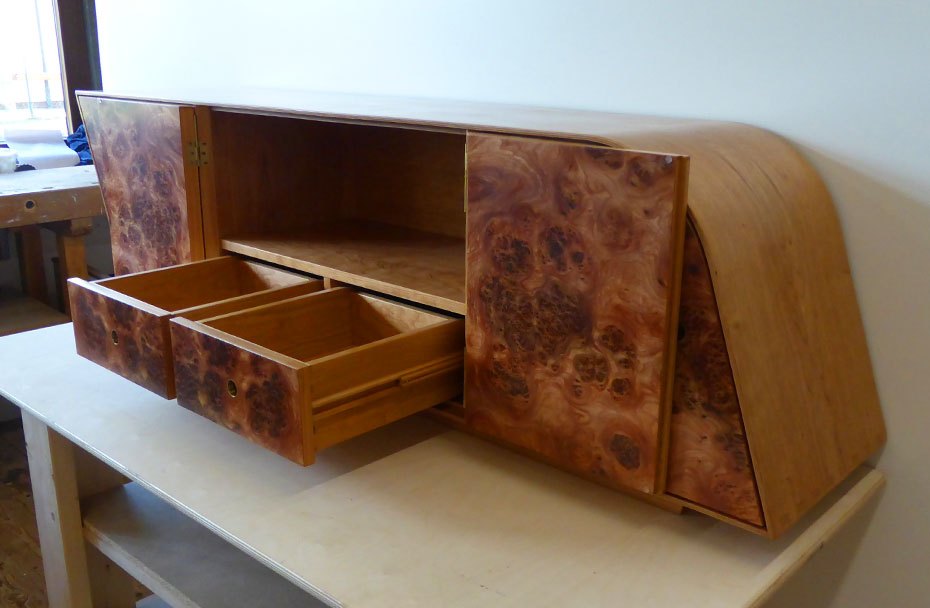
Interest?
We would be happy to inform you about the vacuum bag, your options, all versions, prices, etc.
Thank you very much for your inquiry!
We will get back in touch with you.
INTERESTING BLOG ARTICLE
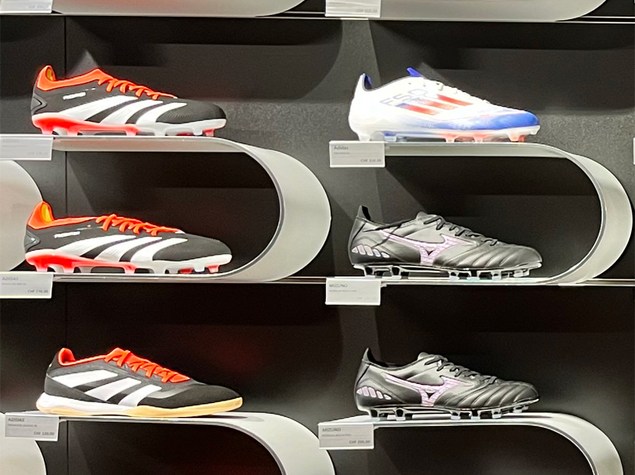
Realising Visions
Swiss Precision Meets Creative Design
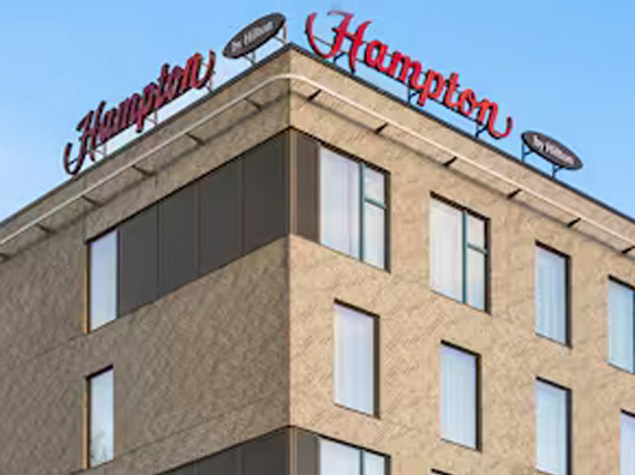
Tailor-made perfection in Estonia
Haapsalu Uksetehase AS Manufactures Doors for Hampton by Hilton
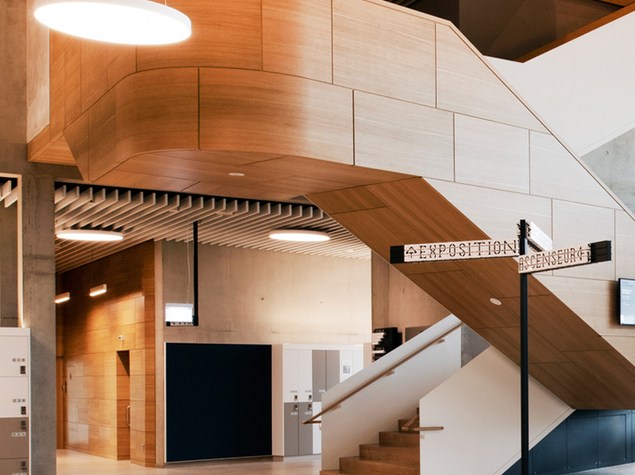
Premium Interior Fittings and Yacht Furnishings
A Vacuum Press has supported Der Ernzerhof for many years
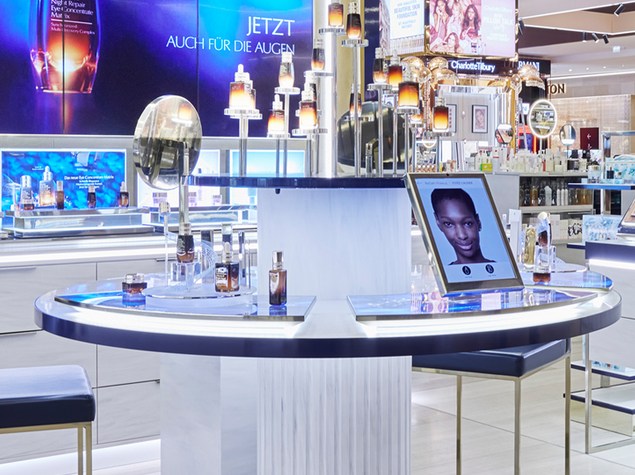
Outstanding Shopfitting with Vacuum
"außerdem" utilizes the advantages of a vacuum press by Columbus
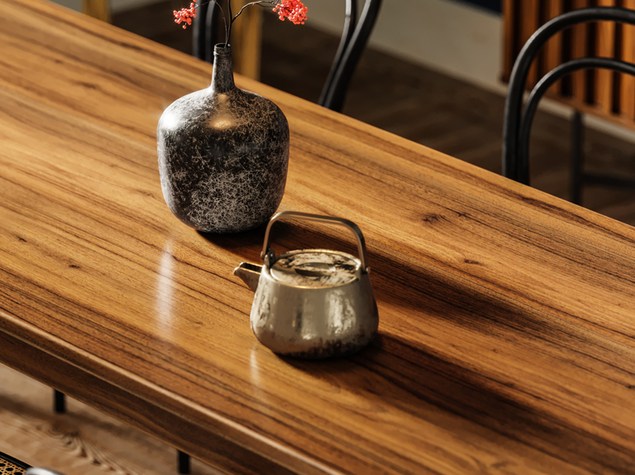
Flat veneering with vacuum
The use of a vacuum press as a veneer press
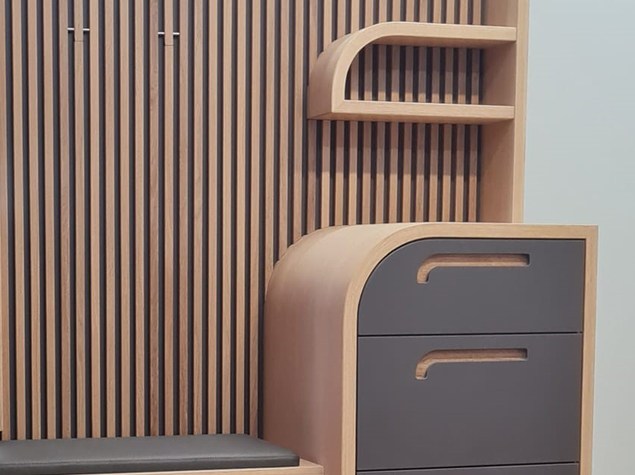
