Curved fronts on DALI speakers made in a vacuum press
DALI speakers are known throughout the world for their sound and high quality. The company has gained global recognition for their high-end speakers and is today sold in more than 70 countries. A strategic decision that DALI will to a greater extent be "MADE IN DENMARK", has led the company to strengthen its home production at its headquarters in Nørager. This has, among other things, led to the purchase of a large vacuum press.
The diaphragm press is of the Columbus Pioneer type and is one of the largest vacuum presses on the market. The diaphragm press is recognized for its simple and functional design with vertical opening and closing function that makes the machine easy to use. At DALI, the curved speaker fronts are placed in the press. The items are covered with glue and 4 mm thick veneer sheets. When the press is full, the operator closes the press mechanically. The strong silicone membrane of natural rubber closes tightly around the workpieces and through vacuum suction the veneer is pressed onto the workpieces. The press presses up to 900 mbar and after an hour in the press, the items are finished.
Thomas Martin Holm, COO at DALI states that surface finish and design are crucial for these high-end speakers. In the choice of machine, he emphasized that the membrane press avoids joints and point pressures. The veneer is delivered primed and with a saturated surface. After the speaker cabinets have been assembled, meticulously inspected, and refined by hand, they can therefore be sent directly for painting. One round in the painting plant, and the cabinets are ready to be shipped on for assembly. Fast and efficient.
