Innovation meets science!
Made with Pioneer - innovative artworks made from biocomposite facade panels
As everyone knows, the spirit of innovation has always been practiced at Columbus just like traditional craftsmanship. We inspire people all over the world to break new ground and create new things. In this blog article we would like to emphasize that vacuum technology from Columbus is also perfectly suited for use at an academic level. Our customer, the BioMat research group at the University of Stuttgart, gives exciting insights into why the vacuum press Pioneer is the perfect companion on new paths. The information comes directly from BioMats research associate Dr.-Ing. arch. Jan Petrš. You may be curious!
BioMat - Pioneers in the field of sustainable materials
What exactly is the BioMat? The department Biobased Materials and Materials Cycles in Architecture (BioMat) is located at the Institute of Building Structures and Structural Design (ITKE) at the Faculty for Architecture and Urban Planning of the University of Stuttgart. The department headed by Jun.-Prof. Dr.-Ing. Hanaa Dahy has the goal to merge the areas design, sustainable material development, form finding and much more in architecture. Teaching, research, material development and production as well as industrial projects are closely linked. BioMat thus offers architecture students and industrial partners the opportunity to participate in current research projects.
Innovative techniques, new insights, extraordinary artworks
As part of the course "Digital design and fabrication of biocomposite facade panels", BioMat used its Columbus vacuum press Pioneer as well as outstanding manufacturing processes far from the usual standard to produce truly beautiful artworks. How exactly, you will find out now!
As a starting point, panels were manufactured using the Tailored Fiber Placement (TFP) method. In this process, natural fibers are placed in specific directions based on their geometry and structural performance. The dry fiber TFP preforms were then infused with resin and placed on molds or curing frames. The final shaping was done through a variety of processes, three of which were performed using our Pioneer vacuum press. Understandable, because the vacuum technology in particular made it possible to press the panels onto both double-curved molds and flat wooden panels. The pressing process was also used for the perfect lamination of sandwich panels with a balsa core between two biocomposite panels. In all cases, the biocomposite cured during vacuum pressing – no additional heating was applied throughout the project. Pioneer's long operating times were also decisive, as the machine often ran for around 12 hours.
Sustainable and innovative unique pieces with Columbus Pioneer