Masterful craftsmanship
The Wardrobe for the Master Carpenter Exam
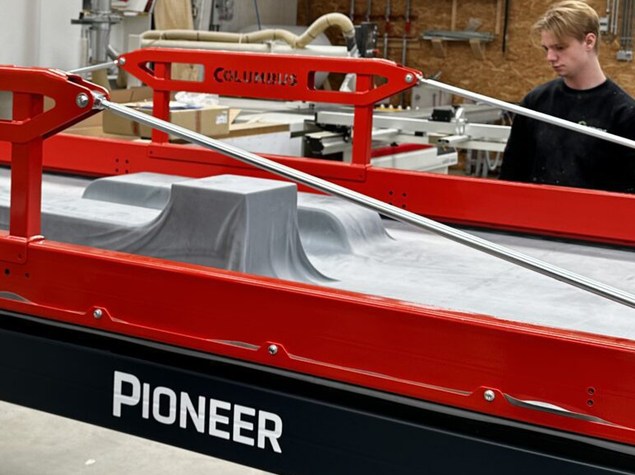
“It presses both flat and curved shapes”
Clairhout Interieur: A Revolution in Interior Design
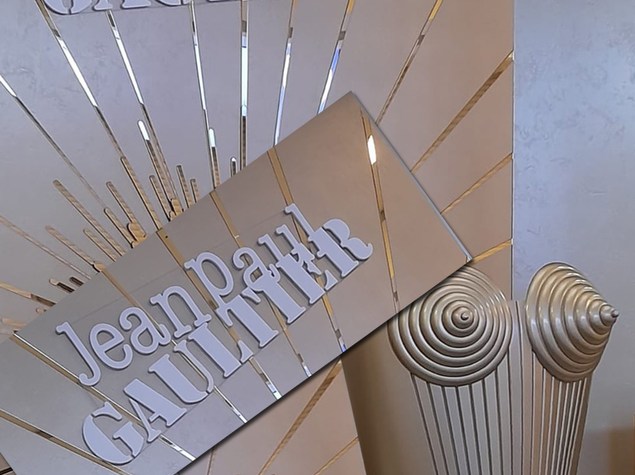
Columbus customer creates artistic masterpiece
Advertisement for Jean Paul Gaultier in Santiago de Chile

Beautiful Gift Idea
My Esel – exceptional bicycles & e-bikes
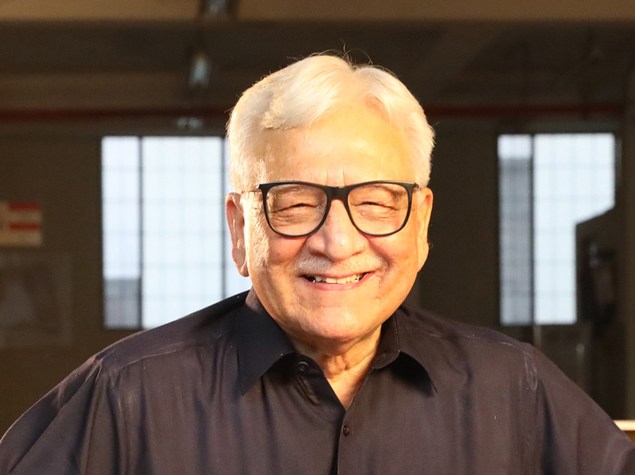
Curving the Impossible with Columbus
Interwood sets new standards with the press
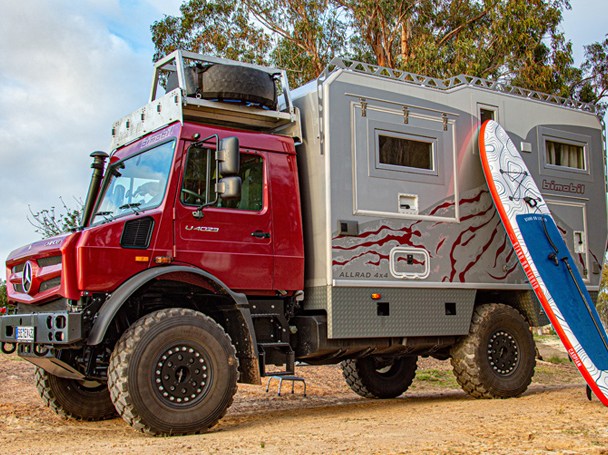
Infinity for bimobil motorhomes
Large-scale perfection for high-gloss paint
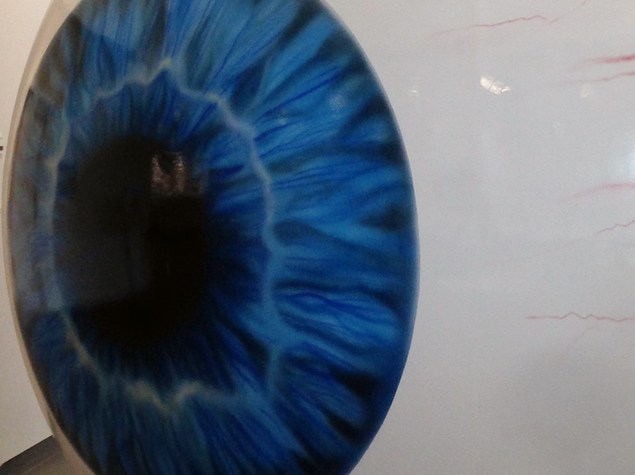
Precession and art from vacuum
Impressive eye model for the university clinic
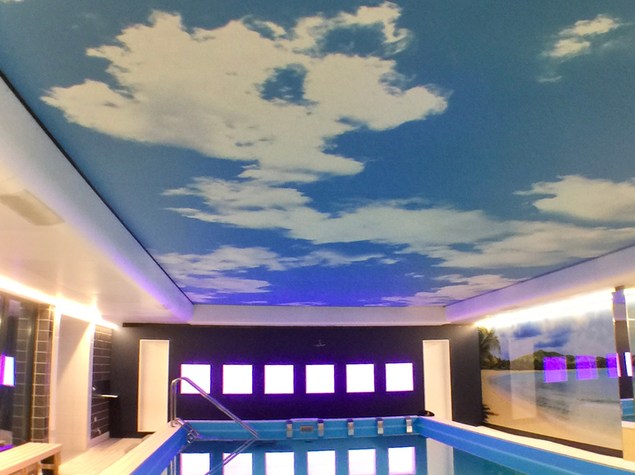
From the fruit bowl to the ceiling construction
The possible applications of a vacuum press