The large vacuum press is part of a major production reorganization and in collaboration with the company's new, large UV painting plant, a noticeable change has been undergone. The drying time is completely avoided due to the UV system, and it only takes 1-2 hours depending on the size of the cabinet, from the time it is put on the conveyor until it comes out again freshly painted and dry. Through these changes, the production time for speakers with a curved edge has been reduced from 6 weeks to 1½ to 2 weeks. A reduction which means that you are fully competitive with foreign producers and can advantageously bring production home to the country. Production optimization is one of the cornerstones of DALI´'s strategy for "MADE IN DENMARK".
The diaphragm press is of the Columbus Pioneer type and is one of the largest vacuum presses on the market. The diaphragm press is recognized for its simple and functional design with vertical opening and closing function that makes the machine easy to use. At DALI, the curved speaker fronts are placed in the press. The items are covered with glue and 4 mm thick veneer sheets. When the press is full, the operator closes the press mechanically. The strong silicone membrane of natural rubber closes tightly around the workpieces and through vacuum suction the veneer is pressed onto the workpieces. The press presses up to 900 mbar and after an hour in the press, the items are finished.
An impressive surface finish
Thomas Martin Holm, COO at DALI states that surface finish and design are crucial for these high-end speakers. In the choice of machine, he emphasized that the membrane press avoids joints and point pressures. The veneer is delivered primed and with a saturated surface. After the speaker cabinets have been assembled, meticulously inspected, and refined by hand, they can therefore be sent directly for painting. One round in the painting plant, and the cabinets are ready to be shipped on for assembly. Fast and efficient.
Production time significantly reduced
The large vacuum press is part of a major production reorganization and in collaboration with the company's new, large UV painting plant, a noticeable change has been undergone. The drying time is completely avoided due to the UV system, and it only takes 1-2 hours depending on the size of the cabinet, from the time it is put on the conveyor until it comes out again freshly painted and dry. Through these changes, the production time for speakers with a curved edge has been reduced from 6 weeks to 1½ to 2 weeks. A reduction which means that you are fully competitive with foreign producers and can advantageously bring production home to the country. Production optimization is one of the cornerstones of DALI´'s strategy for "MADE IN DENMARK".
The vacuum press was purchased from Junget A/S (www.junget.com), who sells the Columbus brand in Denmark. Ulrik Søe Simonsen, KAM from Junget is seen here to the left in the picture together with Thomas Martin Holm, COO at DALI.
More information about DALI: www.dali-speakers.com
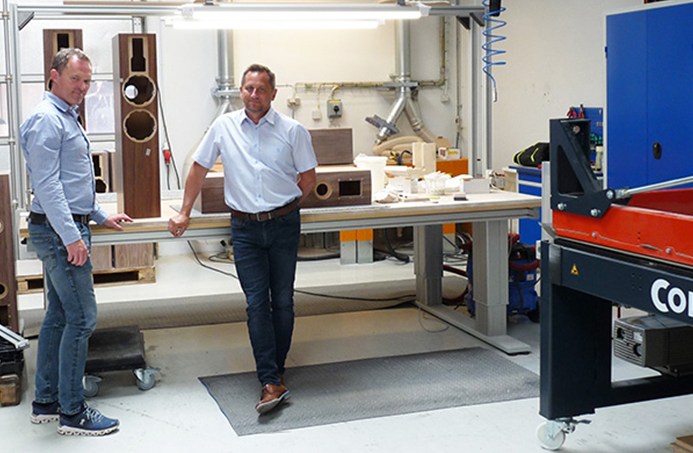
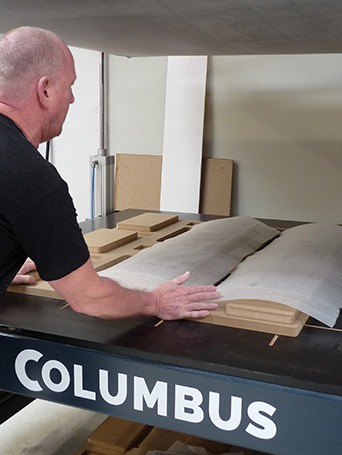
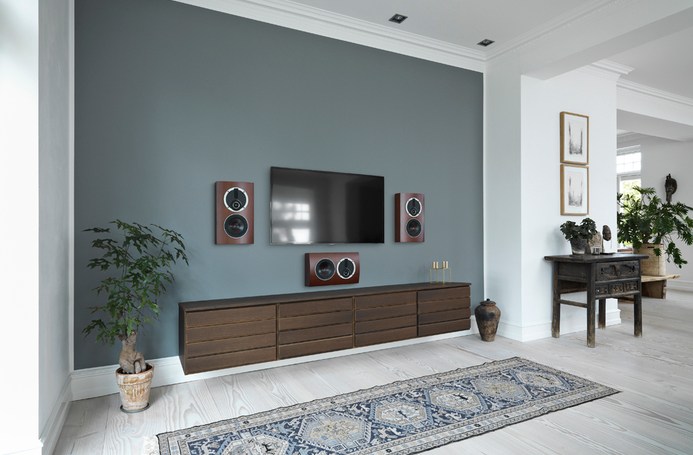
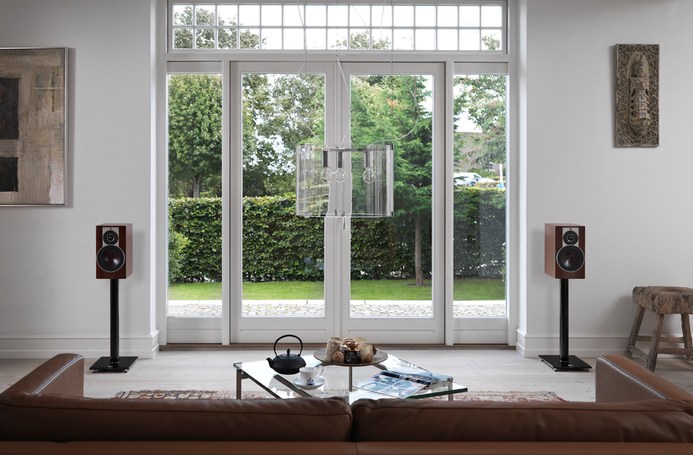
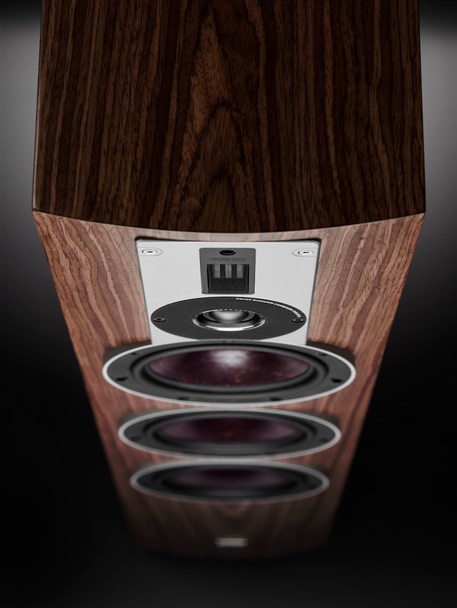
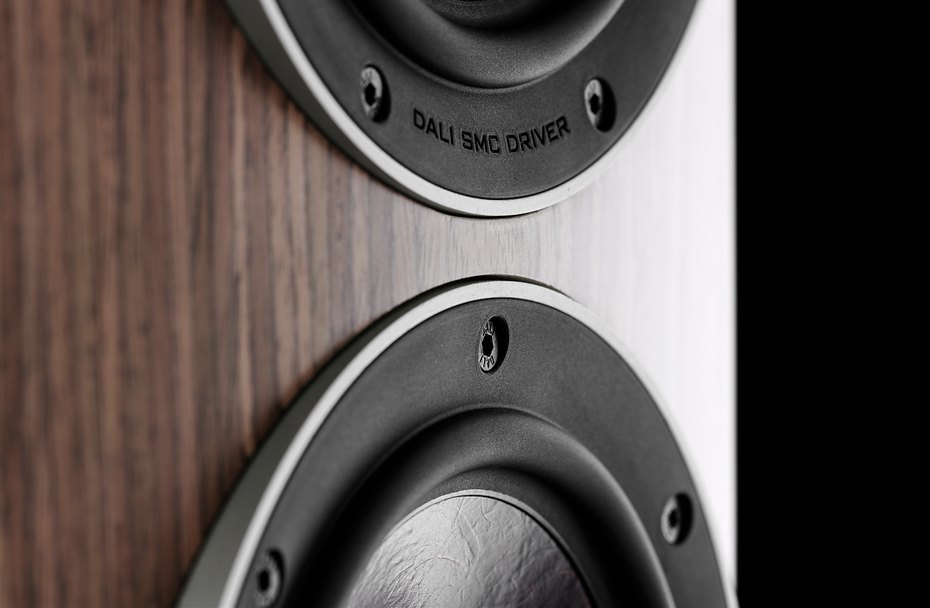
Interest?