The BioMat research group informed us that Pioneer was ideally suited for use in this innovative project. Our designers are also happy about that. Pioneer was created precisely for this level of precision and versatility, while at the same time being easy to use. So you can concentrate on what is important.
Many thanks to the BioMat of the University of Stuttgart for sharing this wonderful success story with us.
© credits for photographs: Photographs by BioMat at ITKE, University of Stuttgart
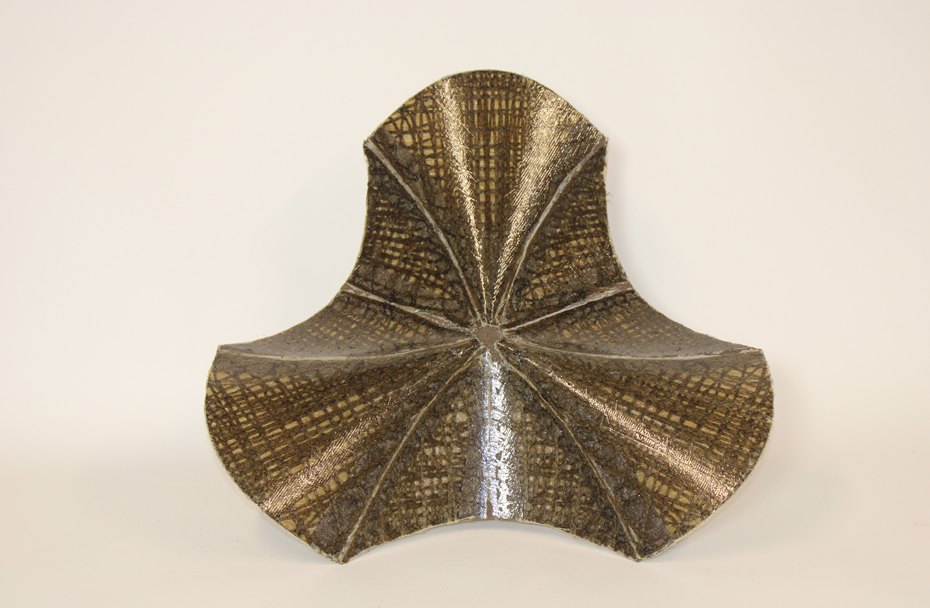
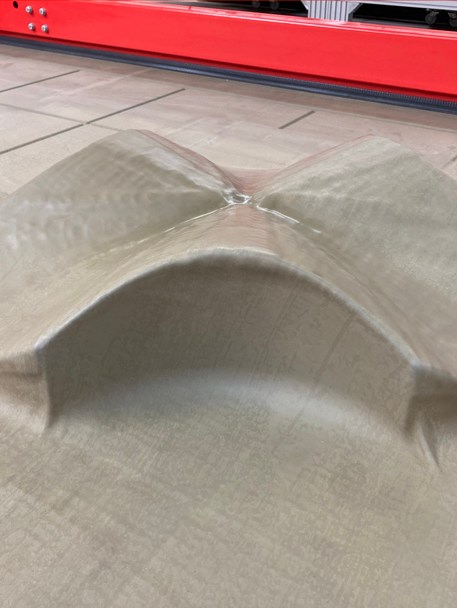
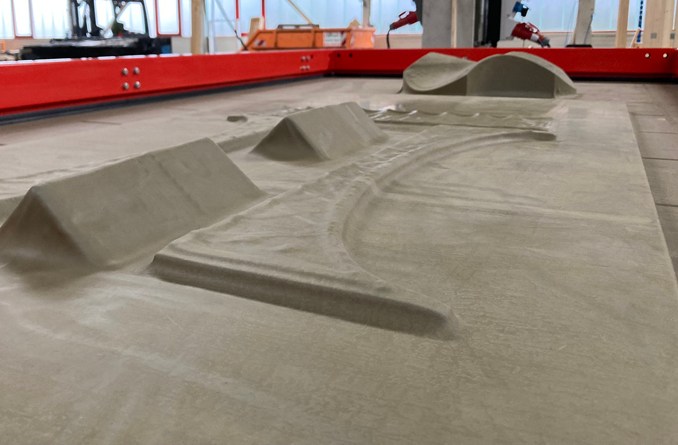
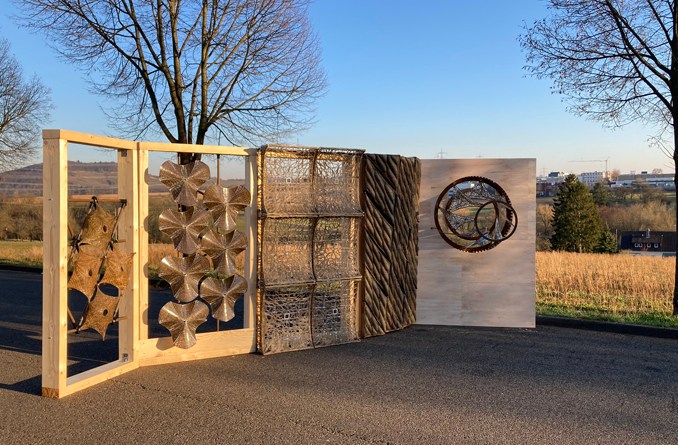
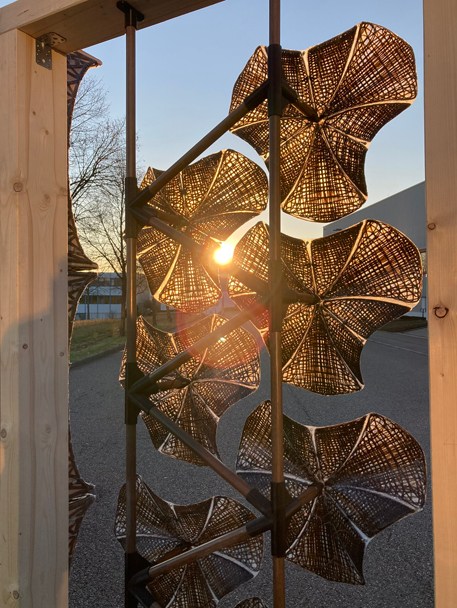
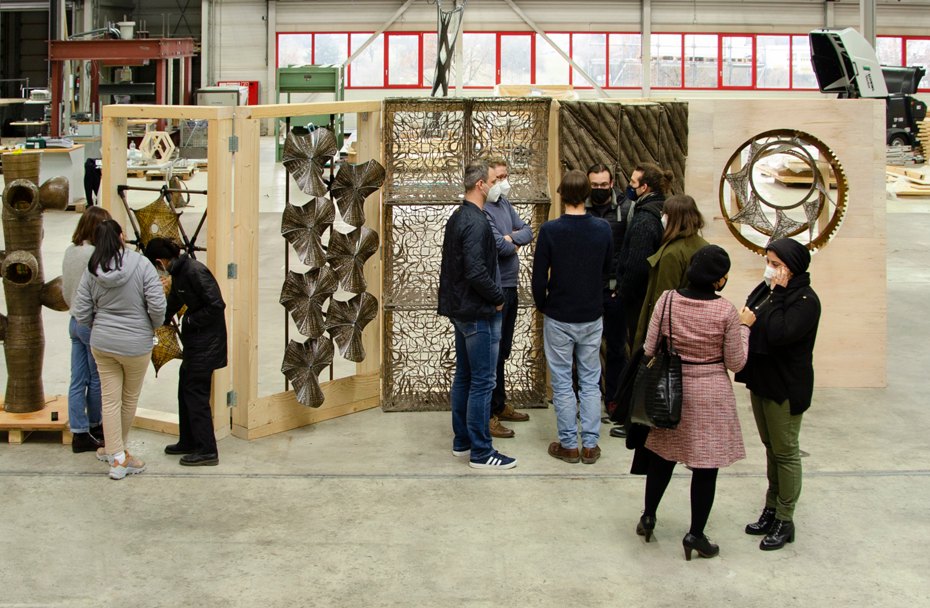
Interest?
If you would like to know more about the PIONEER modular system, we would be happy to provide you with more information!
Thank you very much for your inquiry!
We will get back in touch with you.
We will get back in touch with you.
INTERESTING BLOG ARTICLE
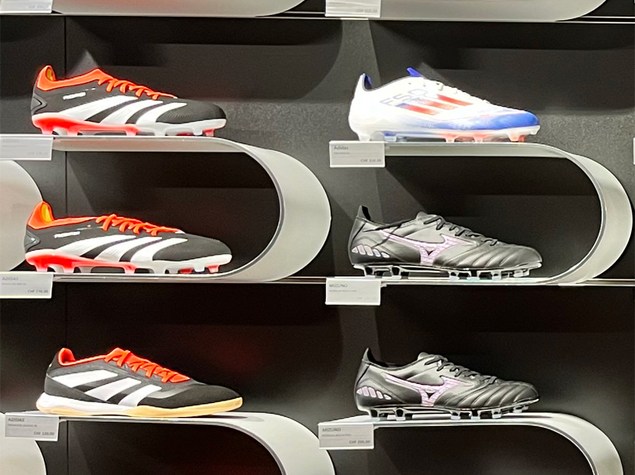
Realising Visions
Swiss Precision Meets Creative Design
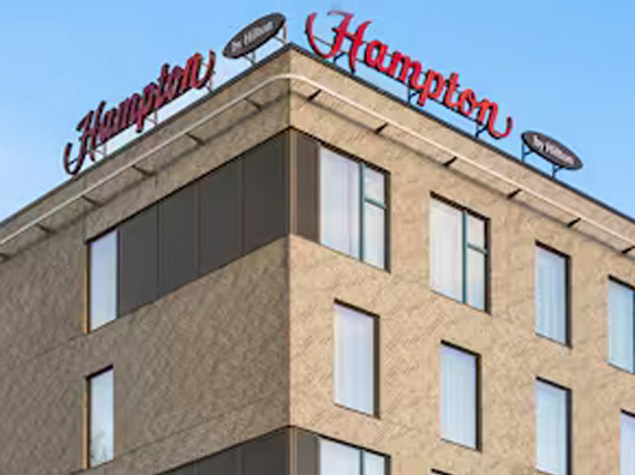
Tailor-made perfection in Estonia
Haapsalu Uksetehase AS Manufactures Doors for Hampton by Hilton
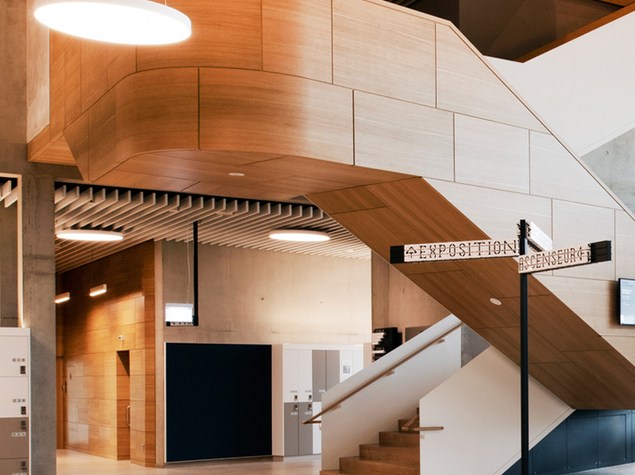
Premium Interior Fittings and Yacht Furnishings
A Vacuum Press has supported Der Ernzerhof for many years
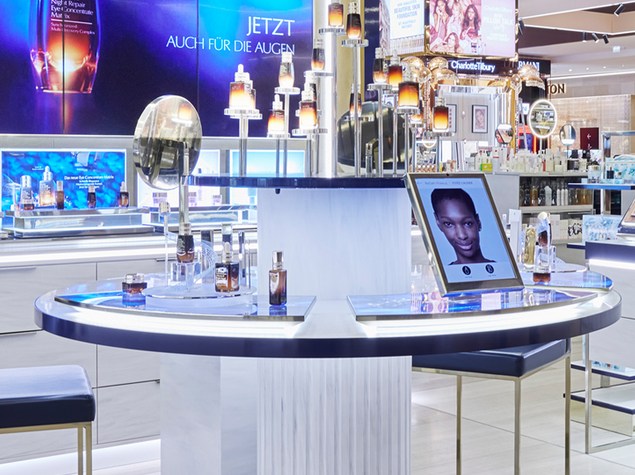
Outstanding Shopfitting with Vacuum
"außerdem" utilizes the advantages of a vacuum press by Columbus