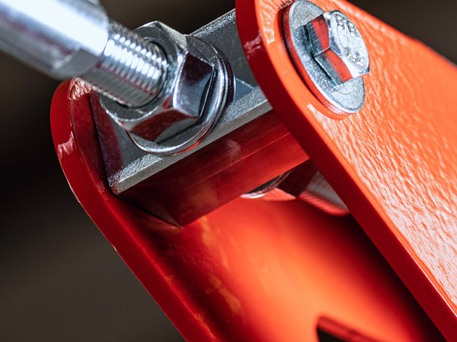
The Columbus Pressure Shifting Tool
So that natural rubber does not deform steel
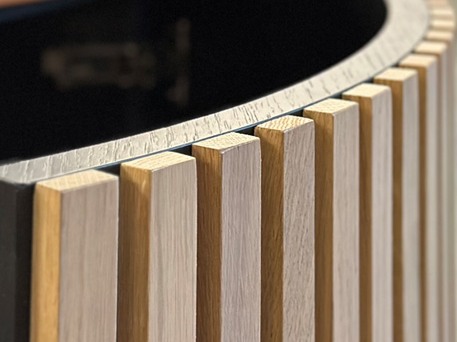
Kempa from Belgium invests in 2 vacuum presses
Round & curved shapes for modern interior design
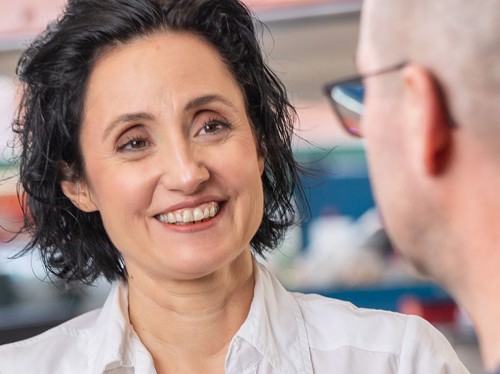
A patent for the modular system
Everyone said it doesn't work - I believed in it
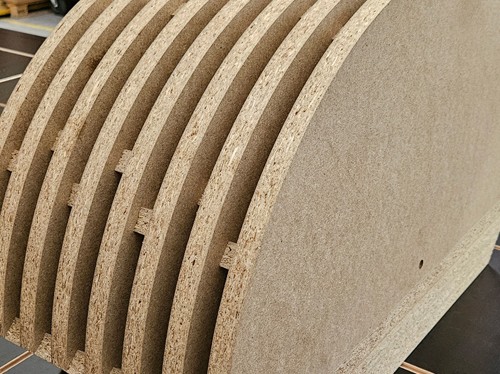
Columbus: Tips and Tricks from Practice
Mold making for mold bonding with vacuum
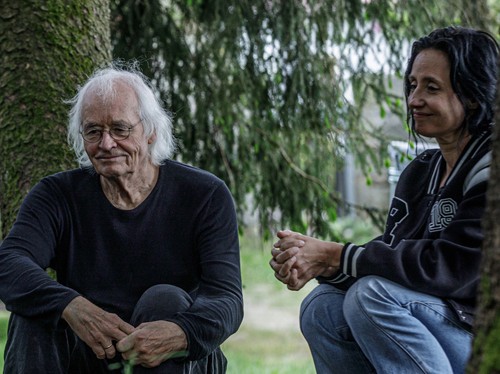
A look behind the scenes at Columbus
Thank you Dad, for a wonderful journey with you
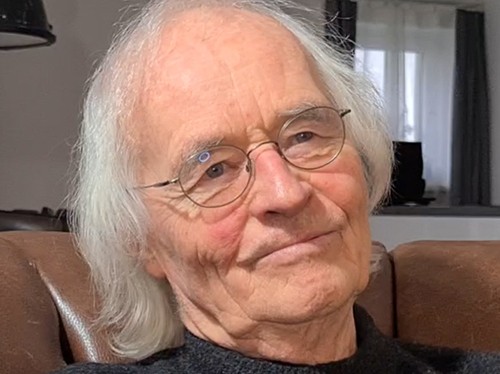
A look behind the scenes at Columbus
Günther Vetter - the invention of the vacuum bag
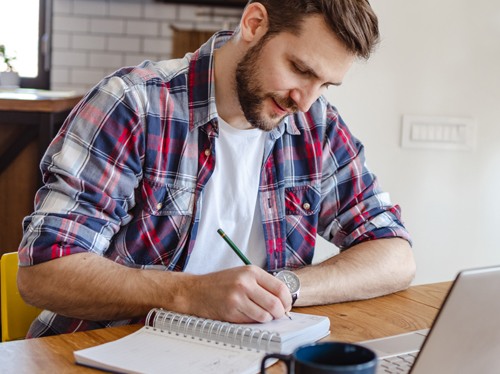
Protect your employees and your company
EU-mandated training for PUR hot melt adhesives
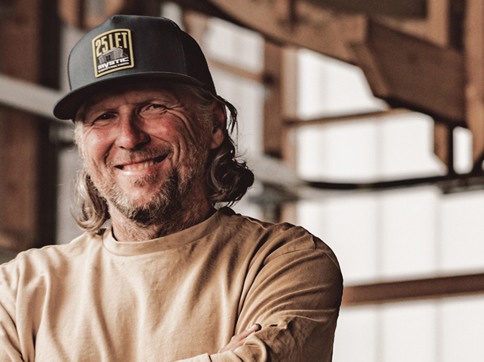