We would be happy to inform you about Pioneer, your options, all versions, prices, etc.
Thank you very much for your inquiry!
We will get back in touch with you.
We will get back in touch with you.
INTERESTING BLOG ARTICLE
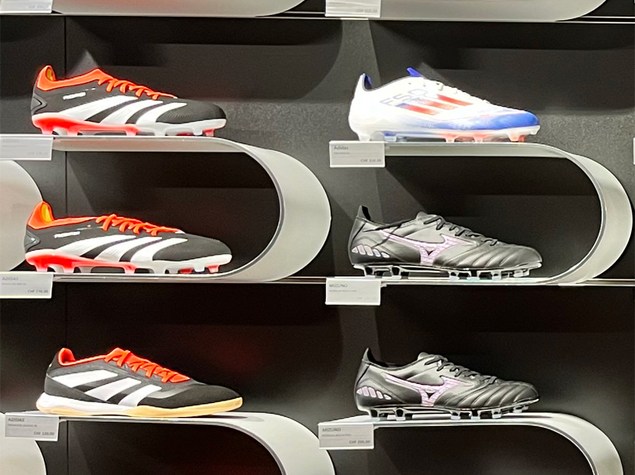
Realising Visions
Swiss Precision Meets Creative Design
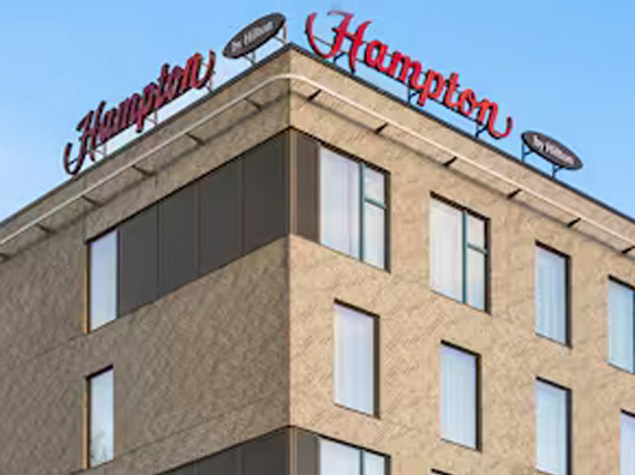
Tailor-made perfection in Estonia
Haapsalu Uksetehase AS Manufactures Doors for Hampton by Hilton
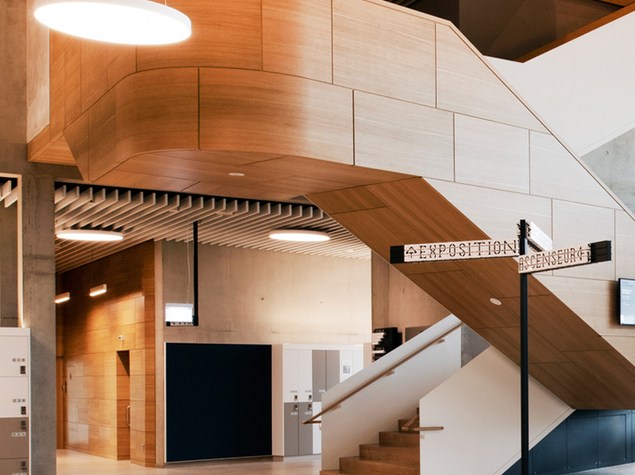
Premium Interior Fittings and Yacht Furnishings
A Vacuum Press has supported Der Ernzerhof for many years
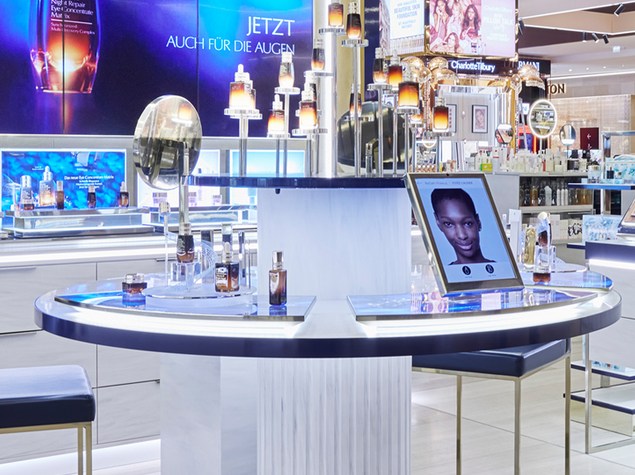
Outstanding Shopfitting with Vacuum
"außerdem" utilizes the advantages of a vacuum press by Columbus
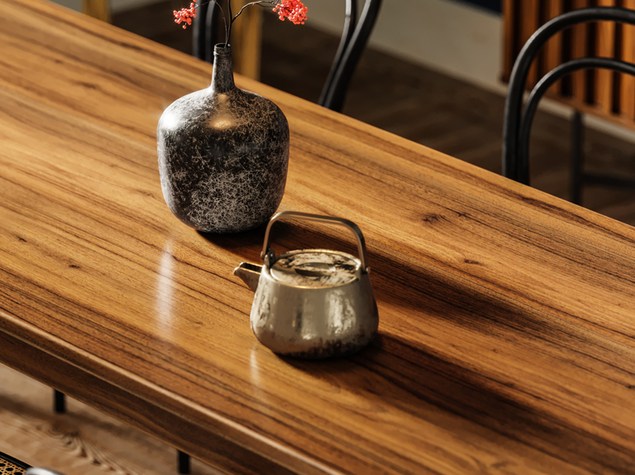
Flat veneering with vacuum
The use of a vacuum press as a veneer press
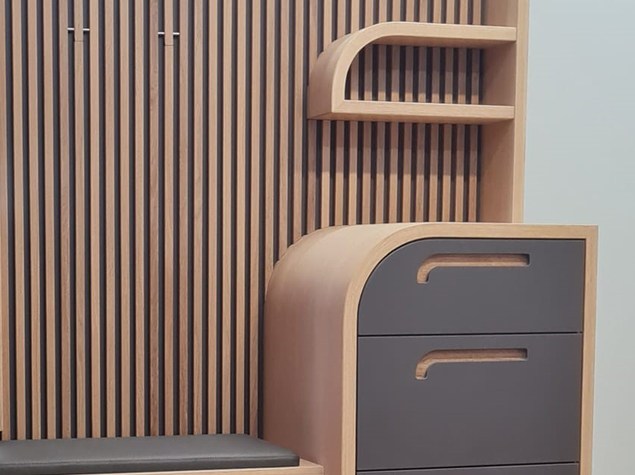
Masterful craftsmanship
The Wardrobe for the Master Carpenter Exam
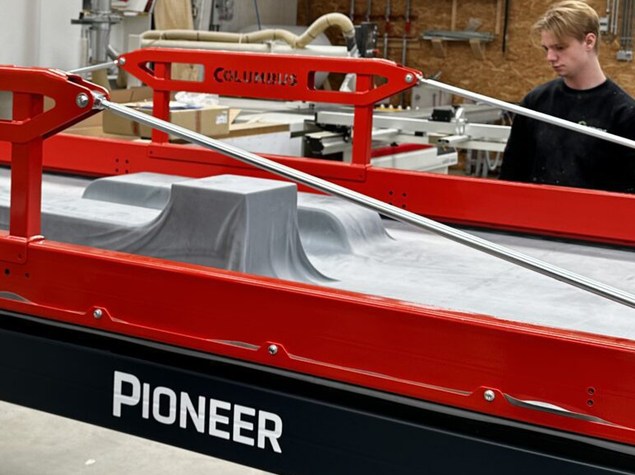
“It presses both flat and curved shapes”
Clairhout Interieur: A Revolution in Interior Design
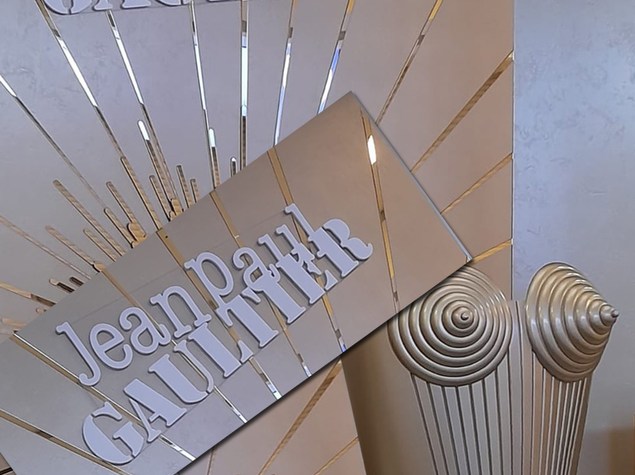
Columbus customer creates artistic masterpiece
Advertisement for Jean Paul Gaultier in Santiago de Chile

Beautiful Gift Idea
My Esel – exceptional bicycles & e-bikes
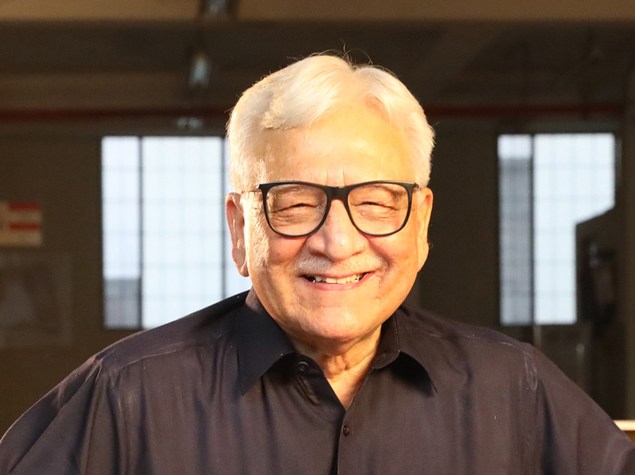
Curving the Impossible with Columbus
Interwood sets new standards with the press
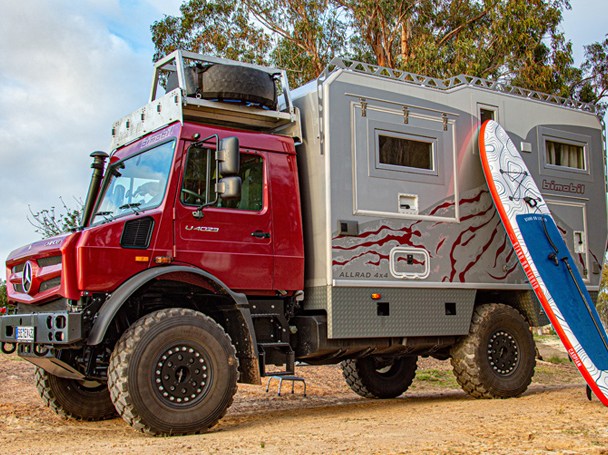
Infinity for bimobil motorhomes
Large-scale perfection for high-gloss paint
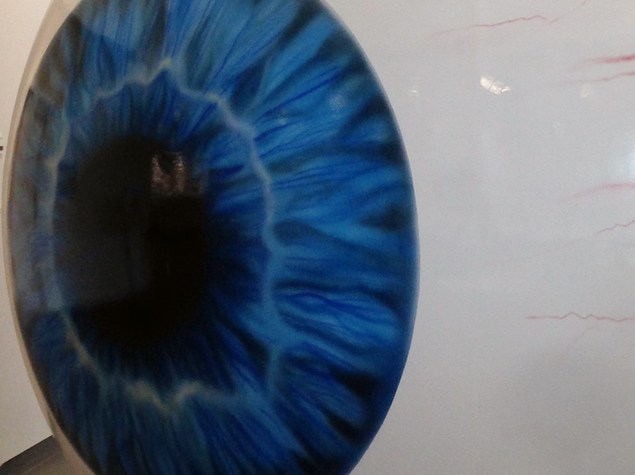
Precession and art from vacuum
Impressive eye model for the university clinic
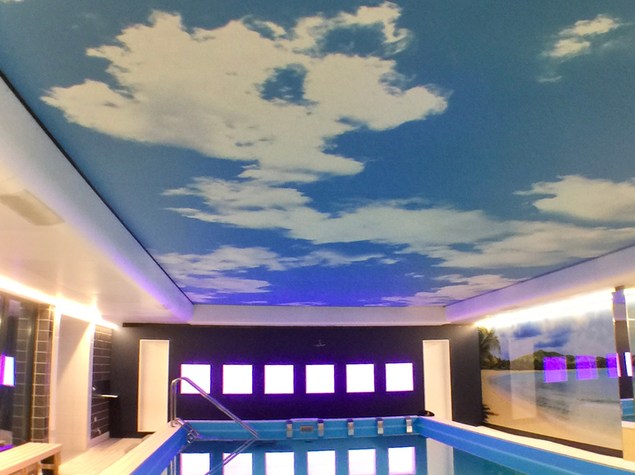