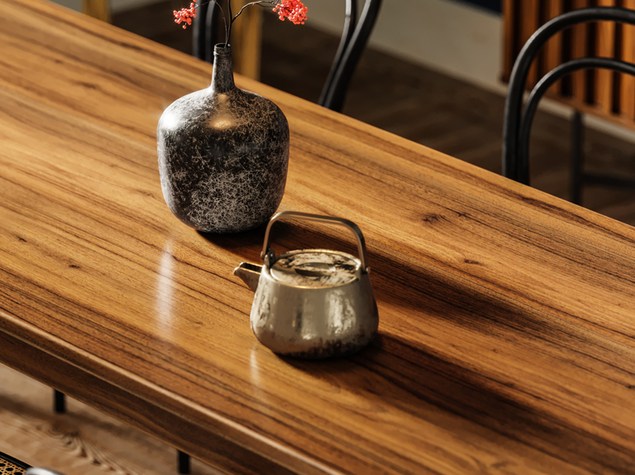
Flat veneering with vacuum
The use of a vacuum press as a veneer press
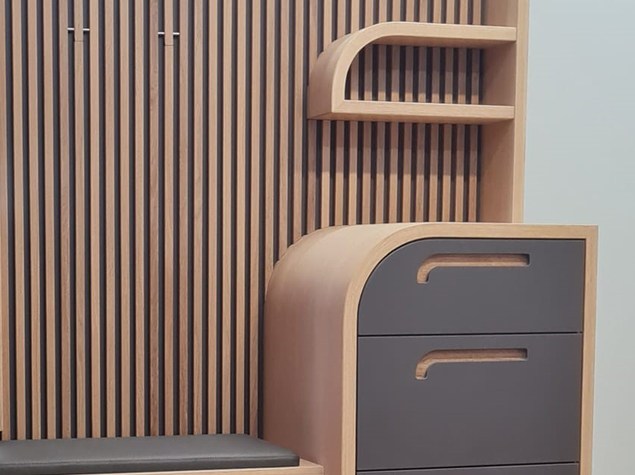
Masterful craftsmanship
The Wardrobe for the Master Carpenter Exam
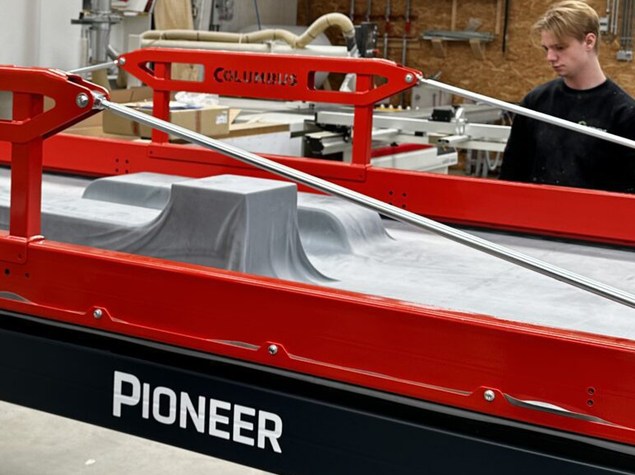
“It presses both flat and curved shapes”
Clairhout Interieur: A Revolution in Interior Design
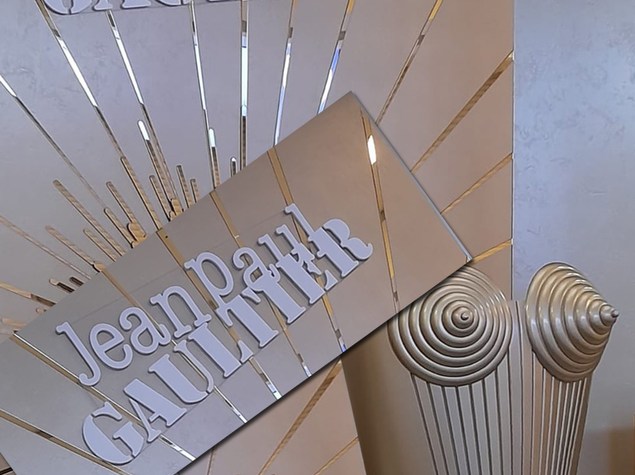
Columbus customer creates artistic masterpiece
Advertisement for Jean Paul Gaultier in Santiago de Chile

Beautiful Gift Idea
My Esel – exceptional bicycles & e-bikes
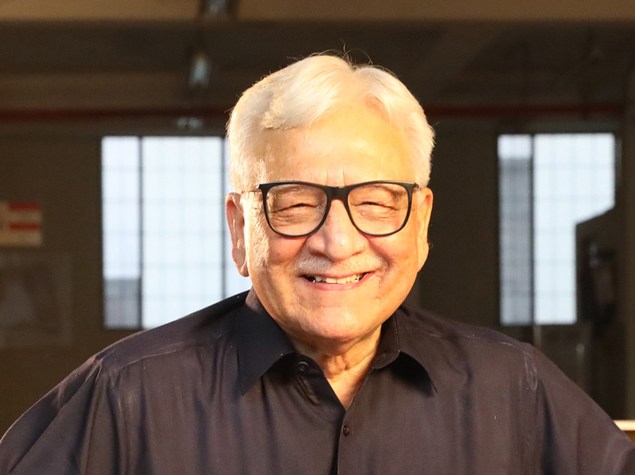
Curving the Impossible with Columbus
Interwood sets new standards with the press
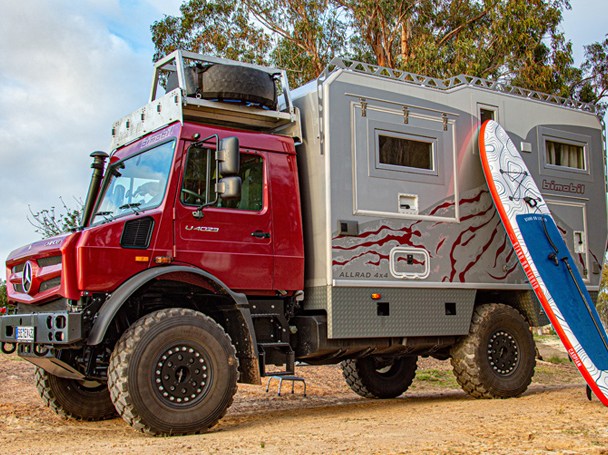
Infinity for bimobil motorhomes
Large-scale perfection for high-gloss paint
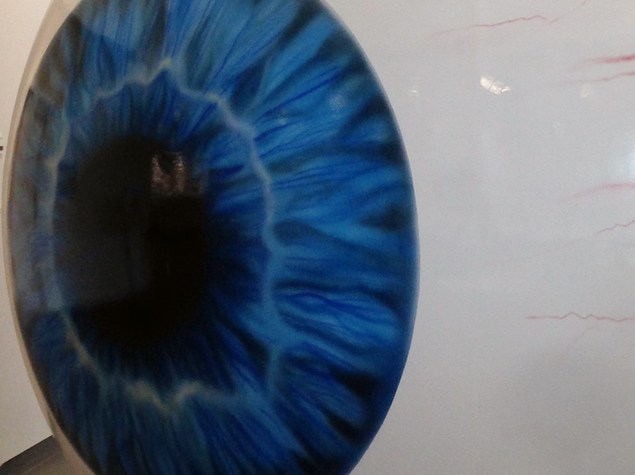
Precession and art from vacuum
Impressive eye model for the university clinic
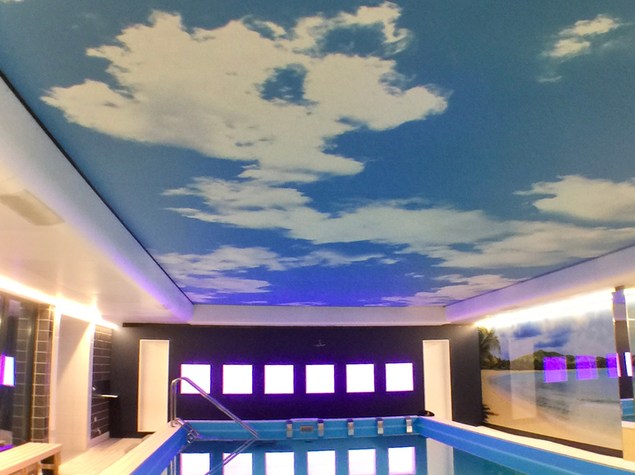
From the fruit bowl to the ceiling construction
The possible applications of a vacuum press
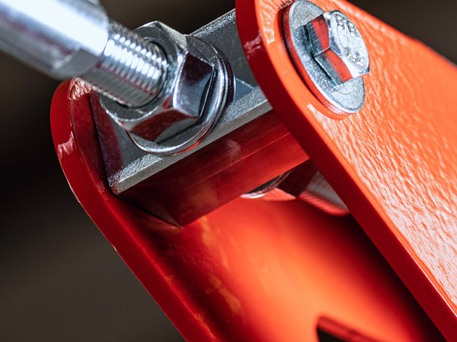
The Columbus Pressure Shifting Tool
So that natural rubber does not deform steel
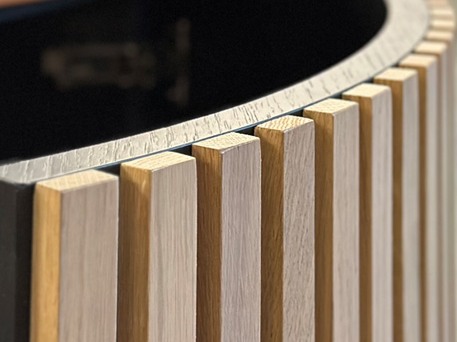
Kempa from Belgium invests in 2 vacuum presses
Round & curved shapes for modern interior design
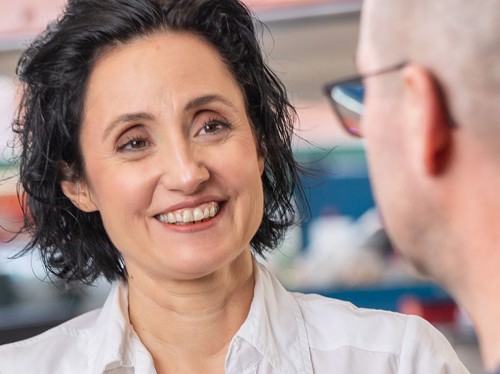
A patent for the modular system
Everyone said it doesn't work - I believed in it
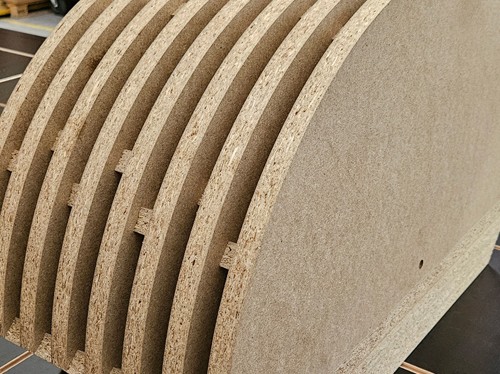