Skateboard ramps with the vacuum press Pioneer
Andreas Schützenberger does great things
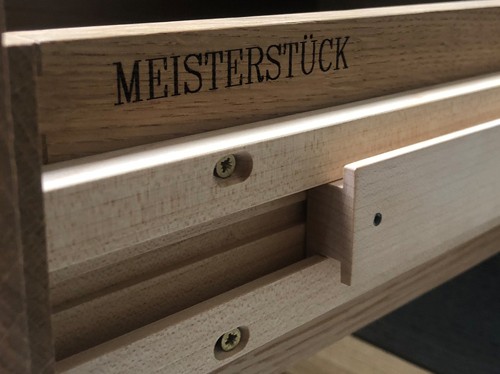
Vacuum bag: ZOSIA by Robert Nößler
His masterpiece with nostalgia and a secret
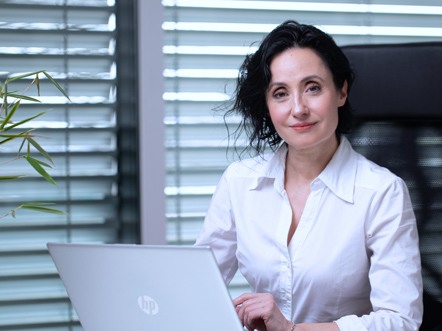
What are the benefits of a vacuum press?
Not only to cover curved workpieces and veneer

Report: International Fair in May 2023
Great success at the LIGNA in Hanover
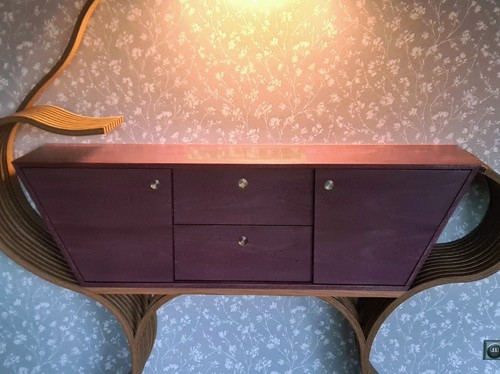
Vacuum bag: Modern Drop by Lars Hackl
Layer bonding for the next masterpiece
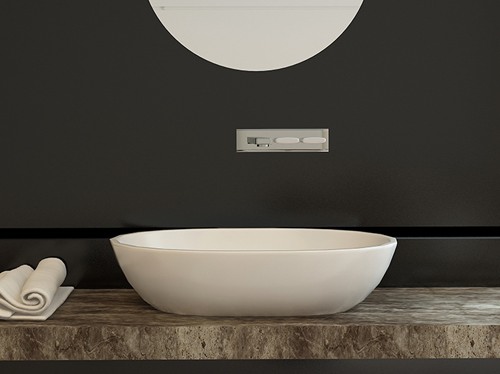
Forming of solid surface materials
Utilizing the great potential of a vacuum press
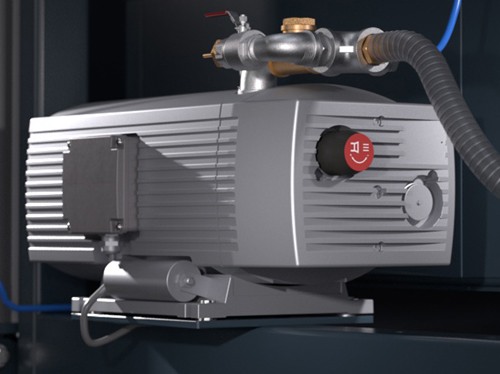
Vacuum pumps: an objective comparison
Columbus shows the advantages of dry runners
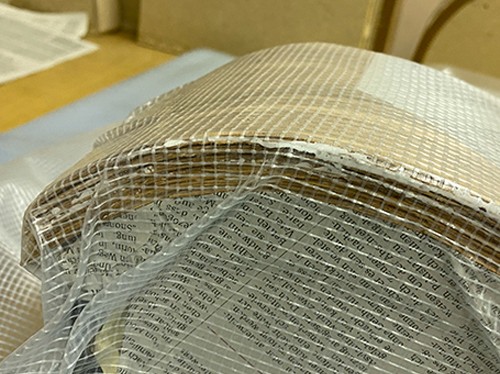
Free creativity in the creating process
Students from the Waldorfschule Mainz
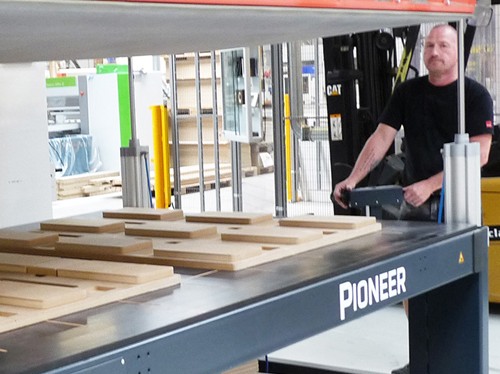