From the fruit bowl to the ceiling construction
The possible applications of a vacuum press
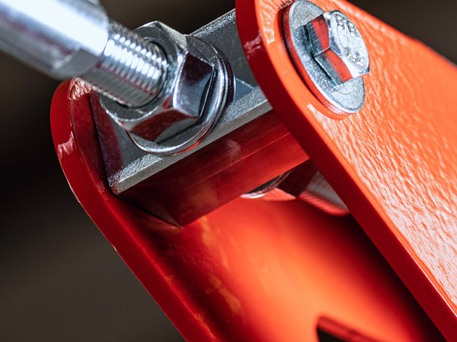
The Columbus Pressure Shifting Tool
So that natural rubber does not deform steel
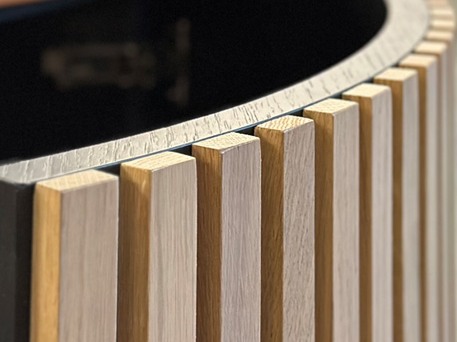
Kempa from Belgium invests in 2 vacuum presses
Round & curved shapes for modern interior design
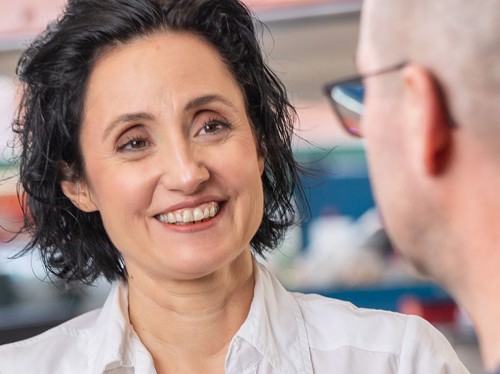
A patent for the modular system
Everyone said it doesn't work - I believed in it
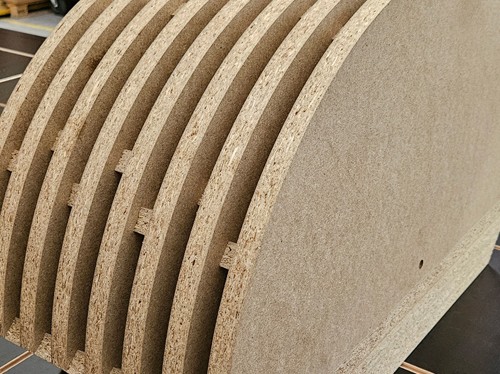
Columbus: Tips and Tricks from Practice
Mold making for mold bonding with vacuum
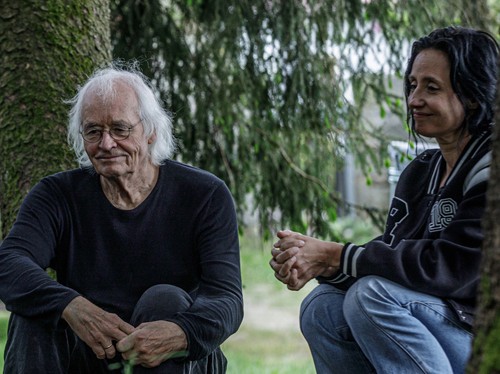
A look behind the scenes at Columbus
Thank you Dad, for a wonderful journey with you
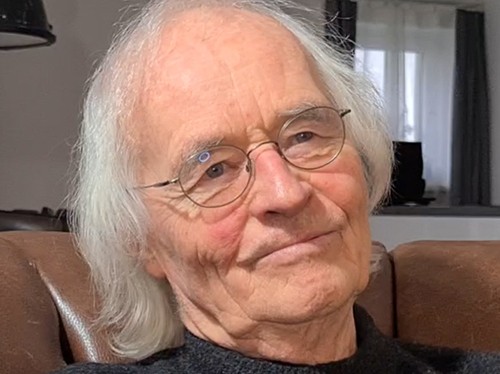
A look behind the scenes at Columbus
Günther Vetter - the invention of the vacuum bag
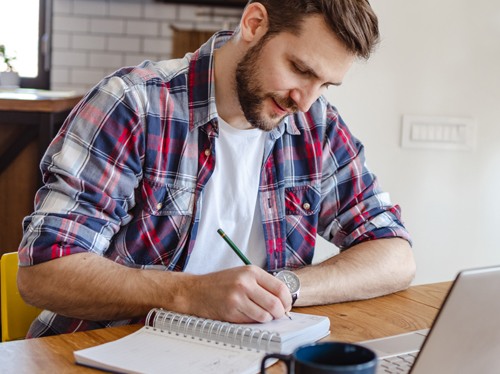
Protect your employees and your company
EU-mandated training for PUR hot melt adhesives
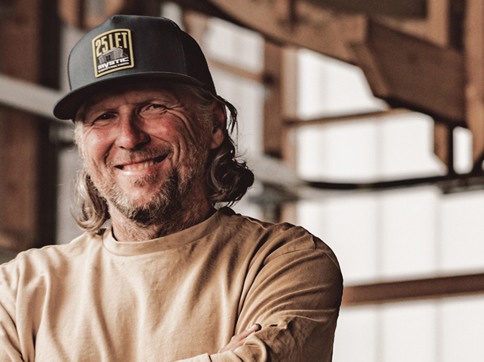
Skateboard ramps with the vacuum press Pioneer
Andreas Schützenberger does great things
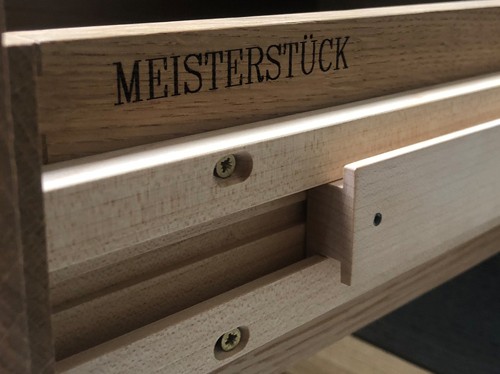
Vacuum bag: ZOSIA by Robert Nößler
His masterpiece with nostalgia and a secret
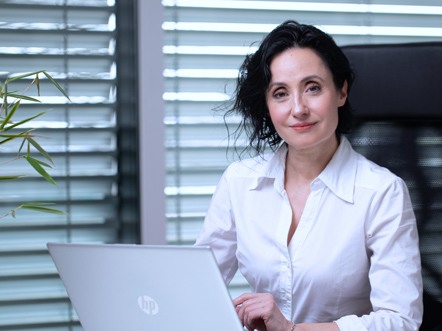
What are the benefits of a vacuum press?
Not only to cover curved workpieces and veneer

Report: International Fair in May 2023
Great success at the LIGNA in Hanover
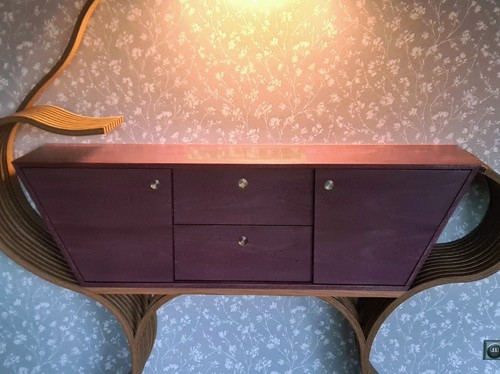
Vacuum bag: Modern Drop by Lars Hackl
Layer bonding for the next masterpiece
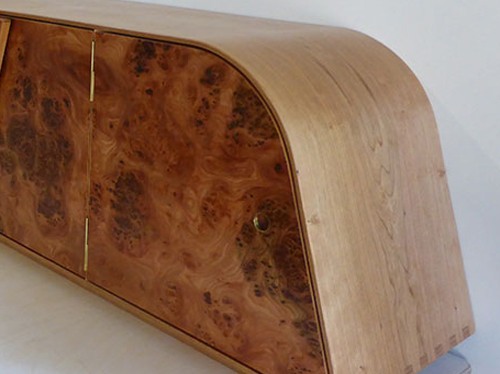
Vacuum bag: masterpiece by Tommy Kairat
First-class form veneering with Vacuflex