Columbus: Tips and Tricks from Practice
Mold making for mold bonding with vacuum
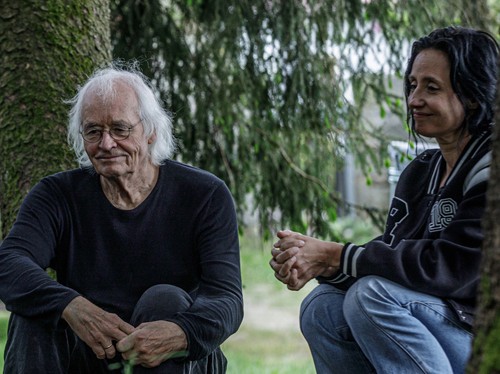
A look behind the scenes at Columbus
Thank you Dad, for a wonderful journey with you
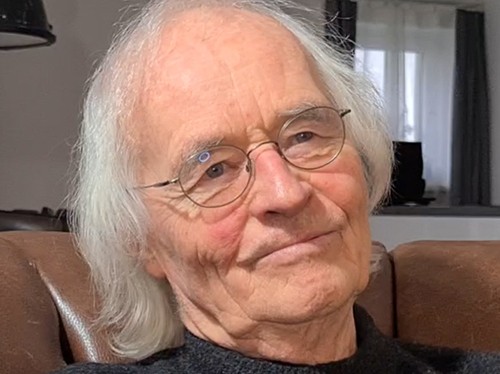
A look behind the scenes at Columbus
Günther Vetter - the invention of the vacuum bag
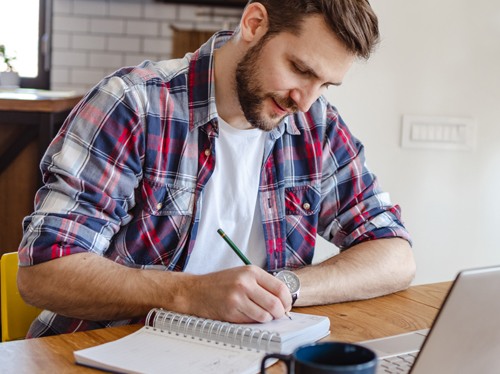
Protect your employees and your company
EU-mandated training for PUR hot melt adhesives
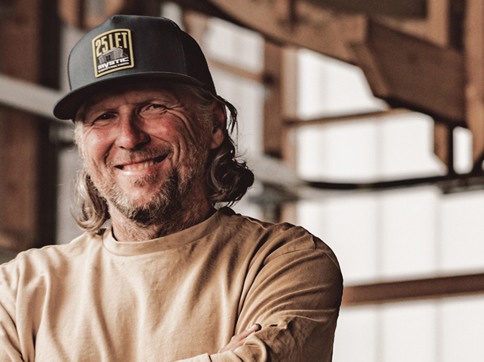
Skateboard ramps with the vacuum press Pioneer
Andreas Schützenberger does great things
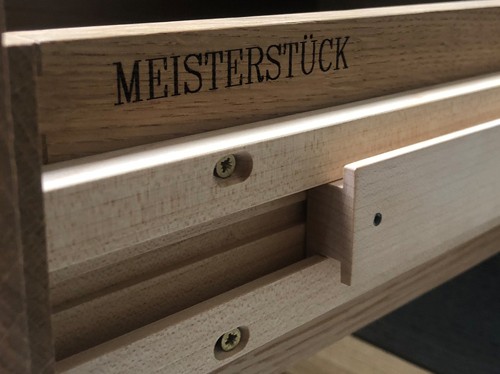
Vacuum bag: ZOSIA by Robert Nößler
His masterpiece with nostalgia and a secret
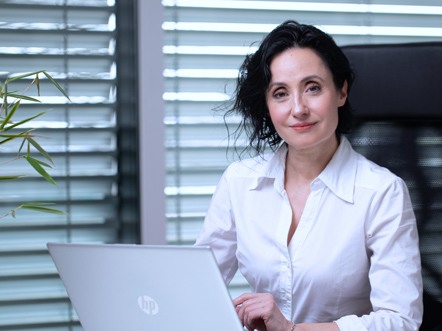
What are the benefits of a vacuum press?
Not only to cover curved workpieces and veneer

Report: International Fair in May 2023
Great success at the LIGNA in Hanover
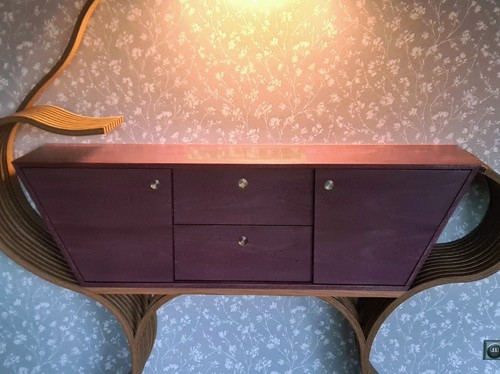
Vacuum bag: Modern Drop by Lars Hackl
Layer bonding for the next masterpiece
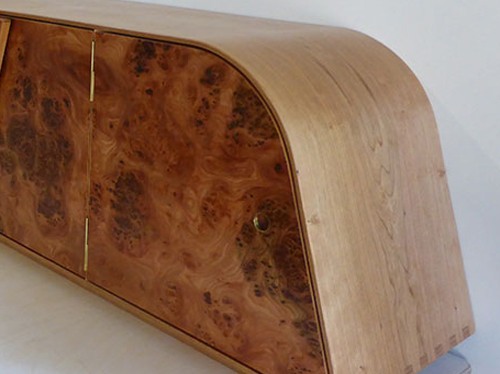
Vacuum bag: masterpiece by Tommy Kairat
First-class form veneering with Vacuflex
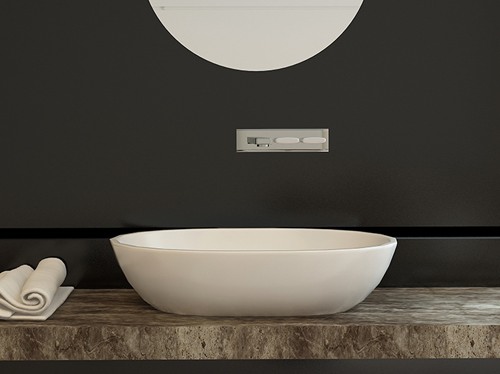
Forming of solid surface materials
Utilizing the great potential of a vacuum press
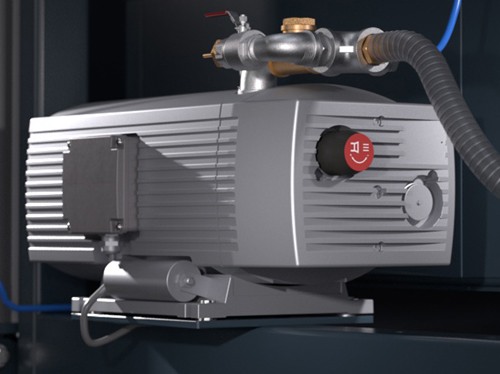
Vacuum pumps: an objective comparison
Columbus shows the advantages of dry runners