1.5 weeks instead of 6 weeks production time
Precisely curved fronts of the DALI speakers
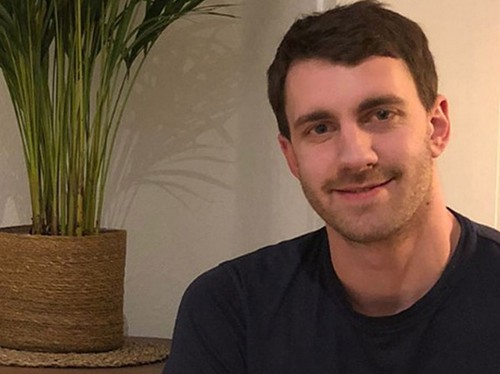
Vacuum bag: Markus Kramer's masterpiece
His vision brings the French past into the present
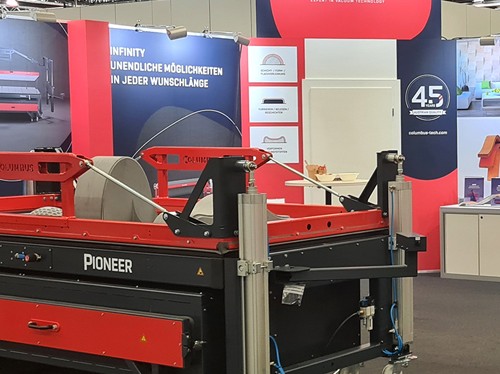
That was the Holz-Handwerk 2022
PIONEER and MOVE: Spectacular success at the fair
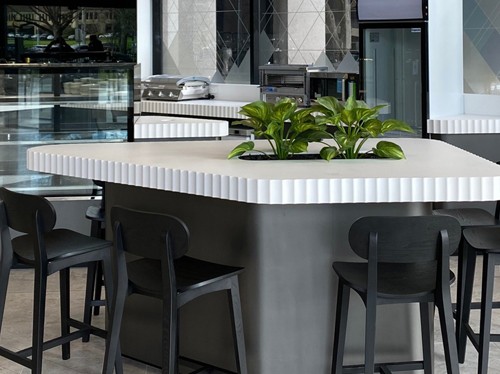
The magic lies in the perfect details
LL Installations creates high-quality accents
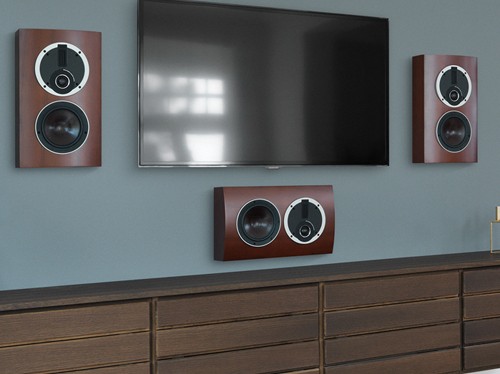
Handmade speakers from Denmark
One million satisfied DALI customers in over 70 countries
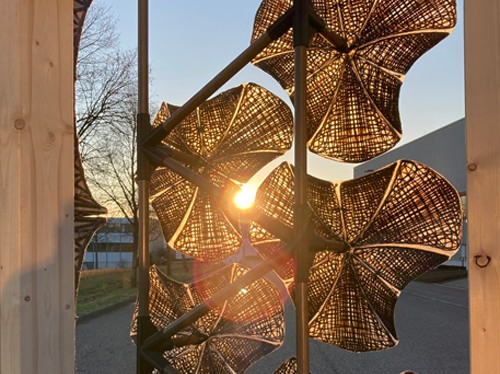
Columbus & University of Stuttgart
Artworks - Innovation meets Science
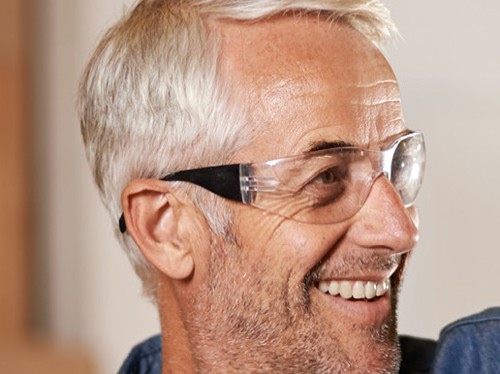
Independence from suppliers
6 Reasons to buy a Vacuum Press from Columbus
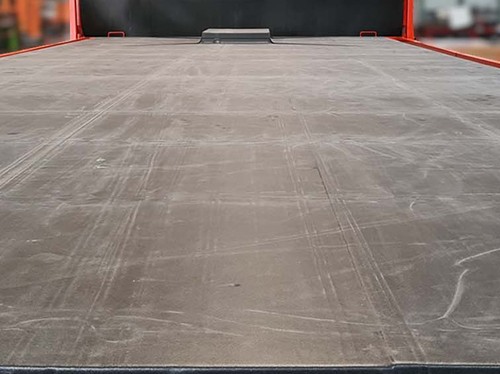
The Birth of Infinity Vacuum Press