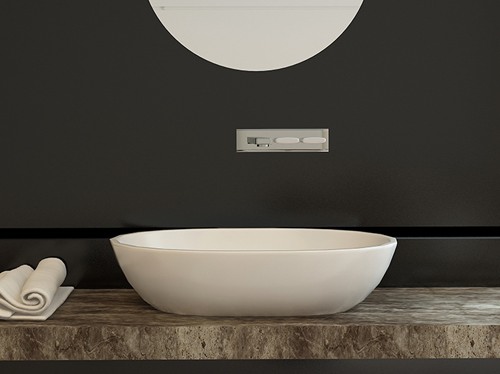
Forming of solid surface materials
Utilizing the great potential of a vacuum press
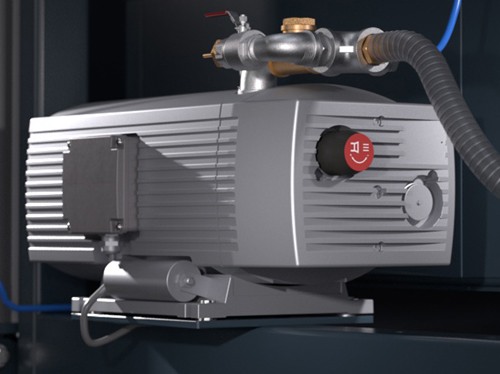
Vacuum pumps: an objective comparison
Columbus shows the advantages of dry runners
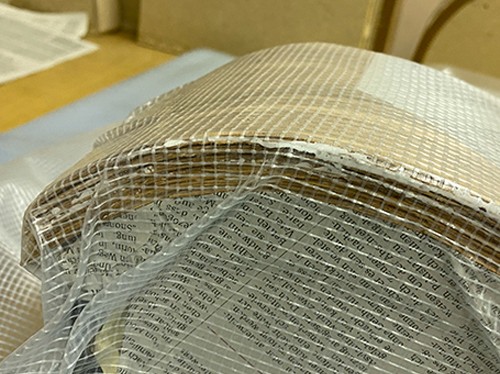
Free creativity in the creating process
Students from the Waldorfschule Mainz
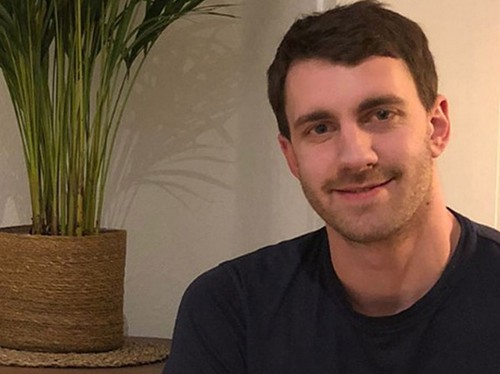
Vacuum bag: Markus Kramer's masterpiece
His vision brings the French past into the present
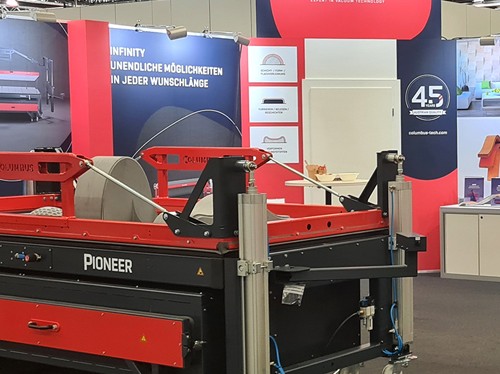
That was the Holz-Handwerk 2022
PIONEER and MOVE: Spectacular success at the fair
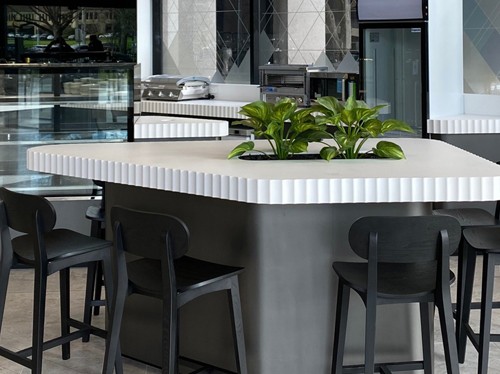
The magic lies in the perfect details
LL Installations creates high-quality accents
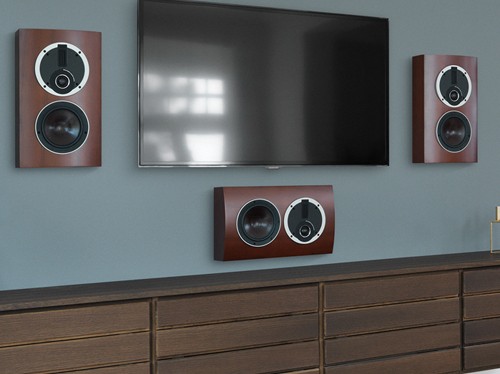
Handmade speakers from Denmark
One million satisfied DALI customers in over 70 countries
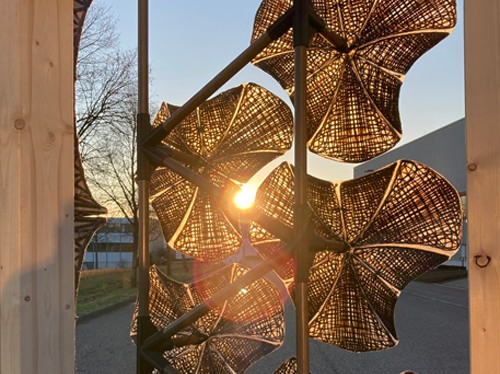
Columbus & University of Stuttgart
Artworks - Innovation meets Science
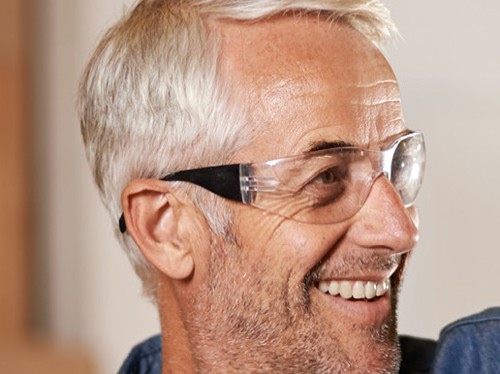
Independence from suppliers
6 Reasons to buy a Vacuum Press from Columbus
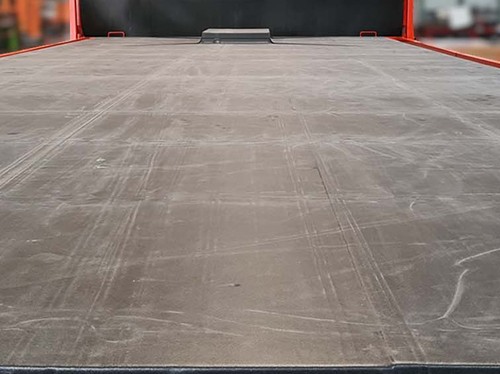
The Birth of Infinity Vacuum Press
Flexstone produces large parts for houseboats
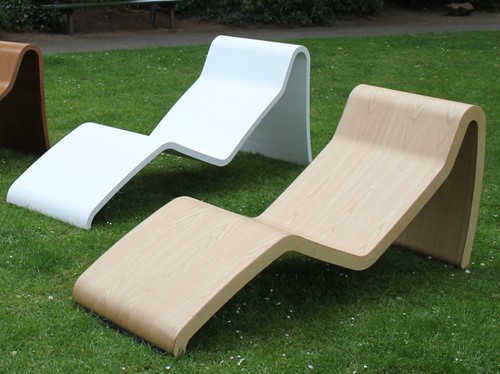
Sound loungers - feel the music
Magnus Hoffmann has developed something creative
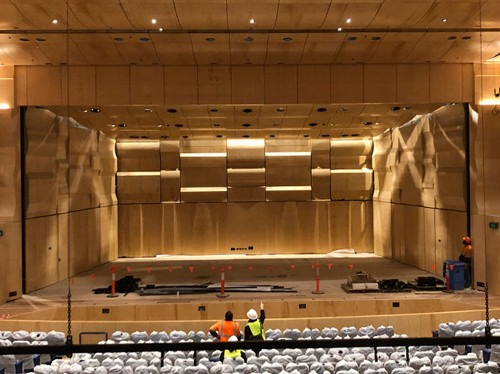
Excellence as far as the eye can see
Acoustic panels for the Leonardian Center in Australia
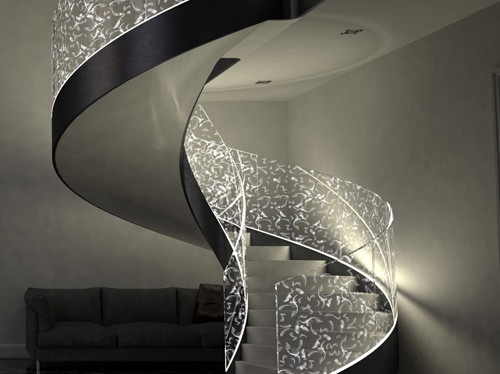
A dazzling cooperation between two pioneers
Vacuum - Acrylic glass - Unlimited possibilities
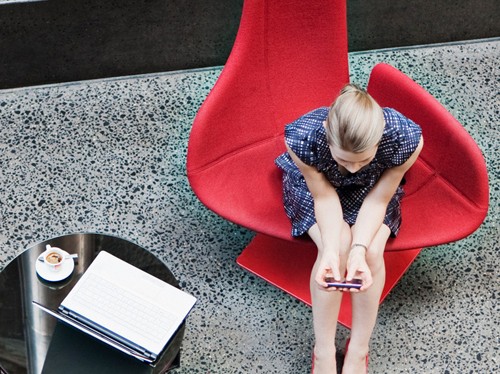
NOW: Individual. Exceptional. Unique.