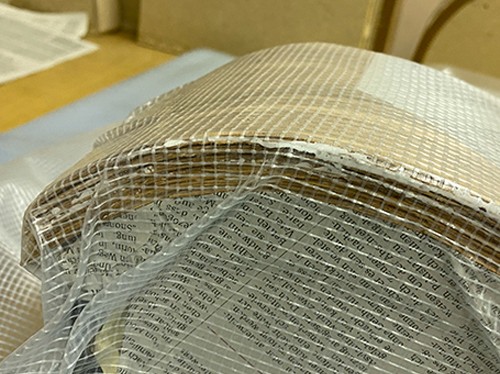
Free creativity in the creating process
Students from the Waldorfschule Mainz
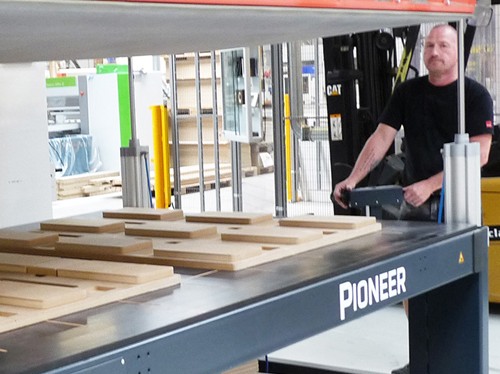
1.5 weeks instead of 6 weeks production time
Precisely curved fronts of the DALI speakers
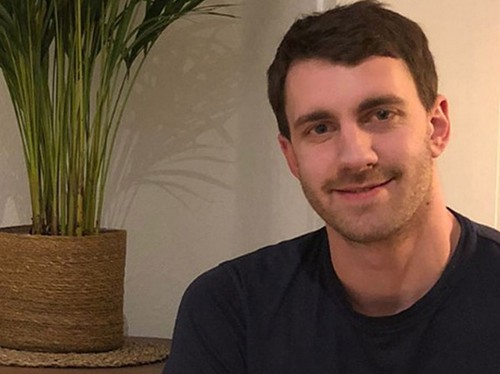
Vacuum bag: Markus Kramer's masterpiece
His vision brings the French past into the present
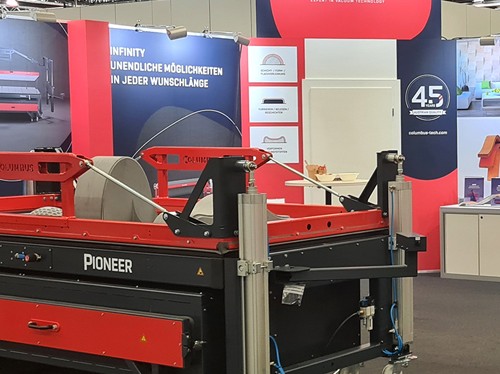
That was the Holz-Handwerk 2022
PIONEER and MOVE: Spectacular success at the fair
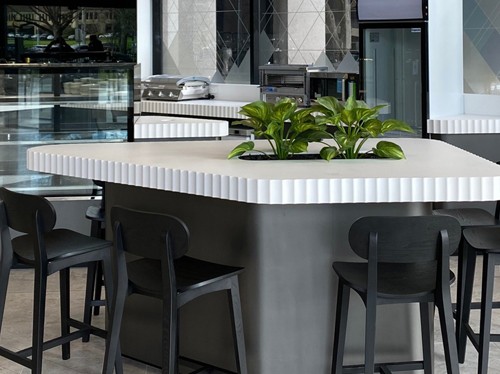
The magic lies in the perfect details
LL Installations creates high-quality accents
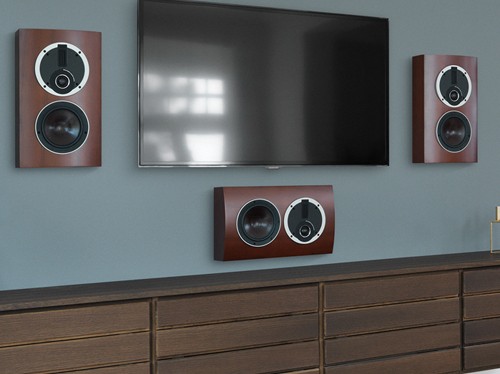
Handmade speakers from Denmark
One million satisfied DALI customers in over 70 countries
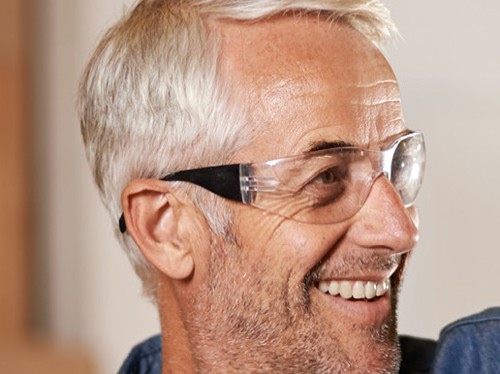
Independence from suppliers
6 Reasons to buy a Vacuum Press from Columbus
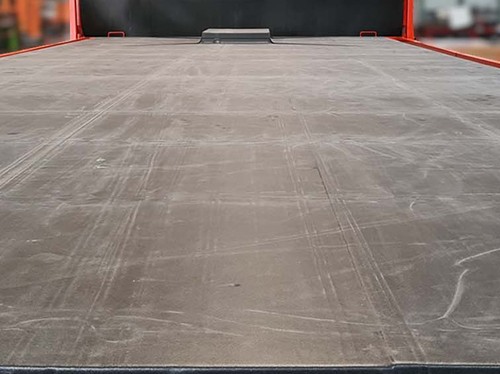
The Birth of Infinity Vacuum Press
Flexstone produces large parts for houseboats
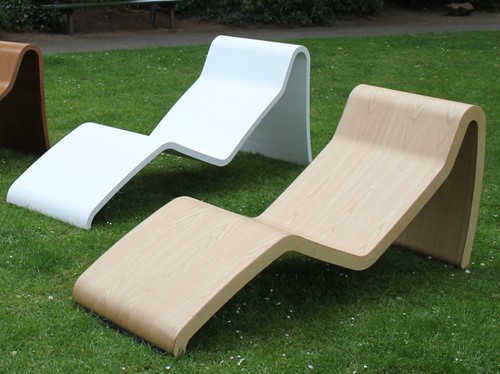
Sound loungers - feel the music
Magnus Hoffmann has developed something creative
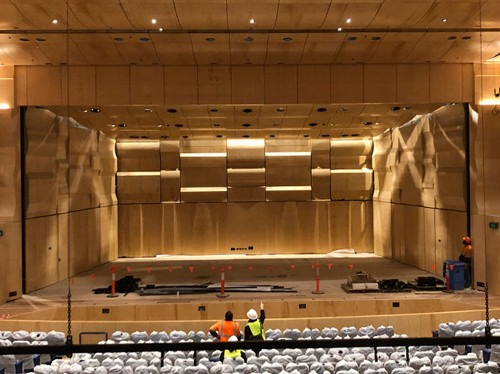
Excellence as far as the eye can see
Acoustic panels for the Leonardian Center in Australia
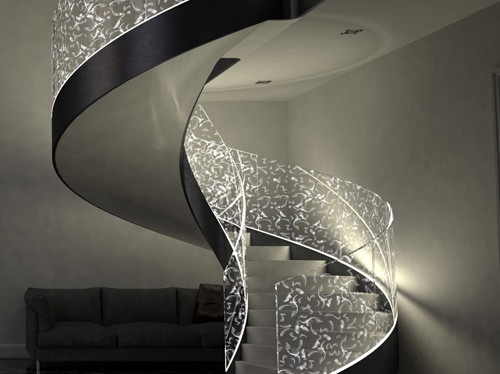
A dazzling cooperation between two pioneers
Vacuum - Acrylic glass - Unlimited possibilities
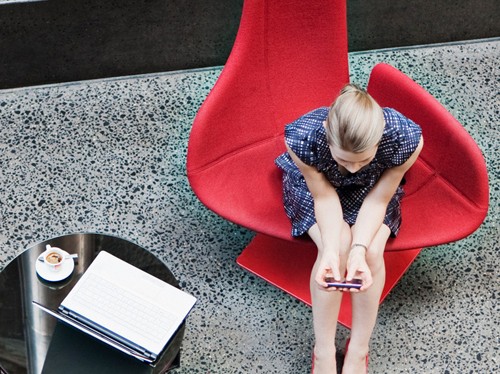
NOW: Individual. Exceptional. Unique.