Flexstone produces large parts for houseboats
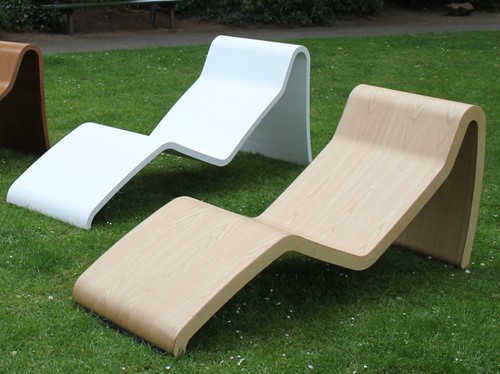
Sound loungers - feel the music
Magnus Hoffmann has developed something creative
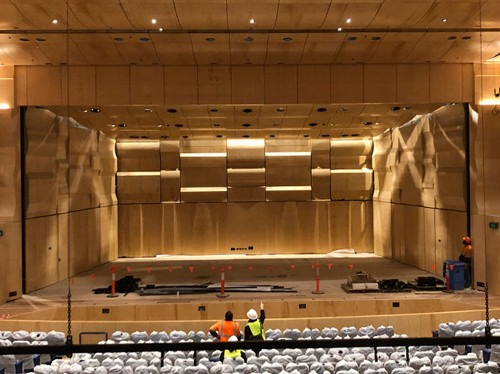
Excellence as far as the eye can see
Acoustic panels for the Leonardian Center in Australia
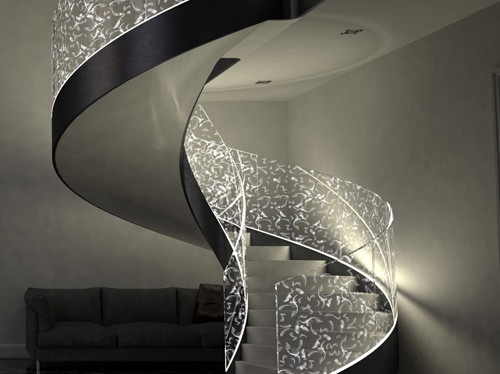
A dazzling cooperation between two pioneers
Vacuum - Acrylic glass - Unlimited possibilities
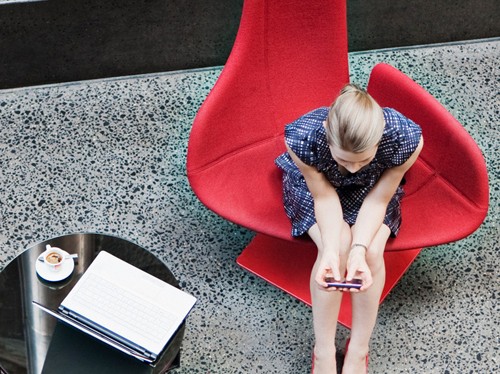
NOW: Individual. Exceptional. Unique.
Vacuum: Best performance from batch size 1
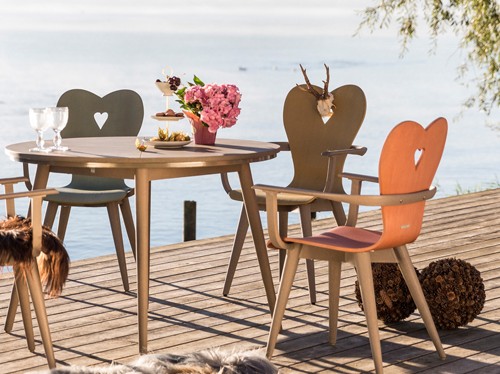
A compound better than wood
Resysta: Design meets sustainability
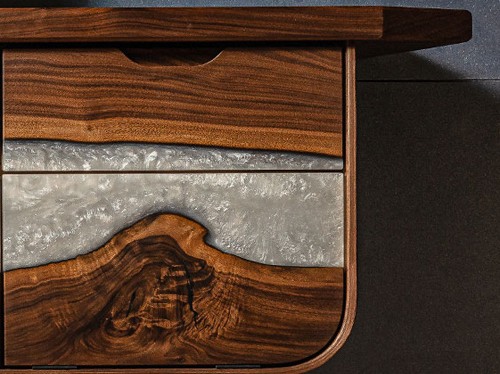
Vacuum bag: White River by Jannik Otte
Masterpiece as an eye-catcher for the entrance area
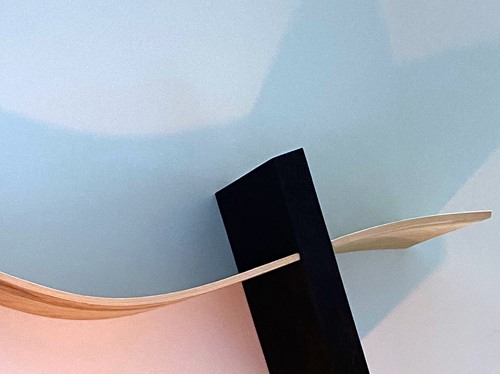
Young creativity conquers the world
Fascinating - these are students - not carpenters