Vacuum: Best performance from batch size 1
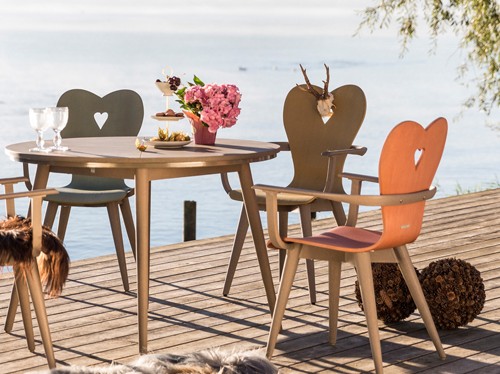
A compound better than wood
Resysta: Design meets sustainability
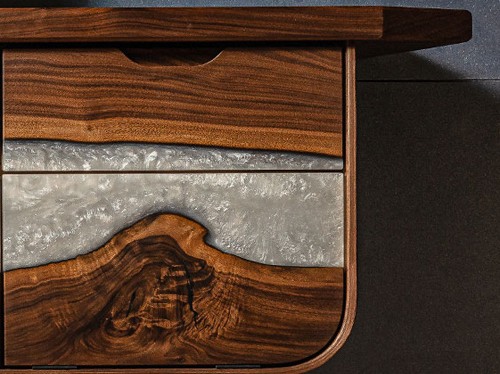
Vacuum bag: White River by Jannik Otte
Masterpiece as an eye-catcher for the entrance area
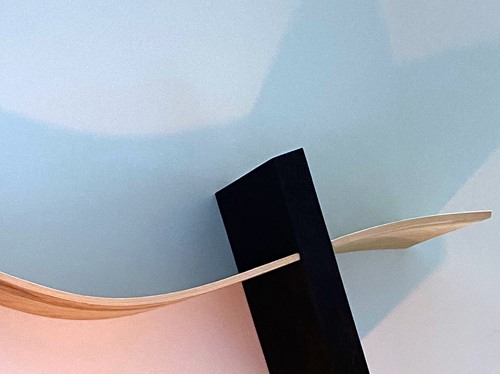
Young creativity conquers the world
Fascinating - these are students - not carpenters
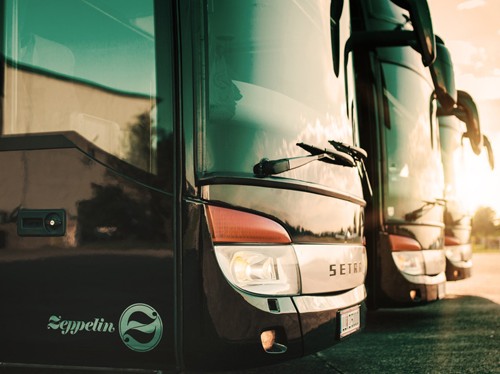
Full speed ahead with a vacuum press
Tour buses for the biggest stars in the world
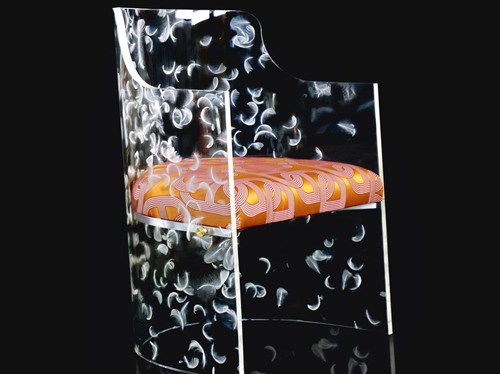
World premiere: acrylic glass chair
Customer Zöllner manufactures for Acrylic Couture
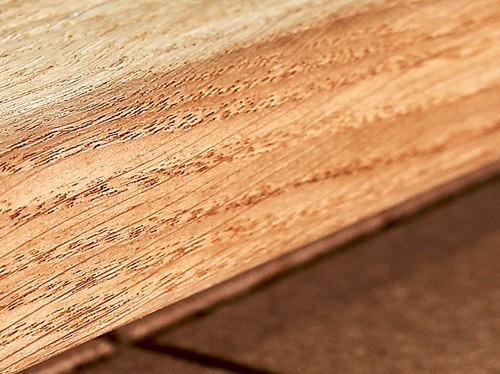
Columbus makes the impossible possible
VIDEO: Seamless veneering in just a few working steps
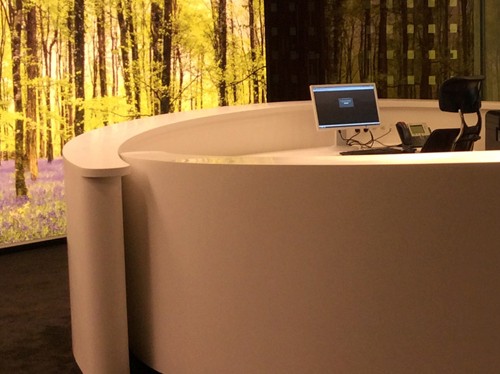
Columbus forms Kerrock in Belgium
An exceptional design future with vacuum presses
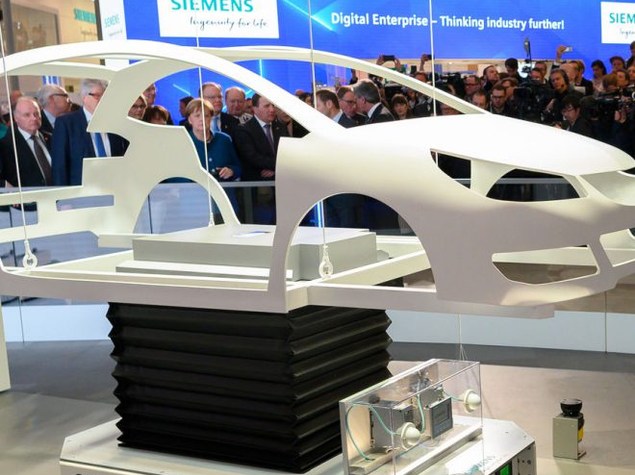
Exhibition builder Prager manufactures for Siemens
An innovative exhibition stand based on vacuum
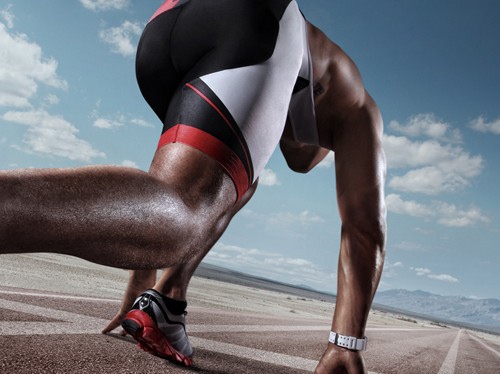
New times bring new opportunities