Vacuum: Best performance from batch size 1
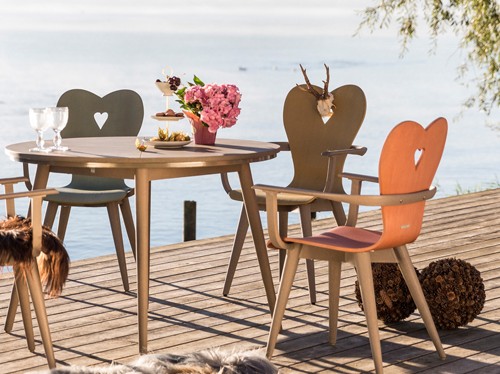
A compound better than wood
Resysta: Design meets sustainability
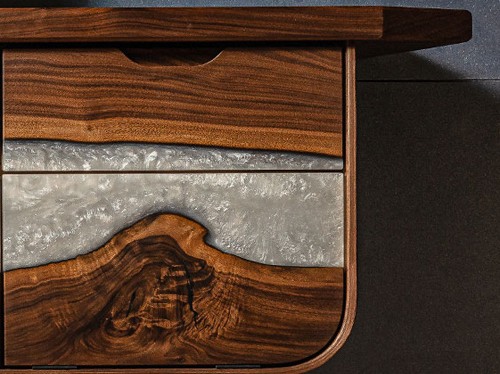
Vacuum bag: White River by Jannik Otte
Masterpiece as an eye-catcher for the entrance area
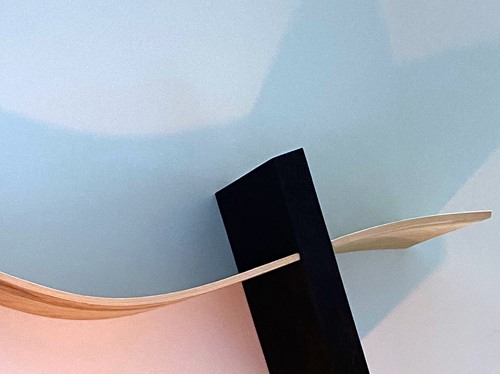
Young creativity conquers the world
Fascinating - these are students - not carpenters
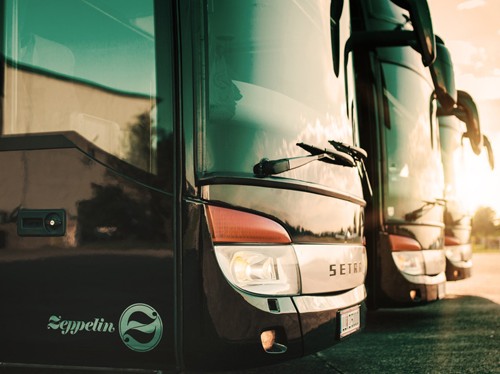
Full speed ahead with a vacuum press
Tour buses for the biggest stars in the world
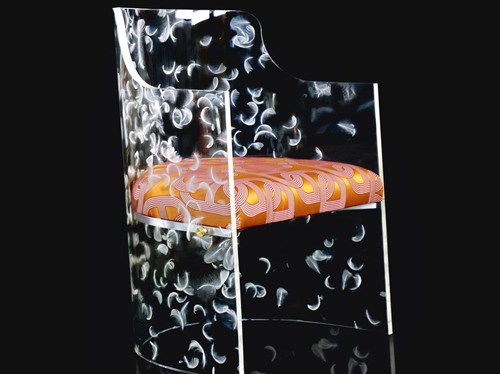
World premiere: acrylic glass chair
Customer Zöllner manufactures for Acrylic Couture
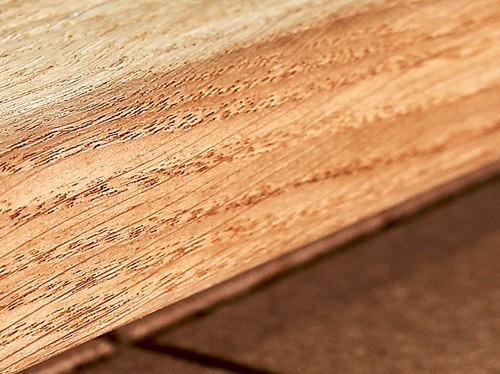
Columbus makes the impossible possible
VIDEO: Seamless veneering in just a few working steps
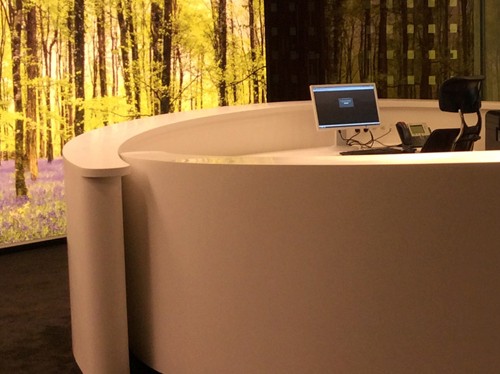
Columbus forms Kerrock in Belgium
An exceptional design future with vacuum presses
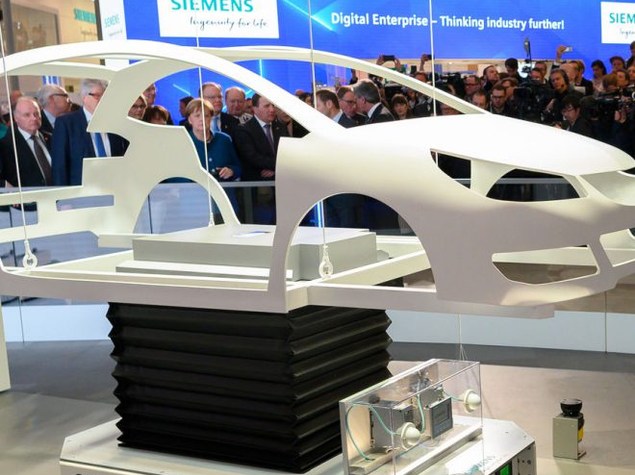
Exhibition builder Prager manufactures for Siemens
An innovative exhibition stand based on vacuum
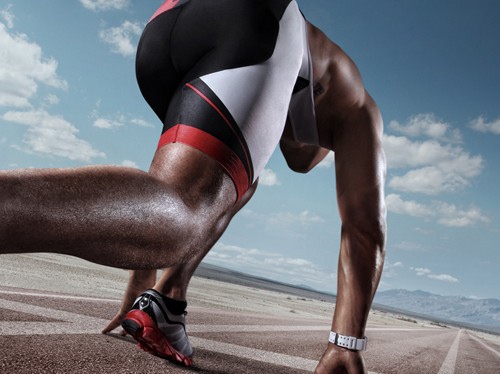
New times bring new opportunities