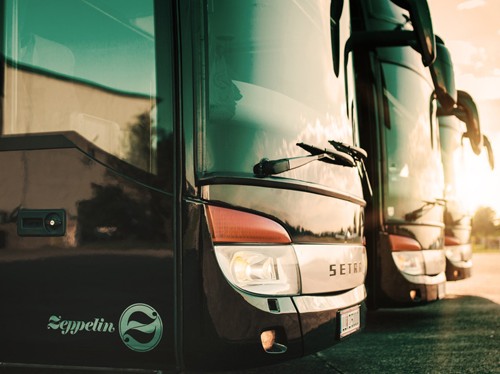
Full speed ahead with a vacuum press
Tour buses for the biggest stars in the world
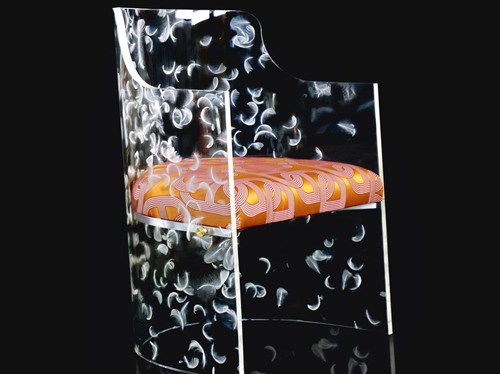
World premiere: acrylic glass chair
Customer Zöllner manufactures for Acrylic Couture
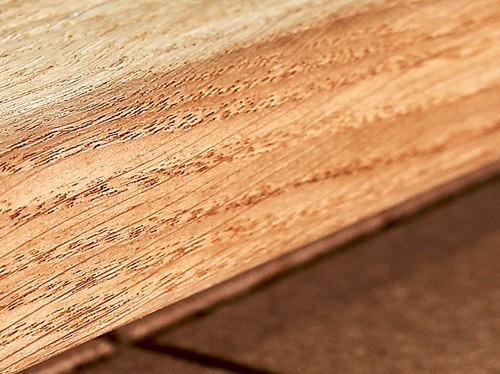
Columbus makes the impossible possible
VIDEO: Seamless veneering in just a few working steps
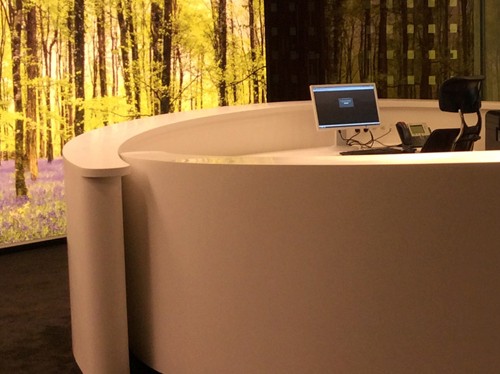
Columbus forms Kerrock in Belgium
An exceptional design future with vacuum presses
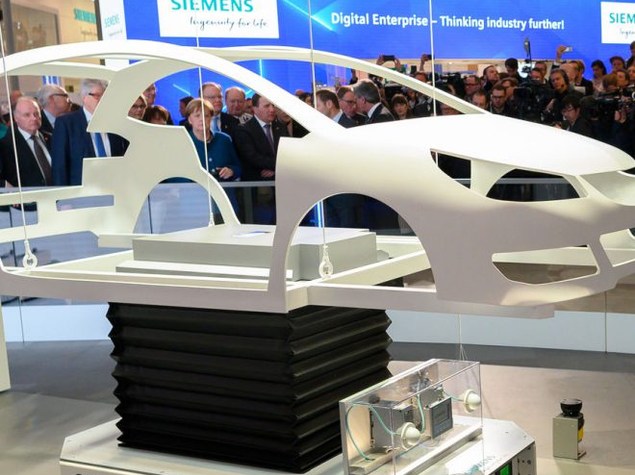
Exhibition builder Prager manufactures for Siemens
An innovative exhibition stand based on vacuum
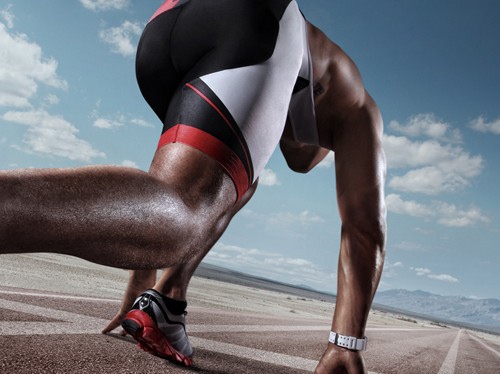
New times bring new opportunities
Conquering existing markets with new applications
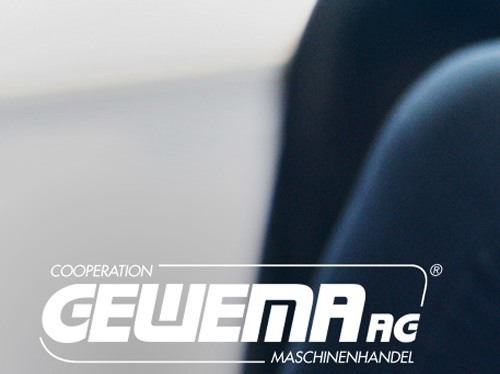
Columbus expands its global dealer network
GEWEMA membership for Columbus Vacuum Presses
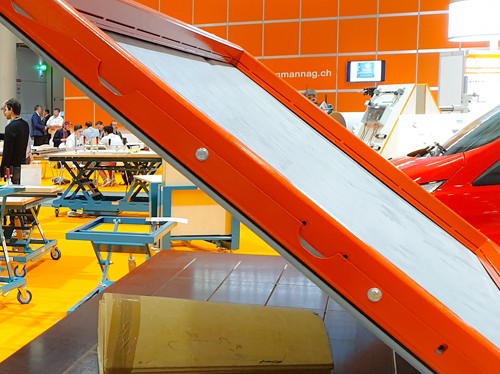