Conquering existing markets with new applications
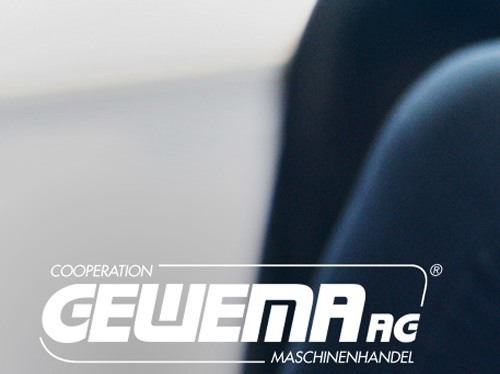
Columbus expands its global dealer network
GEWEMA membership for Columbus Vacuum Presses
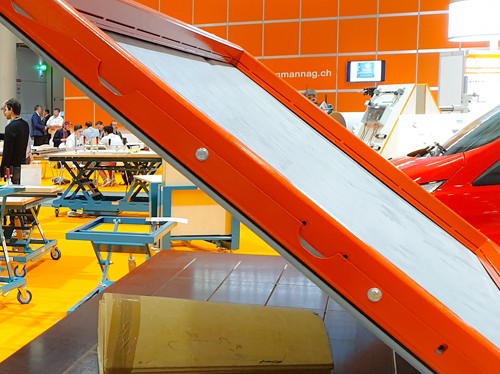
That was the Holz 2019 in Basel
Columbus and the great Swiss carpenters
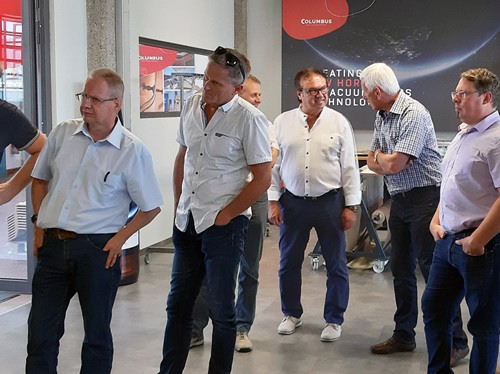
Cooperation with Schachermayer
Columbus receives another strong partner
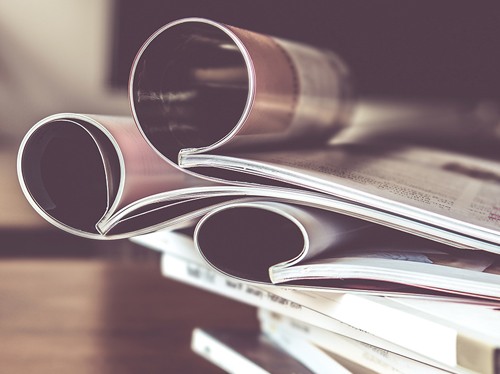
Press: People talk about Columbus
What is published in professional circles about us
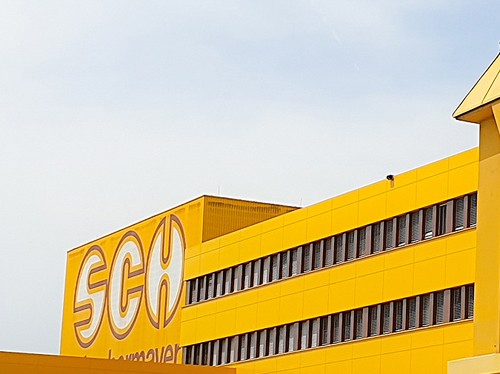
MEETING POINT NOBLE VENEER
Visiting the Schachermayer company
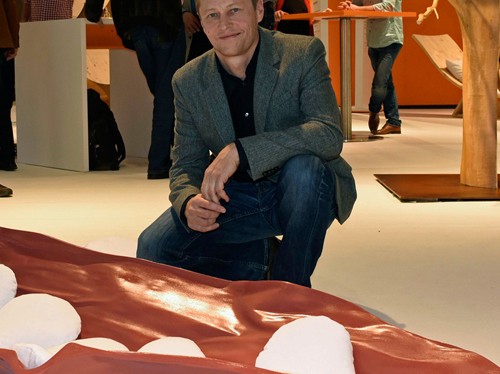
An Honor through Vacuum Technology
A chili as a creative lounge furniture is the winner
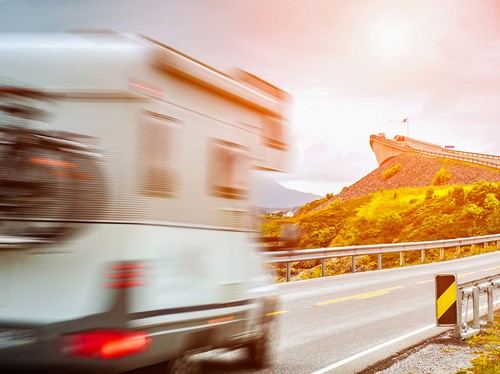
Hymer - a success story with vacuum
The well-known producer works with Columbus
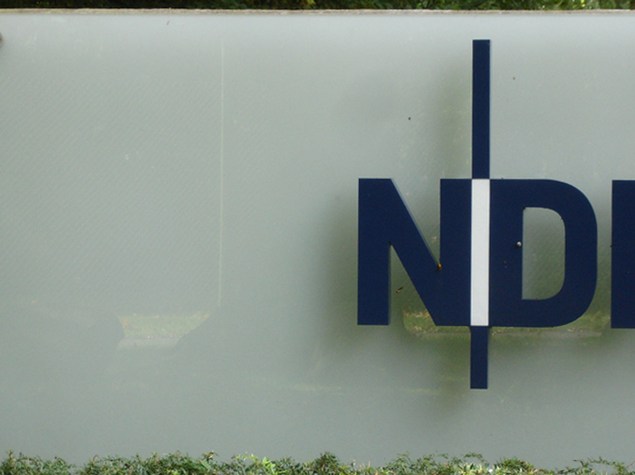
The NDR works with a vacuum press
The Tagesschau desk was produced with Columbus
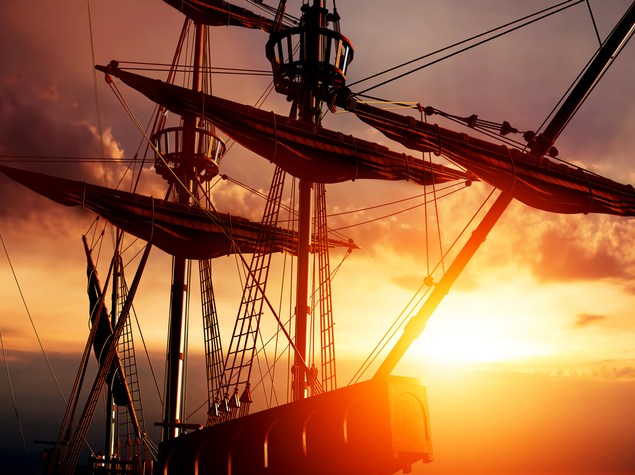
Why we are called what we are called
What Christopher Columbus has to do with Columbus