Conquering existing markets with new applications
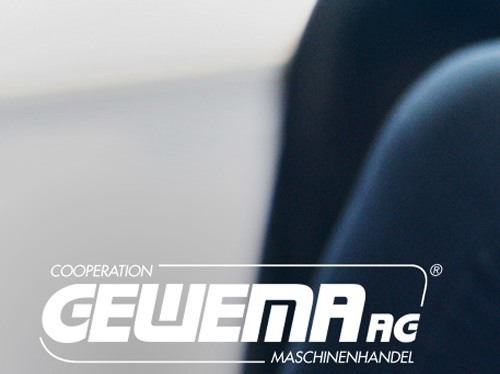
Columbus expands its global dealer network
GEWEMA membership for Columbus Vacuum Presses
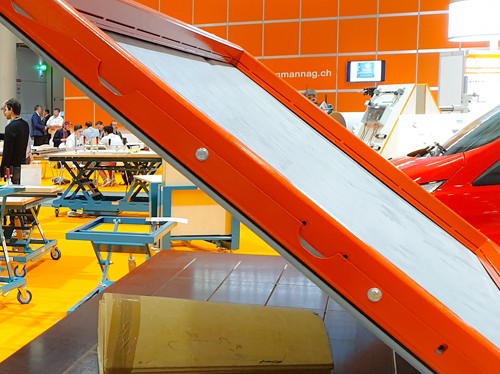
That was the Holz 2019 in Basel
Columbus and the great Swiss carpenters
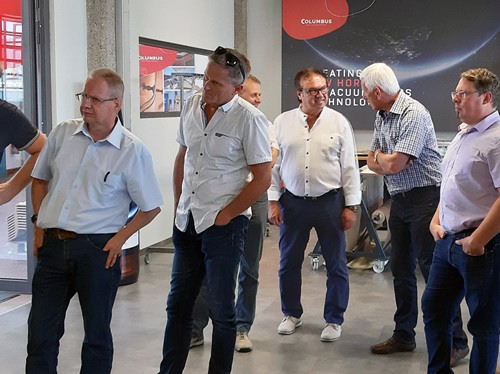
Cooperation with Schachermayer
Columbus receives another strong partner
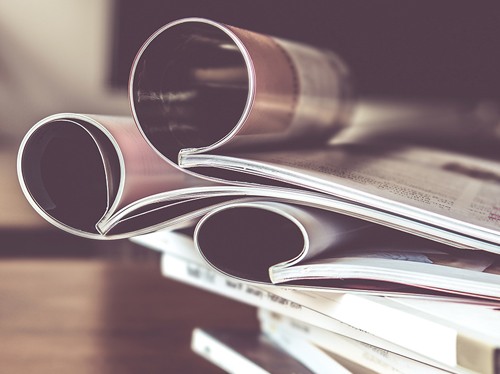
Press: People talk about Columbus
What is published in professional circles about us
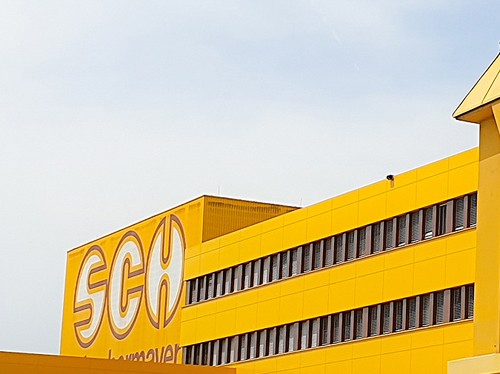
MEETING POINT NOBLE VENEER
Visiting the Schachermayer company
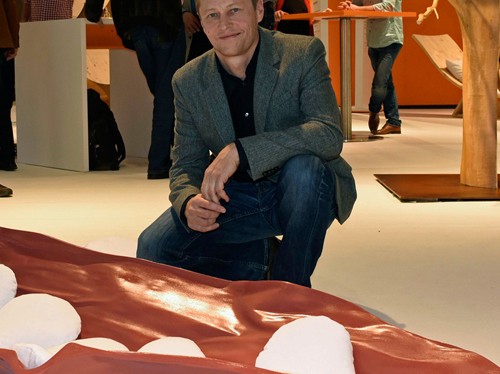
An Honor through Vacuum Technology
A chili as a creative lounge furniture is the winner
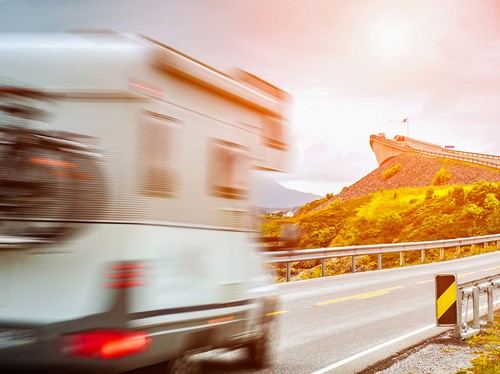
Hymer - a success story with vacuum
The well-known producer works with Columbus
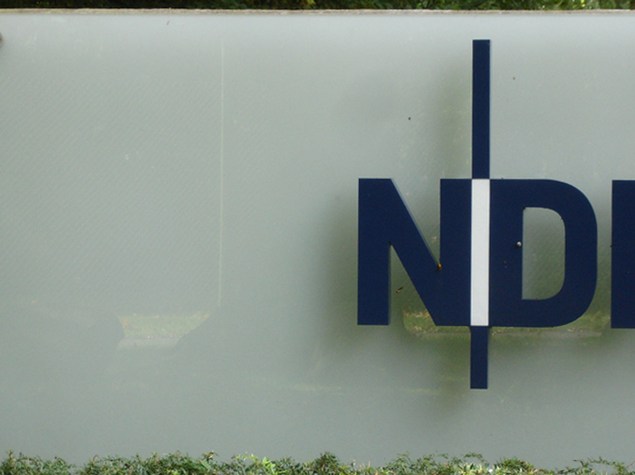
The NDR works with a vacuum press
The Tagesschau desk was produced with Columbus
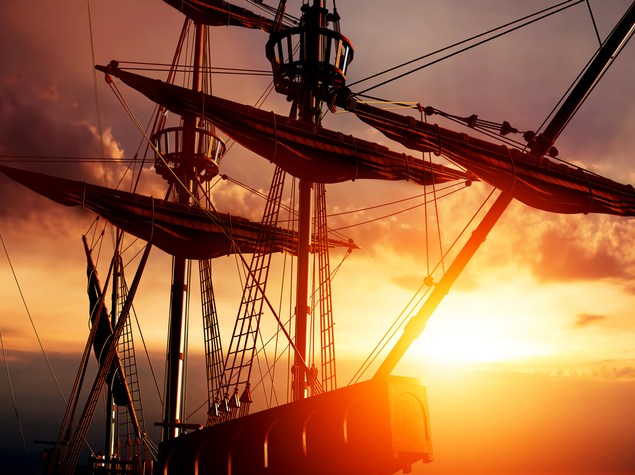
Why we are called what we are called
What Christopher Columbus has to do with Columbus