That was the Holz 2019 in Basel
Columbus and the great Swiss carpenters
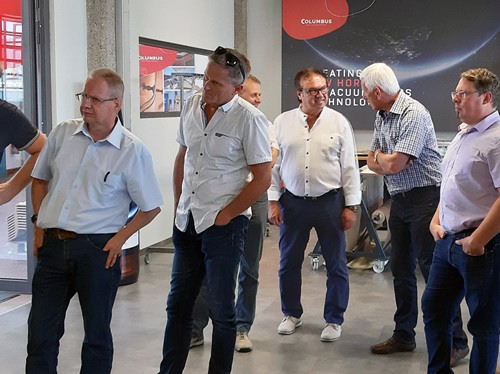
Cooperation with Schachermayer
Columbus receives another strong partner
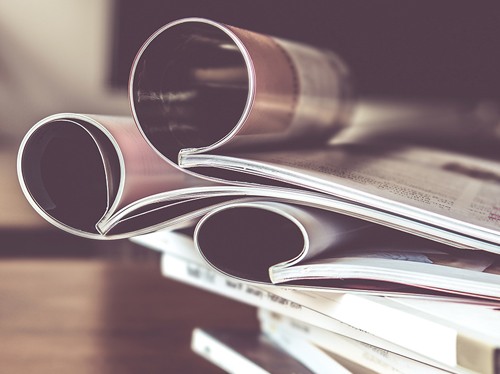
Press: People talk about Columbus
What is published in professional circles about us
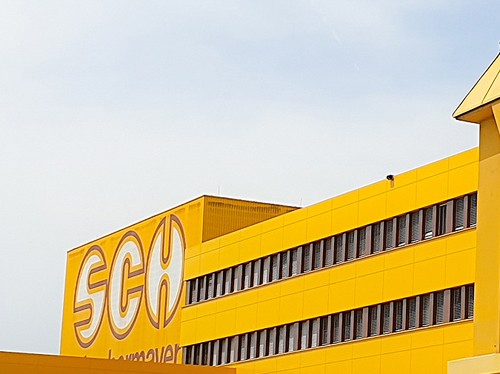
MEETING POINT NOBLE VENEER
Visiting the Schachermayer company
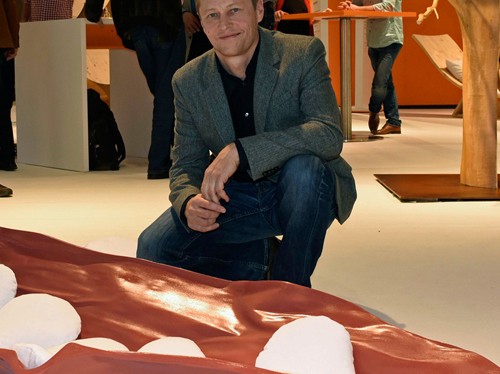
An Honor through Vacuum Technology
A chili as a creative lounge furniture is the winner
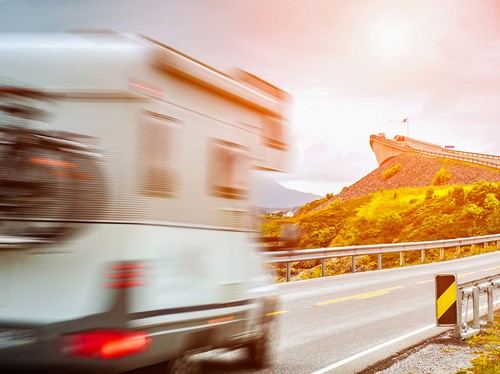
Hymer - a success story with vacuum
The well-known producer works with Columbus
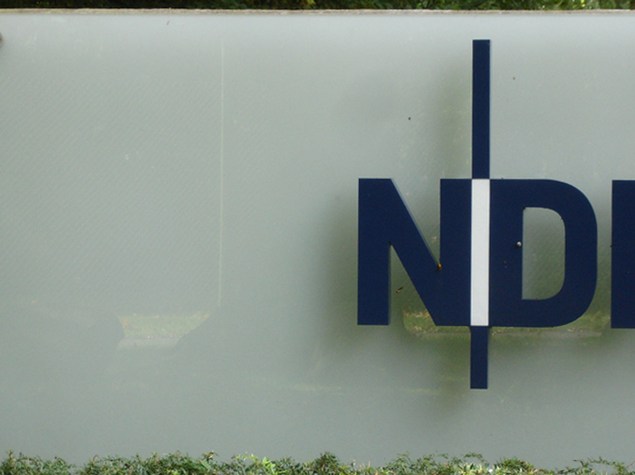
The NDR works with a vacuum press
The Tagesschau desk was produced with Columbus
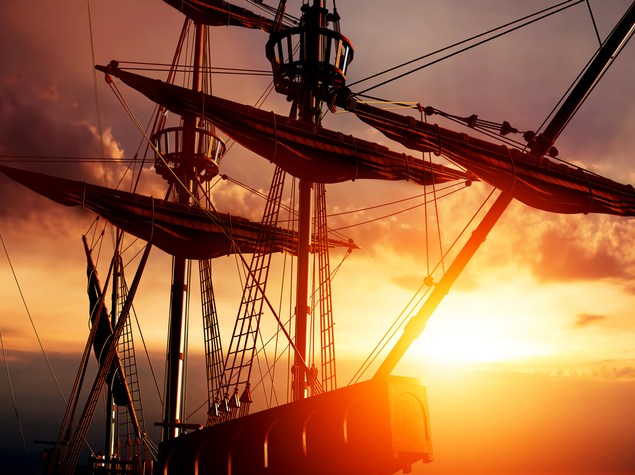
Why we are called what we are called
What Christopher Columbus has to do with Columbus